Table of Contents Hide
- 1 What Is High Bay Lighting
- 2 Applications
- 3 Design Considerations
- 4 Legacy Technologies
- 5 Solid State Lighting
- 6 Types of High Bay LED lights
-
7
Light Source
- 7.1 PLCC LEDs
- 7.2 High power LEDs
- 7.3 COB LEDs
- 7.4 CSP LEDs
- 8 Optical Design
- 9 Thermal Management
- 10 LED Driver
- 11 Lighting Control
-
12
Lighting Quality
- 12.1 Illuminance uniformity
- 12.2 Glare control
- 12.3 Flicker
- 12.4 Color rendering
- 12.5 Color temperature
- 13 Ingress Protection
- 14 Dirt Depreciation
- 15 Surface Treatment
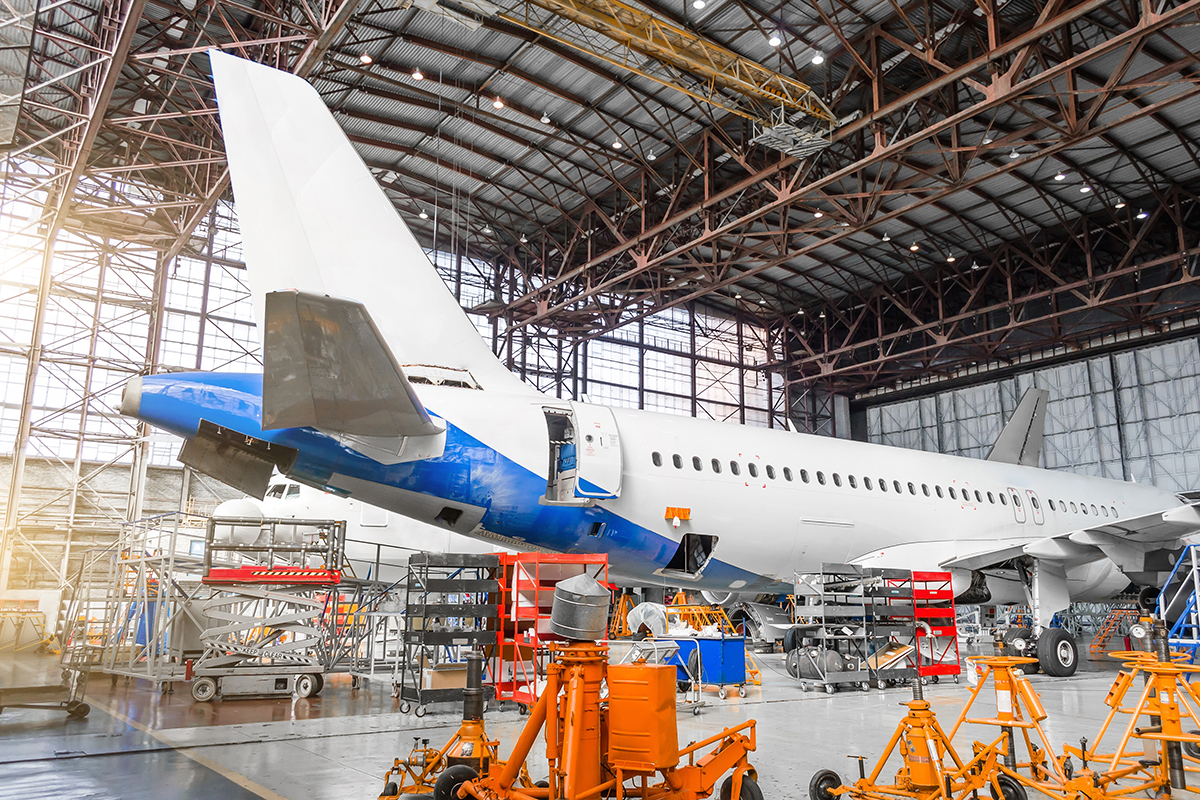
What Is High Bay Lighting
High bay lights are designed for illuminating large interior spaces where the roof truss or ceiling height is greater than 6.1 m (20 ft) above the floor or work plane. The "bay" originally refers to an interior subspace which is formed by a skeletal framework designed for some types of industrial facilities. Yet, in the lighting industry, this term has expanded to include almost any interior space that has a large area to be lit. High bay facilities are generally designed for industrial production, warehousing and storage, indoor sports, big box retail, exhibition and convention. Hard-to-reach ceilings, expansive spaces, harsh operating conditions, and long running hours. These challenges place high demands on the robustness and efficiency of high bay luminaires.Applications
High bay lighting applications are very diverse. Virtually all commercial, industrial, public, sports and recreational facilities with a high clearance between the floor and the ceiling require high bay lighting to provide adequate illuminance.Manufacturing facilities
Lighting can significantly affect productivity and safety in manufacturing facilities. Types of work performed in these areas vary tremendously from production to machining but all need a lighted environment that allows various tasks to be completed at the desired speed with accuracy and safety. Manufacturing facilities represent the largest section of indoor or covered real estate in the industrial sector. A considerable number of these facilities are designed with a high ceiling clearance to accommodate the production requirement. Such production facilities include, but is not limited to, foundries, steel mills, casting and welding facilities, automotive production lines, aircraft assembly lines, machine factories, sheltered shipyards, and all workshops equipped with overhead cranes. In these industrial buildings, powerful illumination is only one of the challenges. Lighting equipment must be made tough enough to resist extreme temperatures, high humidity conditions, corrosive atmosphere, vibration from large machinery, and dirty power.Warehouses and storage areas
Warehouse and storage facilities are found in many commercial, industrial, retail, and logistics environments. These facilities are designed to provide a proper environment for storing goods and materials as well as fulfilling highly diverse tasks such as logistics, inspection, packaging, shipping and receiving, light assembly, and desk work. Depending on the business service requirements and the products to be stored/handled, warehouses and storage facilities can be divided into different types, including open storage, high rise, fixed racking, mobile racking, cold storage, controlled humidity (CH), and special-designed facilities. Loading docks, which are covered shipping and receiving docks for trucks and vans, are also usually a part of warehouses, logistics centers and distribution facilities. Being utilitarian facilities, warehouses require sufficient illumination to facilitate the movement of goods at a high volume and/or high frequency. The never-ending pursuit of low occupancy costs per square foot results in a proliferation of warehouses with increased heights. Warehousing facilities tend to be taller than they were thirty years ago and ceiling heights in these facilities range from a minimum of 24 feet to as high as 80 feet. Aside from providing adequate illuminance for safety and navigation, warehouse lighting is more challenged to provide uniform illuminance on the vertical surfaces of stored goods from top to bottom and along the entire length of storage aisles as the majority of critical visual tasks occur in a vertical plane.Sports and recreational facilities
While large arenas are usually mounted with floodlighting luminaires high around the court perimeter, indoor sports venues intended for Class III and IV play are provided with high bay lighting because of confined spatial conditions. Minimum mounting heights should be less than 6.7 meters (22 feet) for Class III and IV facilities. Gymnasiums, which are generally implemented as part of an educational facility, are illuminated by high hay lights. These indoor facilities play host to different sports and non-sporting activities, high bay lighting should meet the varied or particular requirements for each event. Other sports and recreational facilities with general illumination provided by overhead high bay fixtures include indoor basketball courts, hockey rinks, ice skating rinks, horseback riding arenas, indoor ski resorts, and indoor amusement parks, etc. The challenge in gymnasiums and indoor sports courts lies in achieving uniform, visually comfortable illumination with minimal fixture installations.Convention centers and exhibit halls
