Table of Contents Hide
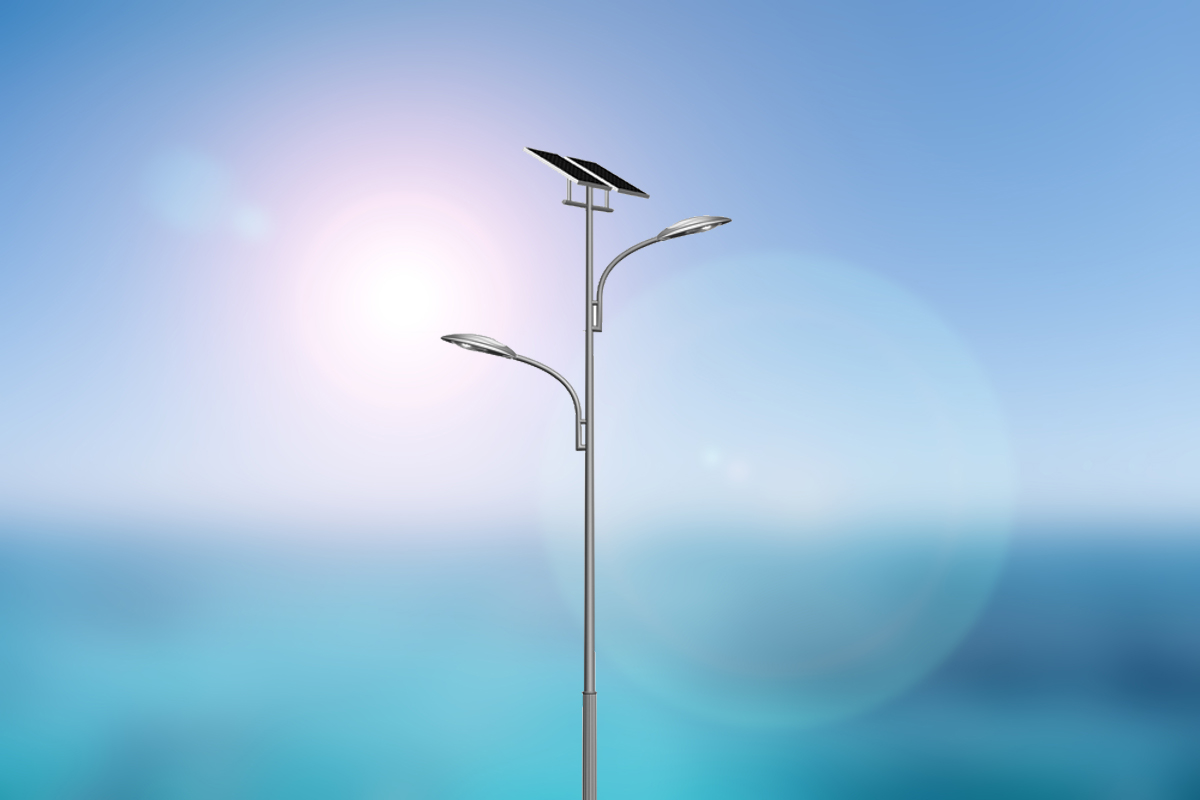
Grid-independent Lighting
A solar street light is an outdoor light fixture that harnesses the radiant energy from the sun to drive its light engine. Whether to create driving visibility, improve traffic safety or enhance pedestrian security, solar street lighting is a practical, simple, and cost effective supplement to grid-tied lighting solutions. The marriage between solar technology and energy efficient, dependable LED lighting takes the sustainability of solar lighting to an unprecedented level. Grid-independent operation eliminates the need for trenching, underground wiring, and connections to the utility grid, making solar street lights the first choice for installations in harsh environments and remote locations where electricity transmission infrastructure is not available or the electrical supply is too costly to connect. No carbon emissions, no energy bills, and minimal ongoing costs. Even in urban areas, these compelling advantages of solar street lights appeal to a number of outdoor lighting applications such as illumination of secondary roads, residential streets, driveways, pathways, parking lots, and building perimeters.Construction
A typical solar street lighting system consists of a solar panel, a solar charge controller, a battery bank, a light assembly, and a light pole or support structure where these components (except for the battery bank in some cases) are mounted. Since there's an irresistible trend towards LED-based solid state lighting, the light assembly further comprises an LED module and an LED driver. The LED driver is oftentimes packaged with the charge controller for the ease of system assembly.Conventional solar street lighting systems are designed and constructed with a discrete architecture in which the solar panel, battery bank and light assembly are remotely located from each other. The use of compact, solid state LED modules and high energy density, small footprint lithium-ion batteries gave birth to solar lighting systems with an integrated architecture, which are known as integrated or all-in-one solar street lights. An integrated solar street light combines all components into a single product. The all-in-one design significantly simplifies installation and reduces cost by eliminating the need for external wiring to remote battery packs and light assembly. The integrated approach also improves system efficiency because long wire runs in solar lighting systems with a discrete architecture often lead to a considerable voltage drop and power loss unless the expensive, large wires are used.
