Table of Contents Hide
- 1 Where There are Mission-critical Applications, There Is Industrial Lighting
- 2 Types of Industrial Facilities
- 3 Classified Areas
- 4 Challenges
- 5 Lighting Technology
- 6 The Advantages of LED Lighting for Industrial Applications
- 7 Design and Construction of Industrial LED Luminaires
- 8 LED Assembly
- 9 Spectral Output
- 10 Optical Design
- 11 LED Driver
- 12 Flicker and Strobe
- 13 Lighting Control
- 14 Thermal Management
- 15 Ingress Protection
- 16 Protection against Corrosion
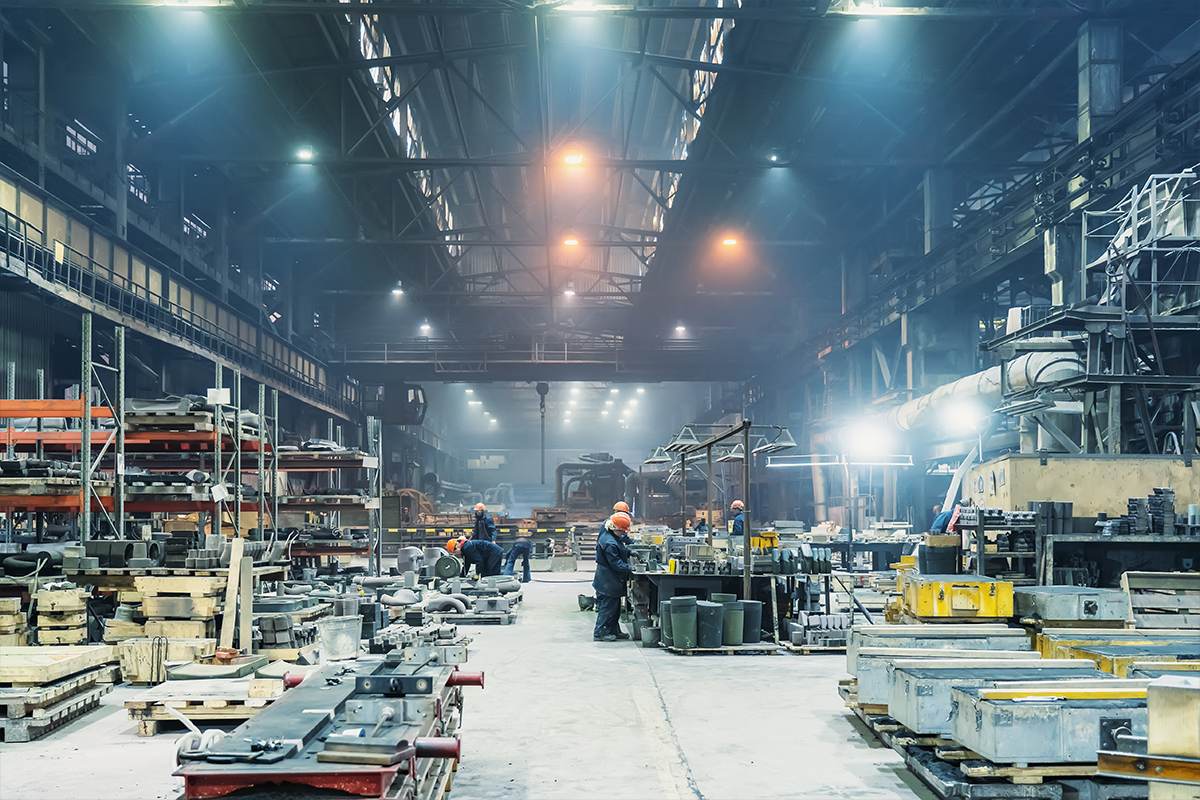
Where There are Mission-critical Applications, There Is Industrial Lighting
Industrial lighting products encompass lighting systems designed for application in indoor or covered real estate in the industrial sector. Most industrial luminaires have cross applications in commercial and recreational facilities such as big-box retail stores, gymnasiums, convention centers, exhibit halls, and buildings with expansive, high ceiling spaces. This guide will walk you through information on lighting systems installed in industrial environments. Few things affect an industrial facility more than lighting. From an operations viewpoint, optimum visual conditions can improve productivity or performance, enhance safety and security, and reduce the number of errors and lost-time accidents. For facility management, an ideal industrial lighting solution will provide a good ROI (return on investment) through energy and maintenance savings while having the ability to survive challenging industrial environments. A successful lighting design for a modern industrial facility therefore necessitates the use of lighting systems that excel in efficiency and reliability, and simultaneously deliver high quality light and photometric performance.Types of Industrial Facilities
There are two major categories of industrial facilities: warehousing facilities and manufacturing facilities.Warehousing facilities
Warehousing facilities are the largest industrial real estate category. The core differentiating features of warehouses are overall building design (typically rectangular in shape), ceiling height (16 to 80 feet), and loading capabilities. Warehouses can be further divided into regional warehouses, bulk warehouses, heavy distribution facilities, cold storage facilities, and rack supported warehouses. Regional warehouses generally do not exceed 100,000 square feet in size and have an average tenant space exceeding 20,000 square. Their ceiling heights are generally in the