These buildings feature virtually column-free, high bay, and long span spaces that require illumination from high lumen lighting systems. Lighting should be designed to provide a substantially uniform level of illuminance across the vast amount of interior floor spaces. As aesthetics are usually one of the basic design elements in modern convention centers and exhibition facilities, it is important for the architectural form of high bay luminaires to blend nicely with the surrounding architecture. High bay lighting should also be able to provide good color rendition of color-critical exhibits.Big-box stores and shopping malls
Also known as a supercenter, superstore or megastore, a big-box store is a physically large, warehouse styled retail establishment with minimal architectural detailing. They're typically windowless, non-partitioned spaces in which the primary task plane is the vertical surface of the racks. It's especially important to provide adequate illuminance towards the bottom of the racks. High CRI light should be provided whenever possible.Passenger terminals
Airport and rail terminals are facilities where passengers embark and disembark. Passenger terminals are usually designed as high bay structures and rely on direct illumination from high bay luminaires to conduct all tasks within the designated areas.Airport hangars
Airport hangars are located on airport grounds and serve as repair and maintenance facilities. These buildings have a scale similar to heavy industrial facilities as they need to be large enough to accommodate an airplane. The ceiling heights of airport hangars can reach as high as 100 feet. This challenges the luminaires' ability to deliver adequate task illuminance from a long distance.Classified areas
Some high bay lights are specifically designed and certified for locations made hazardous by the presence of flammable vapors or gases, combustible dusts, or easily ignitable flying or fibers as defined by the NEC and IEC. These classified areas are typically found in paint manufacturing plants, pulp and paper mills, ammunition facilities, power generation plants, oil refineries, chemical plants, gas processing plants, grain processing and storage terminals.Low bay areas
Sounds strange? In fact the application boundary between high bay and low bay luminaires is ambiguous. Lighting manufacturers usually offer high bay luminaires in a range of wattages, including those designed for low bay facilities such as grocery stores, mechanic shops and multi-storey industrial buildings. High bay and low bay luminaires are generally designed and constructed in the same way, except that the lumen package and optical design of low bay luminaires are tailored for low mounting heights. The light distribution pattern of low bay lights is optimized for a spacing-to-mounting ratio greater than 1.5. Low bay lights may also come with tighter glare control when a higher level of visual comfort is necessary.Hose down areas
High bay lights can be constructed with hose-down capability for applications where luminaires are subject to routine high-pressure washdown with water and/or sanitation chemicals. This type of luminaires is typically found in food-processing facilities, cleanrooms, car washes, livestock or poultry buildings, and commercial kitchens.Design Considerations
The unique physical characteristics and operating conditions of industrial, commercial and sports facilities distinguish high bay lights from other types of indoor luminaires. Many issues enter into design and specification decisions for high bay lighting.Energy efficiency is especially a priority in high bay applications due to the sheer number of luminaires required to cover the expansive space and relatively high wattages typically involved to deliver adequate illuminance from a high mounting height. With energy costs on the rise, an inefficient facility is at a competitive disadvantage when lighting becomes a drain on resources and fails to comply with ever-changing energy codes.
A tremendous opportunity remains to maximize energy savings by operating high bay lights with lighting controls. The ability of a light source to interact with lighting controls and energy management systems has gained increasing attention. The light source must have instant start/restrike and dimming capabilities so that its light output can be controlled in a very dynamic way in step with digital or analog control signals. As the industrial internet of things (IIoT) is ushering in a new era of lighting automation, controllability should be prioritized as one of the key capabilities of a lighting system.