The downside of the fully integrated design is the lack of flexibility in the capacity and tilt angle adjustment of the solar panel, the capacity of the battery bank, as well as the light distributions of the LED module. Furthermore, the LED light engine produces a significant amount of heat that can adversely affect the power conversion rate of the co-located solar panel.
As a result, a hybrid architecture was developed to address the limitation. A solar street light with this type of architecture splits the system into two closely mounted parts: a solar panel and a light head. The solar panel is mounted a rotating support with a tilt mechanism allowing to minimize the angle of incidence between the sunlight and the panel. The light head typically includes the charge controller, battery bank, light assembly and various types of sensors and controls. The hybrid architecture allows the lighting system to provide a scalable offer in light output while enabling optimal orientation and tilt of the solar panel, and accurate light distribution of the light engine.
Solar Panel
The solar panel is a major cost component of a solar street light. The capacity of the solar panel in Watts determines the maximum battery autonomy and light output. The size of the solar panel has a direct impact on the system footprint. The conversion efficiency of the solar panel is inversely proportional to the size of the solar panel. A solar panel is constructed from an array of photovoltaic (PV) modules called solar cells. A solar cell is a semiconductor device that converts light into electricity utilizing the photovoltaic effect. The photovoltaic effect is the creation of voltage and electric current by photons with an energy above the band gap energy of a semiconductor cell with p-n junctions. High energy photons from solar radiation incident upon the surface of semiconductor device create electron-hole pairs in the semiconductor substrate. The electron-hole pairs then migrate to p-doped and n-doped layers of the semiconductor device, thereby generating a voltage differential between the doped semiconductor layers.Most solar cells are based on the p-n junction fabricated from silicon (Si) which is chosen for its semiconductor properties, low cost and wide availability as well as lower band gap energy compared with solar energy packets. Much electromagnetic radiation emitted from the sun is composed of photons with a band gap that sufficiently high to free up extra electrons from silicon atoms for electron-hole recombination. The purity of silicon required for photovoltaic applications is 99.9999% (6N). The 6N silicon comes in two forms: crystalline (c-Si) and amorphous (a-Si). Crystalline silicon is known as bulk wafer silicon. There are two main types of crystalline silicon cells: monocrystalline and polycrystalline. Amorphous silicon is used to make thin film modules.
Monocrystalline solar cells are produced from a single silicon crystal using the Czochralski process. This process yields a large cylindrical ingot by dipping seed crystal silicon into molten silicon and drawing it up very slowly to form a solid crystal structure around the seed. To create cells, the cylindrical ingot is sliced into thin wafers where the epitaxial layer are grown to form the semiconductor junction. Because the wafers are cut from a monolithic-crystal cylindrical ingot, monocrystalline solar cells exhibit a uniform, solid dark blue to black color and come with rounded corners.
Polycrystalline (or multicrystalline) solar cells are fabricated on square silicon wafers sliced from polycrystalline ingots grown in quartz crucibles. Rather than drawing the silicon crystal seed up for a large monolithic-crystal ingot, the molten silicon crystallized around the seed is simply allowed to cool. As such, polycrystalline solar cells made of many small silicon crystals. The presence of different crystal grains of various sizes and orientations gives polycrystalline cells a unique flaky appearance in a lighter shade of blue. The melted and recrystallized silicon crystals can be cast in rectangular prisms, allowing polycrystalline cells to be cut in a distinct square shape.