range of 16 to 24 feet. Regional warehouses have a varied tenant use. Some are designed to store goods, others are utilized as distribution facilities. Bulk warehouses are used to store large amounts of goods. These facilities have a minimum size of 100,000 square feet and a minimum ceiling height of 20 feet. Heavy distribution buildings resemble those of bulk warehouses but have a larger size (100,000 - 500,000 square feet), and a minimum ceiling height of 24 feet. Typical tenants in these facilities are logistic companies. A cold storage or refrigerated distribution facility which is primarily designed for food processing and distribution usually has a freezer floor section, a cooler, and a dry storage area. Rack supported buildings employ rows of box shelving, or racks, to maximize space utilization. Typically, each rack is several floors high. As such, rack supported buildings may have ceilings as high as 78 feet. The tall narrow aisles established by warehouse shelving can create lighting challenges and inefficiencies.Manufacturing facilities
Manufacturing facilities have physical characteristics that involve the manufacturing processes such as fabrication, assembly, sub-assembly, and finishing, as well as quality control, warehousing and logistics. Manufacturing facilities generally fall into two groups: light manufacturing buildings and heavy manufacturing buildings. Light manufacturing buildings have a size smaller than 100,000 square feet and a ceiling height in the range of 14 to 24 feet. Heavy manufacturing facilities have an average building size of more than 300,000 square feet, a minimum ceiling height of 16 feet, and a maximum height of around 60 feet. Aside from these buildings, airport hangars are also classified as manufacturing facilities. Airport hangars which perform repair and maintenance are similar in size to heavy manufacturing buildings and have ceiling heights usually exceeding those of rack supported buildings.There're other categories of facilities, which account for a small percentage of the industrial real estate. These categories include flex, multi-tenant, freight, and telecommunications facilities. Flex facilities refer to flexible buildings used by technology and service tenants for product research, development, testing, or display activities. Multi-tenant facilities are designed to accommodate a multiple number of tenants. Freight facilities are classified as truck terminal and air cargo. Telecommunications facilities are generally data/switch centers.