The photometric performance of a luminaire is often overlooked by end users. However it can significantly impact the quality of illumination and the practical value of a luminaire. Photometric performance can be defined as the efficiency and effectiveness with which a luminaire delivers light to an intended target. High light source efficacies should not be equated with high luminaire efficacies. Legacy technologies can offer a relatively high source efficacy of up to 120 lm/W. However, the omnidirectional emission pattern of HID lamps will result in an optical loss as high as 30% when the light source is integrated into a lighting system.
It is worth noting that a high optical efficiency doesn't necessarily translate into effective use of the light collected by the optical system. The optical design for HID luminaires, for example, causes a concentrated distribution of illuminance directly below the luminaire and a much low density of low illuminance around high intensity "hot spot". Non-uniform distribution of illuminance may distort visual perception of moving objects, which can be a hazard factor or affect task performance. Poor uniformity commands continuous eye adaptation between two significantly different luminance levels physically adjacent to each other when multiple luminaires are installed to illuminate an area. The need to perform high frequency visual adaptation between different vision states can cause eye fatigue. Maintaining uniformity between adjacent areas of luminaires with a high uniformity ratio may be wasteful of energy and increase cost because a higher fixture density is required to compensate for the poor uniformity.
The importance of longevity should run parallel with energy efficiency and photometric performance as the maintenance and relamping costs associated with high bay lighting are very high. The reliability of a luminaire will be determined by all its constitutive parts and their survivability under environmental and operational stresses. A long lifespan light source is critical to the long service life of a lighting system. Yet the design and engineering of the platform where the light source runs on should be paid extra attention to. High bay lights for industrial applications need to operate reliably in hostile environments where there can be presence of extreme temperatures, moisture, vibration, impact, dust, dirt and corrosive elements.
Legacy Technologies
Conventional high bay systems employ metal halide, linear fluorescent, compact fluorescent (CFL), or induction fluorescent lamps as the light source. What make these technologies obsolete are their low luminous efficacy, use of hazardous mercury, and limited lifespans (with the exception of induction lamps). Among these light sources, metal halide had been favored in high bay applications for its ability to operate at a high wattage of up to 1,000 watts and a comparatively high source efficacy. While lower wattage metal halide bulbs may last as long as 20,000 hours, higher power bulbs typically have a life expectancy drastically reduced to several thousand hours. Another concern is long startup and hot restrike times. In particular the long restrike interval can be a serious issue for facilities that require uninterrupted lighting. Poor startup and restrike performance, along with the restrictive dimming capability, makes metal halide lamps outmoded in the era of digital lighting. While envelope failure (bulb explosion) is not common, it is of major safety concern since the hot quartz from a broken bulb may ignite flammable gases or vapors, combustible dust, ignitable fibers or flying that can be present in industrial environments. As previously noted, metal halide high bay lights have a frustrating illuminance uniformity since HID bulbs are high-intensity nearpoint sources. This is a serious application disadvantage when it comes to indoor lighting. On the other hand, fluorescent systems produce diffuse lighting that delivers a better uniformity. However they're limited to mid-bay and low bay installations due to their low system lumen output.Solid State Lighting
A light emitting diode (LED) is a semiconductor device that generates light through the recombination of electronic carriers (electrons and holes). This operating principle differentiates LEDs from traditional light source and lends LED high bay systems many advantages over traditional lighting solutions: high power conversion efficiency, excellent controllability, high photometric performance, spectral versatility, long lifespan, solid state durability, and compact size.The industrial sector has been the most steadfast advocate of energy efficient lighting, which is the most breathtaking part of LED lighting technology. LEDs provide more than twice the luminous efficacy (lumens per watt) of metal halide lights. The energy efficiency advantage of LED lighting is exhibited not only in its high efficiency energy conversion from electrical power to optical power, but also in its superior photometric performance and ability to be seamlessly integrated into various lighting control strategies. The direct nature of LEDs results in highly controllable optical systems. The miniature packages are typically assembled in arrays to form a large light emitting surface (LES), which allows extremely uniform illuminance and tight control of light when the LEDs are mated with tailor-made secondary optics. High illuminance uniformity and precise lumen delivery translate to maximal utilization of light emitted by the light source and contribute to comfortable visibility. Maximized luminaire spacing as a result of high uniformity illumination produces an economical installation. The energy efficiency potential is not fully exploited until lighting controls are used to operate the LED luminaires. Up to 50% of energy consumption can be saved when lighting is automated based on time-based triggers, threshold-based events or a combination of the two.
The economics of lighting is determined by luminous efficacy, optical efficiency, power consumption, first cost, and service life. LED technology provides a viable solution to addressing the first three variables, but leaves the industry struggling in the painful trade-off between the first cost and service life. Although the rated service life of LEDs is projected to be from 50,000 to as much as 200,000 hours, this doesn't imply that LED luminaires will logically last that long. LEDs are current driven, self-heating light sources. Their intercorrelated electrical and thermal characteristics add complexity to system design. In order for the LEDs to perform optimally over their rated life, tight load regulation and effective thermal management are two critical specifications that should be prioritized in the design and engineering of LED luminaires. As a result, the use of high capacity heat sinking devices and high performance driver circuitry considerably drive up the cost of high wattage LED lighting systems.