Monocrystalline solar cells, because of their high silicon purity, have the highest power conversion efficiency of any products on the market under standard operating conditions. The efficiency of monocrystalline solar cells is typically 20% - 25%. However, the complicated manufacturing process leads to the highest production cost among all solar cells. Polycrystalline solar cells, on the other hand, have more irregularities and imperfections than monocrystalline solar cells. Despite a relatively power outputs with efficiencies between 15% - 20%, the manufacturing process for polycrystalline solar cells is less labor intensive than the monocrystalline cells. Compared with monocrystalline cells, polycrystalline cells have a lower temperature coefficient. The temperature coefficient is the rate of reduction in power conversion of a solar cell for every degree the above normal operating temperature (e.g. 25°C +).
Crystalline silicon cells are typically 125 x 125 or 156 x 156 millimeter square. In order to minimize reflection loss of incident sunlight, an anti-reflection coating (ARC) is overlaid on the textured silicon surface. The ARC can be made of silicon nitride, silicon oxide, alumina oxide, or titanium oxide. Photovoltaic cells are connected in series to form a solar panel which provides sufficient voltage to operate a solar street light. The crystalline silicon panel is built in an aluminum frame, fully sealed against moisture ingress, and protected from environmental and mechanical damages, with a protecting layer such as tempered glass or clear plastic cover.
Thin film solar cells are those created by vapor-depositing a very thin layer of semiconductor material on a thin layer of metal, glass, or plastic. The semiconducting absorber layer is much thinner than a human hair, making it possible to produce lightweight and even flexible solar modules. Mass-production of thin film solar panels is rather simple and inexpensive, but the power conversion efficiency of thin film cells, at around ten percent, are far less than that of crystalline cells. Low conversion efficiency makes them space inefficient and results in increased costs of PV equipment (e.g. support structures). Thin film solar panels tend to degrade faster than mono-crystalline and polycrystalline solar panels, which is why they typically come with a shorter warranty.
Thin film cells made from amorphous silicon, the non-crystalline form of silicon, are the oldest and most developed of the thin film technologies and has long been the choice for a variety of low cost and low power applications. Amorphous silicon cells, however, are susceptible to photodegradation and therefore their initial efficiency can deteriorate from 10% to as low as 6% within the first few hours of sun exposure.
Thin film solar cells can also be made from non-silicon materials such as copper indium gallium selenium (CIGS) and cadmium telluride (CdTe). The efficiencies of CIGS and CdTe modules are in the ranges of 10 to 12 % and 8 to 10 %, respectively. CdTe and CIGS thin film panels have a low temperature coefficient, which means they have a more stable conversion efficiency in hot climates than crystalline solar panels. Compared with their competition, these solar panels also have a better performance in shade or low light conditions.