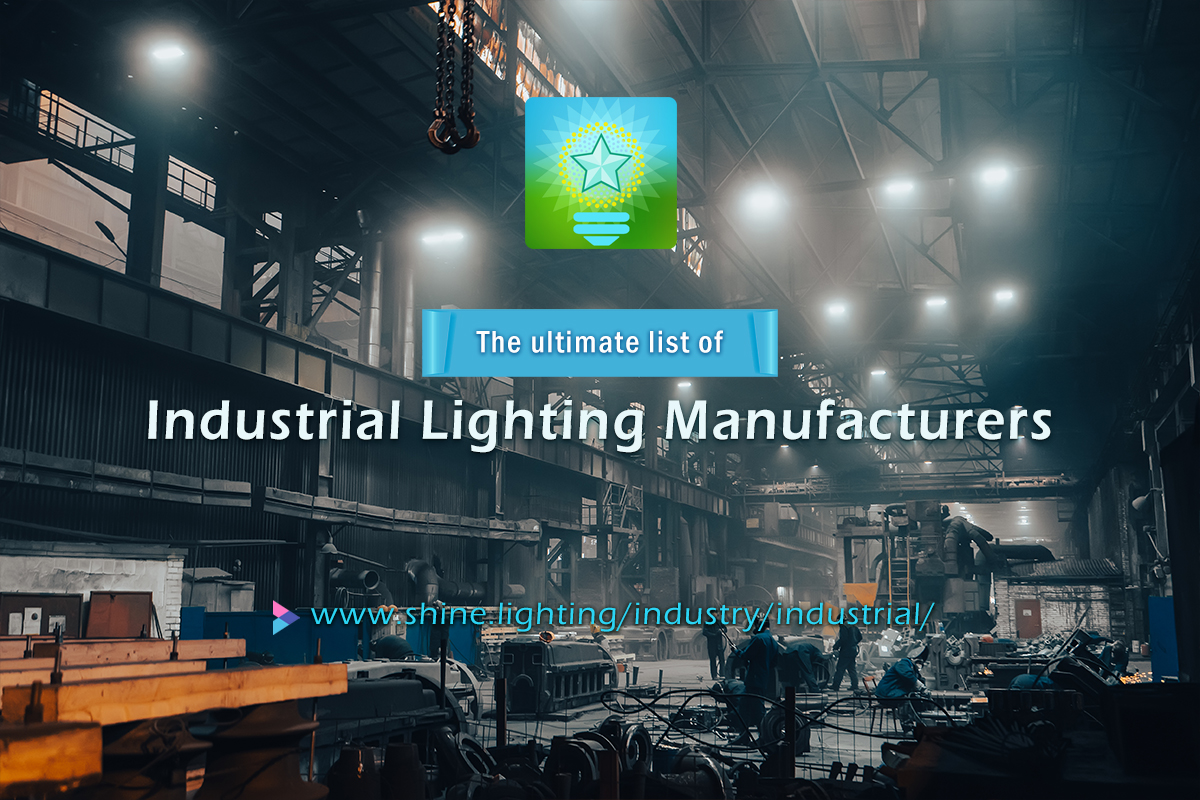
Classified Areas
Industrial environments have a diversity of operating conditions not found within other sectors. Industrial lighting fixtures may be subject to harsh and hazardous environments. These environments are classified and rules are set for the types of luminaires that may be installed in them.Hazardous locations
Hazardous locations are areas where fire or explosion hazards may exist due to the presence of flammable gases, vapors, liquids, dust, ignitable fibers or flyings. In North America, these areas are defined in the National Electrical Code (NEC) published by the National Fire Protection Association (NFPA) and Canadian Electrical Code (CEC) published by the Canadian Standards Association (CSA). Electrical installations in the European Union are governed by the ATEX Directive 2014/34/EU prepared by European Committee for Electrotechnical Standardization (CENELEC). The IECEx system from International Electrotechnical Commission (IEC) operates globally across many national and regional jurisdictions.The NEC and CEC define three categories of hazardous locations that have been designated as Class I, Class II, or Class III.
Class I locations are those where flammable gases or liquid-produced vapors may be present. Some typical class I locations are petroleum refineries, oil drilling rigs, gas processing plants, LNG facilities, mining operations, sewage treatment plants, dry-cleaning plants where vapors from cleaning fluids can be present, pipeline pumping stations, and spray-finishing areas. Based on the ignition temperature of the substance, its explosive pressure, and other characteristics of its ignition or explosive potential, the gases and vapors of Class I are broken into four groups: Group A (acetylene), Group B (hydrogen), Group C (ethylene), and Group D (propane).
Class II locations are those made hazardous due to the presence of a combustible or electrically conductive dust in quantities sufficient to ignite or explode. Typical class II locations include grain elevators, flour and feed mills, plants that manufacture or use conductive or metal powders like magnesium, fireworks manufacturers, producers of starch or candies, spice-grinding plants, sugar plants and cocoa plants, chemical and plastic mixing/storage areas, coal preparation plants and other carbon handling or processing areas. Within Class II are another set of groups: Group E (electrically conductive dust), Group F (carbonaceous dust), and Group G (agricultural and polymer dust). The group is determined by nature of the substance (the ignition temperature and conductivity of the dusts).