An economical high bay lighting system is one which, when the first cost, operating cost, maintenance cost, lifespan, and system performance are all considered, provides the greatest practical benefits for the least total cost. Despite the high product cost, high efficiency operation over the long lifespan of a properly engineered LED luminaires creates a return on investment (ROI) that is significantly higher than legacy systems. Unfortunately, not all people interpret "economical" this way. It's very common that quality is overlooked and the primary criterion for product selection is low price. Consequently, the market is flooded with cheap and crappy products of which the reliability, light quality, efficiency, and even safety are oftentimes compromised. Typically, these products use non-EMC plastic LED packages, bare-bones driver circuits based on linear power regulation or simple switching regulation, and inadequately engineered thermal management systems.
Types of High Bay LED lights
High bay LED lights are designed in various forms to serve different application scenarios or to deliver specific features. There're primarily three types of designs: round, linear and modular.Round high bay lights
Round high bay lights have evolved from traditional style luminaires, which feature a cylindrical heat sink, a top-mount electrical box and a large aluminum reflector, to low profile luminaires in a sleek, aesthetically pleasing style. This type of luminaires are commonly known as UFO high bay lights simply because their shape looks like a disc. UFO high bay lights were by no means designed just to achieve a sleek architectural look. It's the board-style design of LED module that makes the low profile heat sink design a necessity. The disc-shaped heat sink provides an increased surface area for accommodating an LED module with a large LES that facilitates more uniform distribution of light. Maximized thermal distribution area allows the waste heat generated from the LED array to spread quickly across the heat sink. The heat sink, which simultaneously functions as the luminaire housing, is constructed of die cast or cold-forged aluminum. The LED module is an assembly of LEDs which are mounted on a metal core printed circuit board (MCPCB). A lens array is indexed to the circuit board to regulate luminous flux from LEDs when a controlled beam spread is desired. The ability to control light emitted by LEDs with miniature compound lenses allows high bay luminaires to eliminate the bulky aluminum reflector. The LED driver is located in a separate aluminum enclosure or a thermally independent compartment.Linear high bay LED lights
Linear high bay LED lights consist of two categories: traditional style LED luminaires that follow the footprint of traditional two-to-eight lamp T5/T8 fluorescent fixtures, and highly integrated linear LED fixtures with a heavy duty housing and more rugged construction. Traditional style linear LED high bays come with a housing constructed from extruded aluminum or die-formed, cold-rolled steel. The light assembly consists of a number of lumen maintenance trays which mount linear LED strip modules and direct light at the desired beam angle to accommodate facility needs. Integrated linear LED fixtures are in most cases designed for racked/aisle environments, although high bay open area applications are also well served by this type of fixtures. These fixtures have an extruded aluminum housing that provides mechanical strength and heat sinking. The linear light assembly is comprised of one of more LED modules, depending on the fixture length. The LED module has an array of LEDs mounted on a rectangular circuit board. Light produced by the LEDs is regulated by a one-piece lens array. The LED drivers of linear high bay lights are mounted to a gear compartment which is integrally constructed with the housing but is thermally isolated from the light assembly.Modular high bay LED lights
Modular high bay LED lights provide scalability in light output, versatility in light distribution, continuity and flexibility in lighting design. These fixtures are assemblies of modular LED engines and externally mounted drivers. A modular LED engine is a self-contained LED system that is thermally managed, environmentally protected and optically regulated. However, the power supply is not built into the system, instead it's powered by drivers located in a backmount gear box. The housing/ heat sink is made of either die cast aluminum or extruded aluminum. The LED assembly is constructed the same way as that of UFO or integrated linear high bay luminaires.Light Source
The pc-LED (phosphor-converted LED) architecture is by far the dominant white light architecture used in general lighting applications. In this type of LEDs, white light is produced by pumping yellow and red wavelength optical down-converters with a blue InGaN LED chip. During the light generating process, a substantial amount of electrical energy is wasted and converted to thermal energy which needs to be dissipated from the LED chip. Bare LED chips are prone to performance degradation or aging if exposed for a long time in an unfriendly atmosphere. Therefore, an LED chip must be enclosed in a package capable of providing phosphor conversion and light extraction, protecting from extrinsic damages, and thermally, electrically and mechanically interfacing the LED to its operating environment. The design and materials of package into which the LED chip is assembled establish the performance, efficiency, and reliability of the light source. Selection of LED packages is every bit as critical as the design and engineering of lighting systems. LEDs are available in four main package platforms: mid-power packages, high power packages, chip-on-board (COB) packages, and chip scale packages (CSPs).PLCC LEDs
Mid-power packages that follow the standard nomenclature for SMT packages such as 2835, 5630, 3030, 3535, 3014, 4014, etc. are built on the plastic leaded chip carrier (PLCC) platform. These plastic LED packages have a controversial but widespread presence in the realm of high bay lighting. High bay lighting manufacturers take great interest in plastic LED packages as these products have incomparable cost and efficacy advantages. PLCC packages have a fully developed manufacturing ecosystem, a leading market share, and a low material cost. These attributes make PLCC packages the most affordable LEDs and, to a large extent, pushed the massive migration of lighting technology from HID and fluorescent to LED. The construction of mid-power packages is supported by a molded plastic housing and silver-plated lead frame. It's the highly reflective plastic housing and leadframe plating that contributes to the high luminous efficacy of mid-power LEDs. Nevertheless, the plastic resin is prone to degradation under high temperatures, and leadframe plating is at high risk of corrosion when exposed to an atmosphere containing chemically active substances such as sulfur compounds. In high bay lighting applications the light source typically operates under high thermal and electrical stresses. Although the initial lumen/watt of mid-power LEDs can look attractive, fast lumen depreciation and color shifts often occur on mid-power LEDs because of their low resistance to high temperatures and drive currents. Despite the use of more thermally stable epoxy molding compound (EMC) as the housing material and more thermally efficient Quad Flat No-lead (QFN) anode/cathode pads, high bay lights that incorporate mid-power LEDs require careful design and stringent engineering in order to protect the vulnerable light source from damages of high thermal, electrical and environmental loads typical of industrial lighting.High power LEDs