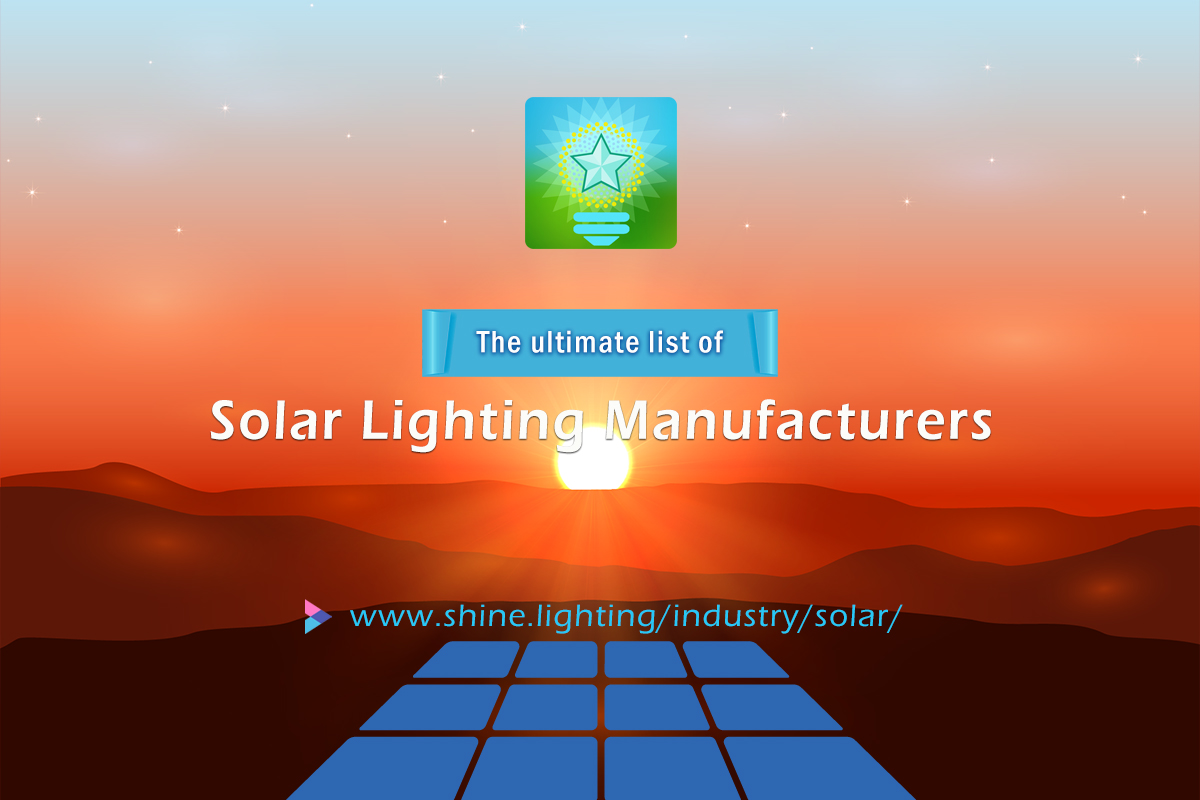
Rechargeable Battery
Batteries are electrochemical cells that store electrical power in the form of chemical energy and then discharge it as direct current through electrochemical reactions to power electrical systems. Solar street lights are very demanding applications for batteries, which are subjected to temperature fluctuations, unpredictable charging, long autonomy periods, and daily cycling. The decision variables in the selection of battery systems for solar street lights include costs (initial purchase, maintenance, shipping, replacement, disposal), lifetime, form factor, cycling capacity, energy density, round-trip efficiency, cold-temperature performance, high temperature stability, capacity in ampere-hours (Ah), cold cranking amps (CCA), state of charge (SOC) over time, self-discharge rate, battery gassing and overcharge reaction. An optimal battery solution also demands a high degree of operational safety and a low environmental impact.Photovoltaic systems use rechargeable batteries for multiple-cycle charge and discharge operations. Some of the chemistries used in rechargeable batteries are lead acid, lithium ion, nickel cadmium (NiCd), nickel-metal-hydride (NiMH). NiCd batteries are one of the most established battery technologies and have advantages such as relatively high energy density (60 Wh/Kg), high mechanical resistance, low maintenance requirement, longer life span, and tolerance for higher discharge. However, this type of batteries is not commonly used in solar powered lighting systems due to their high cost, environmental hazard (cadmium is a toxic metal), high self-discharge rate, and memory effect. NiMH batteries share most of the advantages and disadvantages of NiCd batteries but have a higher energy density (100 Wh/Kg) and contains no toxic metals. However, NiMH batteries have limited applications in solar street lighting because these batteries are not as cheap as lead acid batteries nor as energy dense as lithium ion batteries. Therefore, the two most prevalent battery technologies used in solar street lights are lead-acid and lithium-ion.
While their technology is outdated, lead-acid batteries remain the commonly used energy storage solution for off-grid solar street lighting systems simply because of their price to power ratio is superior to all other battery technologies. As is known, batteries for solar power systems must be of the deep cycle type so as to ensure that they have the ability to be fully charged and discharged. The most recommended deep cycle lead-acid batteries are valve regulated lead acid (VRLA) batteries with an absorbed glass mat (AGM) construction in which electrolyte is suspended in an absorbent glass mat next to the plates. The sulfuric acid electrolyte contains lead dioxide (PbO2) and lead (Pb) which are the positive and negative electrodes respectively when electrochemistry of the battery is in the charge state. In the discharge state the electrodes react with sulfuric acid to form lead sulfate (PbSO4).