Class III locations are areas where easily ignitable fibers or flying are present. Typical class III locations include textile mills, woodworking workshops, cotton gins, and cotton seed mills.
Each class of the hazardous locations is further subdivided into two divisions depending on the likelihood of the hazardous material being present in a flammable concentration. Division 1 applies to an area where ignitable concentrations of hazards are present under normal operation conditions. Division 2 refers to abnormal or not normally present condition. The hazardous material is expected to be confined within closed containers or closed systems. Hazards may be present only through accidental rupture or breakdown of such containers or systems, or due to faulty operations.
The IECEx/ATEX system uses Zones to define hazardous locations. Hazardous locations in which flammable vapors or gases may be present are divided into Zone 0, Zone 1, and Zone 2. Zone 0 refers to areas where the flammable vapor or gas is continuously present or present for long periods of time. Zone 1 refers to areas where the flammable vapor or gas is likely to be present in normal operation. Zone 2 refers to areas where the flammable vapor or gas is usually not present in normal operation. The duration of the possible presence is short. Hazardous locations in which a combustible dust may be present are divided into Zone 20, Zone 21, and Zone 22. Zone 20 refers to areas where the combustible dust in sufficient quantities for a fire or explosion hazard to exist is present continuously or for a long period. Zone 21 refers to areas where the combustible dust in sufficient quantities to produce an explosive mixture is likely to be present occasionally during normal operations. Zone 21 refers to areas where a fire or explosion hazard due to the presence of a combustible dust is not likely to occur, and persists for only a short period of time if it does occur.
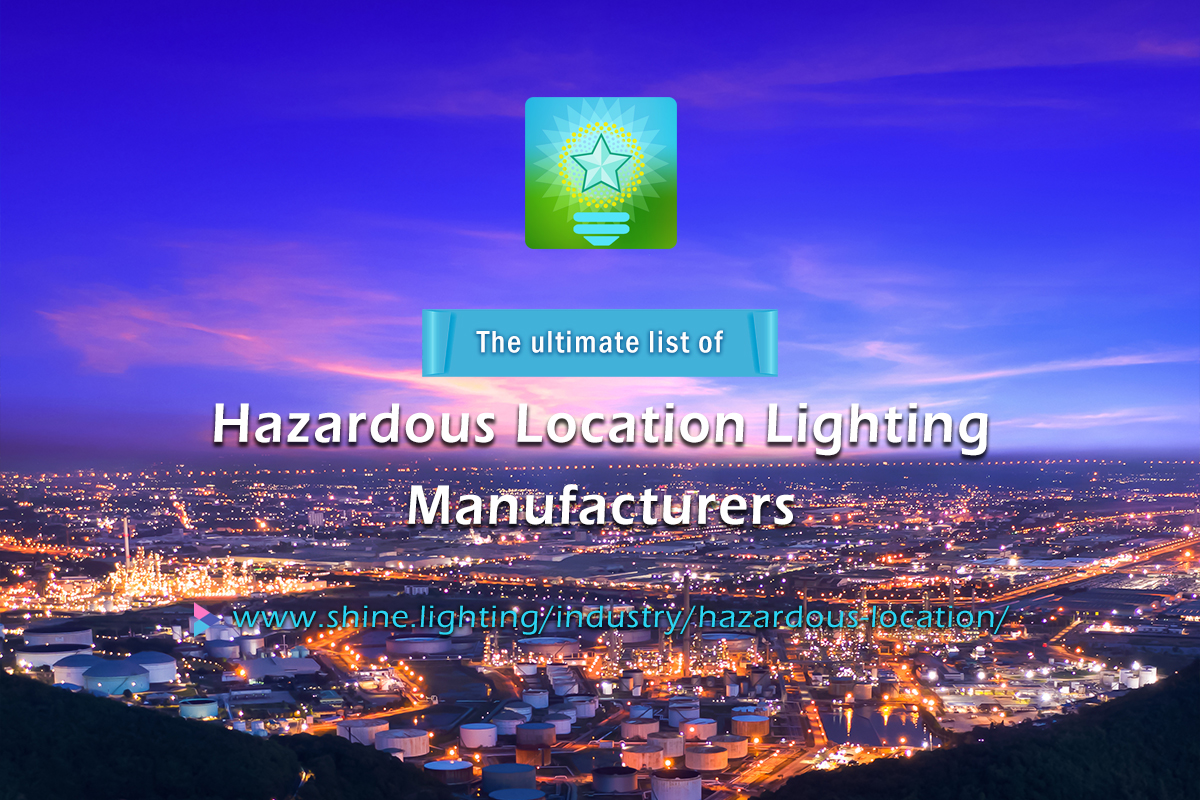
High humidity or atmospherically corrosive areas
Moisture ingress and corrosion are two major failure factors in industrial lighting systems, particularly LED luminaires. High humidity or corrosive atmospheres are likely to be present in many industrial environments such as chemical plants and warehouses, food processing facilities, pulp and paper mills, dyeing and printing mills, cement plants, and facilities located in coastal regions. Corrosive gases not only rust or wear