High power LEDs which are built on a metallized ceramic substrate enable high lumen LED designs that are not possible with mid-power LEDs. Ceramic LED packages eliminate the use of plastic resin and lead frames which are the main failure factors of mid-power LEDs. High thermal and chemical stability of ceramics allow high power LED packages to thrive in harsh operating conditions. Aside from using high thermal conductivity dielectric material, high power LEDs typically come with a 3-pad (an anode pad, a cathode pad and an electrically insulated thermal pad) design and an array of thermal vias. These design elements combine to create a high capacity, high reliability thermal conduction path that allow the LEDs to perform optimally at high junction temperatures of up to 150 °C with no drastic reduction in rated lifetime. While cheap mid-power LEDs have been aggressively encroaching on the high power lighting market, high power LEDs generally offer a considerably better ROI than the plastic packages in high lumen lighting applications because of their excellent lumen maintenance and high color stability. In high ambient temperature industrial environments such as steel mills and foundries, high-power LEDs are the only viable option.COB LEDs
Chip-on-board (COB) LEDs are integrated LED arrays capable of producing a high volume of lumens from a single package. This feature makes it a popular light source for traditional style round high bay LED lights which have a limited space to accommodate the light source. Multi-die design allows COB LEDs to produce homogenous illumination, which eliminates the need for expensive secondary optics. However, either a bulky reflector or a high cost optical system is required to shape the beam spread of high power COB LEDs when high bay lighting demands an accurately controlled light distribution. While the diodes within a COB package are die-bonded onto an MCPCB or a ceramic substrate for high efficiency package-to-board heat dissipation, the electrical path to the individual diode which is created using wire bonding can be a failure point under an electrical overstress (EOS). COB LEDs are not advantageous in cost and luminous efficacies when compared with mid-power LEDs, nor are they comparable to high power LEDs with regard to resistance to thermal and electrical overstresses. It's logical that this type of LED packages has a shrinking share in the high bay lighting market.CSP LEDs
Chip scale package (CSP) technology significantly reduces failure factors in LED packages and drives down the packaging cost by stripping superfluous packaging elements such as plastic submounts, ceramic substrates, lead frames, and bonding wires. The majority of current CSP packages are built on flip-chip dies, onto which the phosphor and encapsulant are applied. The P and N contacts are directly metalized on the bottom of the bare die. Delivering performance and reliability comparable to high-power LEDs at a cost that is significantly lower than mid-power LEDs, CSP LEDs are deemed to become a top performer in the market and re-define LED lighting.Optical Design
High bay facilities have widely varied requirements on light distribution. In some applications high bay luminaires with exposed LEDs can serve the lighting task very well, yet in some applications precision designed secondary optics are used to regulate luminous flux from the light source and deliver uniform illumination to a specified target area. The use of aluminum reflectors, once a standard optical component for HID and traditional style LED high bay luminaires, has gradually diminished. There have been very limited applications of reflectors in modern LED systems, their role is only to shield the LEDs from direct view, reduce glare and screen off spill light. Modern high bay LED systems are typically designed with a light module that has an array of LEDs distributed over a large circuit board. A large parabolic reflector will only control the light that is incident on the reflector surface, a large part of the emitted light from the LEDs doesn't interact with the reflector. Refractor shades remain an optional light control device for modern high bay systems. Made of acrylic or polycarbonate, refractors take advantage of two-or three-dimensional prisms to control directions from which light leaves a luminaire. Refractors can be used to obscure source images for a softer lit appearance, widen the beam produced by the luminaire, and enhance vertical illuminance distribution. Diffusers are mainly used in traditional style linear high bay fixtures to diffuse luminous flux from LEDs evenly to all directions for a uniform light distribution and enhanced visual comfort.High bay LED lights are typically equipped with one-piece injection molded lens arrays to control light with the precision previously unavailable with bulky reflectors. LED lens arrays can be custom molded to fit tightly over the LEDs and use single or multiple optical elements to extract and control virtually all of the light produced by the light source. TIR optics are a type of compound lenses that capitalize on characteristics unique to LEDs. This type of optics combines refraction and reflection to maximize the beam shaping capabilities and minimize optical loss. Precision molded lens array allows the beam produced by every LED to radiate out in any desired beam angles and to produce asymmetric or double asymmetric distributions for the directional lighting of vertical surfaces such as high racks and store shelves. Most of the LED lens arrays are manufactured of PMMA (acrylic) which is economically sensible and has superior optical properties. PC (polycarbonate) is the secondly most used lens material.
Because LED lenses usually sit close to the LEDs, thermal stability of the optics should be factored into lens design considerations when high drive current and high flux density operations are involved. The temperature at the phosphor layer is higher than junction temperature as the process of photoluminescence produces a significant amount of Stokes heat. Polycarbonate resin which can tolerate high temperatures of up to 120°C offer a higher thermal stability compared to acrylic which is rated to operate under 90°C. However, in some high power systems phosphor down-converter temperatures can approach 150° C. This may demand lenses with higher thermal stabilities. Silicone lenses with a maximum permanent operating temperature 150°C may be used to handle high temperature conditions. In extreme conditions glass which is temperature stable up to 400°C or aluminum reflectors can be a more reliable and cost effective solution.