Deep-cycle lead-acid batteries have the ability to operate efficiently even at low temperatures and discharge over minutes to days, and in some cases, even weeks. They also have a high overcharge tolerance compared to lithium-ion batteries. These advantages, combined with the low capital cost, trump their low energy densities and low cycle lifetimes. Lead-acid batteries have a cycle life of 1500 - 2500 cycles, a lifespan of 3 - 5 years, a depth of discharge (DOD) or round trip-efficiency (RTE) of 70 - 90%, and an energy density around 30 Wh/kg to 50 Wh/kg depending on the lead density. Lead-acid batteries take between 12 and 16 hours to reach 100% capacity, which is an allowable disadvantage because solar radiation usually lasts for many hours during a day and the slow charge rate allows efficient charging of the batteries.
Lithium ion batteries have the highest energy density and the longest cycle life of all battery chemistries. The lithium-ion battery is a lithium-ion transfer cell in which lithium ions, the working ionic component of electrochemical reactions, shuttle between the anode and the cathode through the electrolyte. In the charge state lithium ions move from the cathode to the anode. During discharge lithium ions move back to the cathode. The electrodes store lithium ions via electrochemical intercalation. Lithium ion batteries are commonly classified by their cathode chemistry. Five types of lithium ion batteries are currently available: lithium iron phosphate (LFP), lithium cobalt oxide (LCO), lithium nickel cobalt aluminum oxide (NCA), lithium nickel cobalt manganese oxide (NCM), and lithium manganese oxide (LMO) batteries. LFP or LiFePO4 batteries, the cathode of which are made from iron and phosphate, has a strong position in solar street lighting applications for their lower cost as compared with other lithium battery technologies.
Lithium ion batteries are typically used in integrated solar street lights which require an energy storage solution with a long cycle life, high energy density and small footprint. In addition to these advantages, lithium ion batteries exhibit qualities such as high DOD, good thermal stability, high charging efficiency, and short discharge time. Lithium ion batteries have a high energy density of 75 - 200 Wh/kg, a cycle life of up to 10,000 cycles over a lifetime of 8 - 10 years, a DOD around 95%, and an RTE of 100%. However, the cost-per-watt ratio of lithium-ion batteries is much higher than that of lead-acid chemistries. Most importantly, Li-ion systems must be correctly designed to avoid serious safety hazards from battery cell abuse and improper operation such as overcharging, overheating, or short-circuiting.
There's three battery mounting options: base mounted, buried or column mounted. Column mounting (including co-location with lighting systems or solar panels) enables greater system efficiency. The buried option provides best protection for the batteries, in particularly with regard to temperature impact. Base mounting allows ease of access to the battery box but leaves the battery prone to vandalism.
Solar Charge Controller
Solar panels are subjected to varying amounts of sunlight (irradiance) and can produce voltages higher or lower than the desired load voltage. The power generated from solar panels is also affected by the variation of temperature upon the photovoltaic cells. With an increase in cell temperature, the operating voltage is dropped and the maximum power point (MPP) shifts to a much lower voltage. Unregulated load voltage can overcharge or undercharge the battery, which leads to reduced charging efficiency or causes damage to the battery. In addition, the battery voltage can vary with state of charge. This will create further inefficiencies if the panel voltage is not adjusted accordingly to match the battery voltage.It's therefore necessary to maintain the MPP under dynamically varying conditions of solar irradiance, cell temperature and shadowing. A charge controller which optimizes the output voltage of the panel to match the required-state voltage level of the rechargeable batteries is used in solar power systems. The controller monitors and regulates the power going into the battery to prevent battery overcharge and maximize the output efficiency. The controller also controls the power coming out of the battery to ensure that the connected loads don't over-discharge the battery. A charge controller is basically a DC-DC converter that has control and feedback mechanisms. Various techniques have been employed to regulate the switches of the charge controller. They can be broken into three categories: simple ON/OFF control, pulse width modulation (PWM), and maximum power point tracking (MPPT). The ON/OFF control is designed to protect the battery from overcharge or undercharge, and prevent reverse current. PWM controls the amount of current charging the battery and provides trickle charging. MPPT is a more advanced approach that is commonly used in solar street lightings systems for high efficiency battery charging.