out exposed metal parts, but can also penetrate through the LED encapsulant which is often silicone-based. Corrosion of the lead frame used in the mid-power LED packages will cause a reduction in light output. Corrosion of electrodes or bonding wires will result in electrical discontinuities or abnormal increases in forward voltage. Long-term exposure to a high humidity environment not just leads to corrosion. The diffusion of moisture within an LED package is the underlying cause of the formation of cracks in silicone encapsulants as well as the delamination between the LED die and the encapsulant, when both temperature and humidity are active stresses. Luminaires installed in high humidity environments have either a damp location rating or a wet location rating. A damp location refers to an environment is normally or periodically subject to condensation of moisture in, on, or adjacent to electrical equipment, and includes partially protected locations. A wet location refers to an environment where water may drip, splash, or flow on or against electrical equipment.Industrial environments with extreme ambient temperatures
Another challenge inherent to operating LED luminaires is heat. High temperature is one of the primary failure accelerators in LED-based lighting systems. Operations involving high air temperatures or radiant heat sources make it very challenging to thermal management of LED luminaires. The amount of heat that can be dissipated from the LEDs depends on the temperature gradient along the heat flow path from the LED junction to the ambient air circulating around the luminaire. Abnormally high ambient temperatures are often present in industrial applications. Industrial facilities that have high ambient temperatures include: iron and steel foundries, nonferrous foundries, heat treatment workshops, brick-firing and ceramic plants, glass products facilities, rubber products factories, fossil fuel power stations, boiler rooms, chemical plants, mining sites, and smelters. In these facilities, the luminaires should be designed to survive high ambient temperatures of as high as 65°C.Unlike fluorescent lamps that require a ballast for low-temperature starting, LED luminaires perform well in low ambient temperatures, with longer lumen maintenance and better color stability. However, the performance of other materials used in the luminaire, such as optical components and gaskets, should be verified at expected temperatures.