Thermal Management
Thermal management is critically important for high bay lighting systems to achieve the reliability expected from LED lighting and push the boundary of lighting performance. LED lighting involves two light generation mechanisms: electroluminescence and photoluminescence. The processes that enable electroluminescence and photoluminescence in LEDs are also two major sources of waste heat. More than half of the electrical energy fed into LEDs is converted to heat. The waste heat remains trapped within the LED package and must be conducted away from the LED die at a rate that outpaces the load rate to prevent a buildup of heat. Excess heat buildup will raise junction temperature and cause the LEDs operate beyond its thermal tolerance. Many failure mechanisms in LEDs are temperature-dependent and they eventually leads to irreversible lumen depreciation, color shift, and even premature failures. Typically, high temperature operation can spur nucleation and dislocation growth in the active region, cause permanent degradation in phosphor conversion efficiency, and accelerate the kinetics of discoloration in encapsulant, plastic housing materials and optical lenses. Continuous operation of an LED beyond its maximum rated junction temperature will result in a drastic reduction in the useful life of the LED (30 - 50 % decrease in LED life for every 10°C increase in junction temperature).The objective of thermal management is to build a thermal transfer path dimensioned to outperform the maximum applied power load. Thermal design for a high bay LED luminaire begins with the selection of light source. High-power, COB and CSP LEDs are more temperature stable than mid-power PLCC LEDs. They are packaged on low thermal resistance platforms that allow efficient extraction of heat from the LED junction. Mid-power LEDs are highly sensitive to thermal stresses as their packaging materials are prone to thermal degradation. Thermal conduction from semiconductor junction to system PCB can be the weakest part of the thermal path in lighting systems that incorporate mid-power LEDs. Whatever the type of LED packages used, effective thermal management calls for high reliability, and high operating temperature capable interconnects between the LEDs and the circuit board. Many catastrophic failures occur at the interconnection level. In addition to providing adequate resistance to high thermal, electrical and mechanical loads, solder interconnects should be engineered to provide a high coefficient of thermal expansion (CTE) match between the package and PCB so as to avoid failures due to strains incurred in thermal cycling.
System-level thermal management for high bay luminaires handles the thermal resistance from the PCB through the heat sink to the ambient. Thermal design at this level revolves around maximizing material thermal conductivity, heat transfer surface area of the thermal path, and the amount of fluid flow (e.g. air) across the surface area. The rate at which heat is transferred depends on the conductive and convective cooling capacity of the thermal path, which typically consists of a metal core PCB where LEDs are mounted, a thermal interface material (TIM), and a heat sink. The most common MCPCB construction consists of a copper layer on top, a high conductivity dielectric layer beneath, and an aluminum or copper substrate at the base. The MCPCB must meet the minimum high potential (hipot) test requirements while providing high thermal conductivity and stability such that the board can continuously serve in a high temperature condition. The TIM, which can be a grease, epoxy, or pad, is placed between the MCPCB and heat sink to minimize the interfacial thermal resistance.
The heat sink, which additionally serves as the luminaire housing in UFO type luminaires and integrated linear fixtures, is the last and most influential part of the thermal management system. It is designed to provide a high thermal mass by using an adequate volume of materials that have high thermal conductivities. A maximized surface area in physical contact with the heat source directly or through TIMs facilitates heat spreading across the heat sink. Heat sinks can be designed for either natural convection (passive cooling), which utilizes free flow of air around the luminaire to cool the heat sink; or forced convection (active cooling), which relies on an external mechanism to provide additional cooling capacity. For passive heat sinks to perform to their full capacity, it's critical to maximize the surface area of the boundary and deploy an effective aerodynamic design. Geometry is a significant characteristic of the heat sink. Aim of the geometry design is to bring design aesthetics to the luminaire, increase the rate of natural air circulation, and maximize convection surface area. Cooling fins are often designed to capture as much airflow as is possible and increase surface area while allowing the luminaire to remain confined to a given footprint.
Heat sinks for high bay luminaires are produced by casting, extrusion, or forging. Aluminum is the most commonly used material for its cost-effectiveness, high thermal conductivity and excellent processability. Aluminum die casting is capable handling complex geometry that enables superior aerodynamics. Other factors that come into play include high dimensional stability, excellent corrosion resistance, precise dimensional consistency, good surface finishability, and low production cost. Despite a comprise in thermal conductivity (90 - 120 W/mk) due to the use of alloy elements, aluminum die casting delivers the best value for money as well as exceptional design flexibility. When the heat sink demands a thermal conductivity beyond 120 W/mK, cold forging and extrusion processes can fulfill the requirement. Aluminum extrusions made from 6xxx alloys offer thermal conductivities as high as 215 W/mK. Cold forged aluminum heat sinks which offer a thermal conductivity of up to 240 W/mk provide superior passive cooling.
Whenever possible it is always best to use passive heat sinking because it's reliable and noise-free. When the thermal load of an LED system is too high and natural convection is insufficient, active cooling may be the only solution. With forced convection provided by fans, blowers, heat pipes, liquid cooling, Peltier devices or synthetic jet cooling, the heat transfer coefficient can be drastically improved. However, very few active cooling devices can last as long as the long lifetime of LEDs. The effectiveness of active cooling devices should be weighed against the reliability, noise, cost, additional power consumption (and thus lower system efficiency) and maintenance of these devices.