MPPT charge controllers use sensors, microcontrollers and various sampling algorithms to calculate the highest possible power output and then control a switching circuit to simulate ideal load conditions. The MPPT algorithm communicates with the controller which changes the duty cycle of the converter accordingly to regulate the input voltage to the required load voltage. Current and voltage sensors constitute a feedback system to bridge information about current and voltage values between the photovoltaic panel, the load, and the controller. When the input voltage (panel voltage) is higher than the load voltage, the MPPT charge controller will step down the voltage and simultaneously increase the current delivered to the batteries. Conversely, the MPPT charge controller lowers the charge current to boost the load voltage.
MPPT charge controllers can be up to 97% efficient in the conversion, depending on both the MPPT algorithm and the type of voltage regulation implemented. There are several algorithms available to implement maximum power point tracking, including perturb & observe (P&O), incremental conductance (INC), the constant voltage (CV), open-circuit voltage (VOC), and short-circuit current (ISC). To efficiently perform MPPT under changing irradiance, temperature, and voltage conditions, the P&O and INC algorithms are commonly used in MPPT controllers. Switching regulators employed the DC-DC converters are preferably the buck-boost or the flyback type which can adjusts input voltages higher or lower than the load voltage.
Lighting System
The light engine for solar street lights can be a self-contained lighting system, a combination of light modules, or a light assembly that is directly integrated into the system housing. Whatever the design, a high performance, high reliability lighting system demands a careful consideration in the LED sources and a comprehensive engineering approach that combines electrical, thermal, and optical aspects of the LED system.The light engine of solar street lights can be equipped with mid-power PLCC (plastic leaded chip carrier) LEDs, high power LEDs, chip-on-board (COB) LEDs, or CSP (chip scale package) LEDs. PLCC LEDs such as SMD 3030 and 2835 packages offer a very attractive initial lumen/watt with a system efficacy as high as 200 lm/W. However, the resin-based reflective LED housing and silver plated lead frame are inherently not resistant to chemical contamination and thermal stress. This makes lumen maintenance tremendously challenging. High power LEDs deliver a stable, high intensity light output even at high ambient temperatures and come with an excellent lumen maintenance thanks to their ceramic-based, thermally efficient package architecture. COB LEDs are also high power packages that're capable of pumping out a substantial volume of lumens over a large light emitting surface (LES). CSP packaging eliminates the need for wire bonding, lead frame and plastic housing of PLCC packages, which significant improves thermal performance and package reliability while allowing for a more compact size and reduced cost.
Thermal management is a critical engineering point for LED lighting systems. More than a half of the electrical power supplied to the LEDs is thrown away as waste heat that has to be dissipated from the LED junction. Inefficient thermal management will cause rapid depreciation in light output and shortened lifespan due to degradation of materials utilized in the LED packages (such as phosphor and encapsulant), and nucleation and growth of dislocations in the semiconductor crystalline structure. In integrated street lighting systems, thermal buildup in the light engine can thermally stress the solar panel and result in a reduction in power conversion efficiency. A good thermal design consists of two component: a robust thermal conduction path from the package to the heat sink with high coefficient of thermal expansion (CTE) match between components along the thermal path, and a high capacity heat sink that comes with an excellent thermal conductivity and provides high efficiency convective thermal transfer.
Light produced by LED light engines can be shaped and projected onto the roadway or ground using various types of secondary optics. These optics include TIR lenses, convex glass lenses, reflectors, etc. Optical engineering of street lights aims to improve light extraction efficiency and produce a desired light distribution pattern with excellent illuminance uniformity and minimal glare. Frequently, the optical lenses also serve as the environmental shields for the LEDs. They're typically sealed to the light engine to prevent ingress of dust and moisture. Moisture absorption are known to be one of the primary causes of reduction in interfacial adhesion strength and the delamination in silicone-coated LED packages.