LED Driver
A high bay LED light, to a large extent, is only as good as its driver. LEDs are forward biased, current-sensitive devices and their light output is proportional to the current flowing through them. An accurate constant current control is required to ensure the light output remains constant regardless of changes in the supply voltage or forward voltage. High bay LED systems are operated by constant current drivers which employ a feedback mechanism to maintain the desired current level. Typically, the driver is designed as a switching power supply (SMPS) which transforms incoming power supply into pulse current by switching a pass element, such as a MOSFET, between its full on (cut-off) or off (saturation) regions at a high frequency. This mode of load regulation allows drivers to be designed with minimal power loss, high quality light output, superior dimming functionality, universal input voltage capability, and galvanic isolation. SMPS LED drivers are the only sensible option for medium to high power solutions which can't afford a low power efficiency.The SMPS is technically complex solution to LED current control because it generates the predetermined magnitude of DC power through a high frequency switching operation. And it involves the use of reactive components, capable of storing and converting the electrical energy and reducing the ripple in the LED current, such as oscillating coils and electrolytic capacitors. Switching regulation introduces a potential source of EMI (electromagnetic interference) noise that has to be suppressed by filtering coils and high voltage capacitors. The driver is connected to the AC mains through a power factor correction (PFC) circuit which shapes and time-aligns the input current into a sinusoidal waveform in phase with the source voltage while also reducing total harmonic distortion (THD). Output protection such as over-current and short-circuit is implemented on power supplies to protecting both the driver circuit and the load from excessive current. Operating a power supply in a constant current mode requires protection against overvoltage triggered by various events such as switching operations/load change on the power grid, lightning strikes nearby, and electrostatic discharge. The drivers are furthermore equipped with over-temperature protection (OTP) to minimize the risk of thermal overload due to operation of the LEDs with high load or insufficient cooling.
The steep cost and complexity of full featured SMPS driver solutions remain one major bottleneck in bringing high performance LED systems to high bay lighting applications. While cost optimization of SMPS drivers is a continual effort, the market is being tempted by a low cost alternative - linear power supplies, despite the fact that the SMPS provides fundamental advantages. The linear power supply is simple and cheap because it regulates the DC power on resistive loads without relying on bulky and expensive reactive components. Absence of EMI radiation eliminates the need additional circuits which can double the overall cost of the LED driver. Linear power regulation allows driver-on-board (DOB) design which significantly scales down the size of a luminaire. The linear design, however, is extremely inefficient because operating in this mode means that there is always a headroom (dropout) voltage - the minimum input-to-output voltage differential required for regulation. The headroom voltage is thrown away during linear regulation, which causes the power supply to have a low efficiency. The waste power is dissipated as heat which produces additional thermal stress to the LEDs in DOB systems. For high bay systems that are designed to produce a high volume of lumens, this headroom loss means a huge economic loss that can be not be compensated by the savings in the equipment cost. Furthermore, it is impossible to build universal inputs and accomplish galvanic isolation with linear power supplies.
Lighting Control
Lighting controls are designed to maximize energy savings, support flexibility of use of a space, and provide a safe, comfortable environment for all building occupants. LEDs provide instant light and react instantaneously to changes in the forward current, lending them perfectly to various lighting scenarios. Along with advanced light management came the demand for better dimming characteristics. Of LED drivers that provide dimming, pulse-width modulation (PWM) and constant current reduction (CCR) are the most common dimming methods. CCR, which is sometimes referred to as analog dimming, operates by adjusting the current flowing continuously through the LEDs. Analog dimming circuitry may be controlled through various protocols, including 0-10V, DALI and ZigBee. PWM dimming is implemented by driving the LEDs with full amplitude pulses of current. The brightness is controlled by varying the width of the pulses. PWM dimming is often preferred over analog dimming because it keeps the forward current constant, thus the CCT of LEDs is maintained regardless of dimming level and light output can be accurately controlled. However, PWM operation may generate EMI from the high frequency switching, which makes it not suitable for certain applications. LED lighting may also be controlled in a traditional way, such as phase control dimming (leading edge, trailing edge) which operates by cutting out a portion of the AC waveform to limit the amount of voltage and current supplied to the luminaire.The inclusion of controls, such as daylight harvesting controls, occupancy sensors, time clocks, and energy management systems, allows the operation of high bay luminaires to be automated with various levels of adaptation. High bay LED lights in modern facilities are typically operated by a networked control system and may hold intelligence within one server or may broadly distribute intelligence via programmable chipsets that are embedded in the luminaires. The network-based solution may provide stand-alone, group and centralized control of luminaires via web-based or mobile applications. Adding networking capabilities, processing power and memory to high bay luminaires with automated intelligence creates an intelligent lighting solution that transforms lighting from a fixed expense to a strategic asset.
Lighting Quality
Lighting design for high bay facilities requires a great deal of information about the tasks to be performed in the space. For a lighting design to support a safe, comfortable, functional and productive environment, it is important to review the spectral quality and optical control of the light source, and modulation in light. The source-dependent factors that determines the quality of lighting include illuminance uniformity, glare control, flicker, color rendition and color temperatures.Illuminance uniformity
High bay lighting is intended to provide substantially uniform illumination throughout an area. Uniform horizontal illuminance is important for task visibility, material handling and general circulation. Most industrial, retail and Class III sports facilities require an average uniformity ratio of 3:1 or less. A high bay luminaire that provides very uniform distribution of light will contribute significantly to good visual conditions and wide luminaire spacing. The illuminance uniformity of high bay LED luminaires can be improved by spreading LEDs in an optimal pitch over a large circuit board and distributing light emitted from LEDs uniformly through precision designed compound lenses.Glare control
LEDs are directional light sources that concentrate luminous flux on a small LES. This optical characteristic makes LEDs inherently harsh and leads to an increased glare profile of LED luminaires. Extremely high sensation produced by luminances within the visual field can cause discomfort, reduction of visibility, and even momentary loss of vision. One of the goals of optical control to soften the harshness of LEDs and reduce the size of the light source's solid angle from which the source can be viewed directly. High bay luminaires are typically less demanding in glare control because their high mounting heights produce a small solid angle. However, for low bay applications specialized secondary optics will be needed to reduce direct glare.Flicker
The flicker produced by LED luminaires can be a function of how well the driver converts AC electricity to low ripple current. Most LED drivers are able to filter out large ripple that is responsible for low frequency light flicker noticeable to the human eye. However, even if flicker is not visible at higher frequencies (above 80 Hz), it can be perceived by the human brain produce negative effects on health, such as eyestrain, blurred vision, impaired visual task performance, headaches or even seizures in extreme cases. Residual ripple that causes high frequency flicker can be reduced with output filter capacitor. However, low cost driver circuits usually do not include high capacitance ripple suppressors. In general, 10 percent flicker or less at 120 Hz, or 8 percent flicker or less at 100 Hz is considered safe for all but the most sensitive populations.Color rendering
Color rendering is the general expression for the ability of a light source to faithfully reproduce the colors of an object. As expected, the cost and efficacy often weigh against the color quality of the light source for industrial and commercial lighting. LEDs with a higher color rendering performance are more expensive and less efficient than those with a lower color rendering performance. As such, most LEDs for high bay lighting applications come with a color rendering index (CRI Ra) of around 80. However, for color-critical applications the light source may require a minimum CRI Ra of 90 of or a high score of saturated colors from R9 to R12, particularly R9 (for red color rendering) that's often left out in low cost LEDs.Color temperature
Color temperature is metric that relates color appearance of a white light source. High bay lighting is typically provided with a correlated color temperature (CCT) in the 4000 K - 5500 K range. This is because the higher percentage of blue in high CCT light sources can stimulate the occupant to alertness and activity, thus enabling them to stay alert and productive. The relatively higher amounts of blue wavelengths also stimulate the ipRGC photoreceptors to contract the pupils of the eye, which results in better visual acuity in low luminance conditions (mesopic vision). The correlation of spectral distribution and visual acuity can be described by the scotopic/photopic (S/P) ratio. A light source with a high CCT carries higher S/P value, which relates to a good visual performance in mesopic vision. LEDs with a CCT in the 6000 K - 6500 K range are heavily promoted in some markets because of the preference inherited from fluorescent lighting, higher efficacy and relatively lower manufacturing cost of these LEDs compared with low CCT LEDs. However, light emitted by the 6000 K - 6500 K LEDs contain an excessively high percentage of blue wavelengths. Ill-timed or prolonged exposure to high dosage blue-enriched white light can lend occupants to circadian disruption and photobiological reactions in the retina.Ingress Protection
The LED optical system of high bay LED lights, whenever economically feasible, should be sealed with a high IP rating, e.g., IP65 or above, to prevent ingress of moisture and contaminants such as dust, dirt and other particulates. The electrical compartment or driver box should be sealed to at least IP54. Silicone is the most widely encapsulant for LED packages due to its high thermal and chemical stability. However, its large coefficient of thermal expansion (CTE), high moisture and gas permeability make LED packages prone to moisture-polymer reactions especially in the presence of heat and humidity. Moisture can diffuse into the encapsulant and lead to hydrothermal ageing of silicone and delamination at the chip/phosphor interface, which in most cases is accompanied by color shifts and ends up in premature failure. For luminaries that is gasketed at all housing interfaces to achieve high watertight integrity, it is important to equalize pressure differentials inside and outside sealed enclosures, which would otherwise put extreme stress on the housing seals and cause the original IP level to degrade over time.Dirt Depreciation
The use of polymer optics has raised an issue of concern with regard to Lamp Dirt Depreciation (LDD). The depreciation rate of LED luminaires equipped with exposed polymer optics is 3% versus 0.9% per year for systems gasketed with flat glass outer optics. High bay luminaires are typically mounted at hard-to-reach heights and are expected to operate up to ten years with minimal maintenance. This demands a high initial lumen capacity to compensate for the high LDD with polymer optics over time, or incurs a high labor cost due to a short cleaning interval required to maintain design illuminance values. Also, a long cleaning interval can result in permanent lens deterioration and/or discoloration in polymer optics. Glass lenses will cause up to 10% initial optical loss, but it attracts less dirt, nor does it lose optical clarity, discolor or otherwise degrade in harsh environments. Moreover, glass lenses have excellent serviceability with power washing. The long term benefit of protecting the LED assembly with a clear tempered glass lens far outweighs the initial cost and optical loss.Another issue with dirt accumulation is that it can cause depreciation in heat sinking performance. It's not uncommon for heat sinks of high bay lights to carry a complex design intended to promote conductive and convective cooling. However, the intricate geometry makes the heat sink a dust collector and compromises the luminaire's self-cleaning ability. Dust accumulation will negatively impact the thermal performance of the heat sink, and ultimately cause temperature dependent failures. High bay LED systems used in dust and dirt-prone environments should be designed to discourage accumulation of dirt and debris, and to allow water to easily flow off the luminaire when being washed.