Cleanrooms
Clean rooms are sealed, controlled environments designed to eliminate microscopic particles of a specified size, such as dirt, airborne microbes, aerosol particles and chemical vapors. Maintaining the integrity of a clean environment is necessary for many manufacturing processes, such as semiconductor wafer fabrication, pharmaceutical manufacturing, and bio-tech research. Clean rooms are categorized into a series of classifications based on the number of micron particles found in a cubic foot of air inside the room. The International Standards Organization (ISO) cleanroom classifications are rated ISO 1 through ISO 9. The lower the rating, the cleaner the clean room. The classifications of the Institution of Environmental Sciences (IES) cleanroom classifications include start at 100,000 parts per cubic foot (Class 100,000), and proceed through Class 10,000, Class 1,000, Class 100, to Class 10. Cleanroom lights are usually constructed to carry a high degree of ingress protection (IP) and have an outside surface that is smooth, cleanable, and corrosion resistant.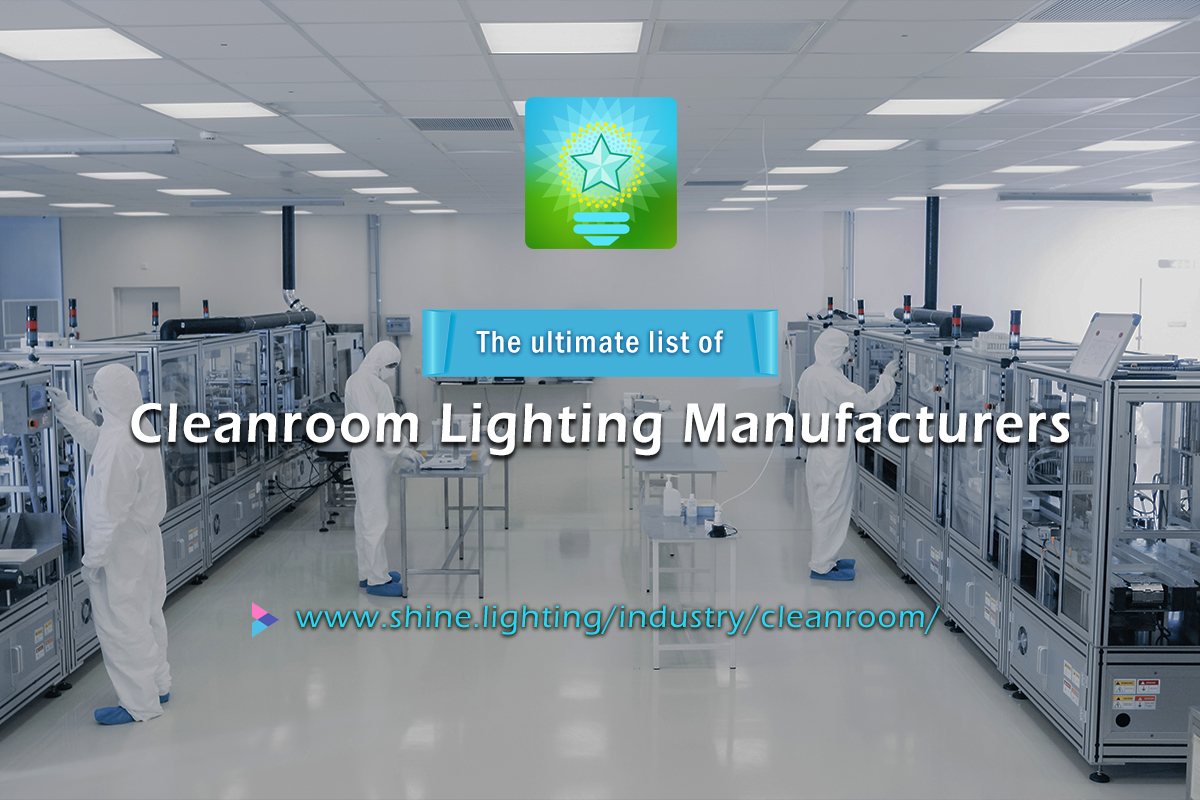
Food processing facilities
Luminaires installed in food processing facilities must hold up to sanitation required to prevent bacteria growth or harborage of other contaminants. Food processing applications usually require such products to be certified to standards such as those established by the National Sanitation Foundation (NSF). The NSF concerns itself with these luminaire construction issues such as the trapping of food particles, encouragement of bacterial growth, suitability for hose-down application. Therefore, the design and construction of the luminaire must take into account these factors: good cleanability, high watertight integrity, free of material toxicity and high corrosion resistance. A watershed design is required to ensure that a flow of water will carry the food or other contaminants off the luminaire housing. The gasketed area of the luminaire must be capable of resisting the daily high-pressure wash downs. The expose materials of the luminaire must endure the corrosive effects of cleaning solutions and will not introduce toxicity into food that would come in contact with the luminaire. However, lighting fixtures often do not come in contact with the food under normal conditions also they can physically located in food preparation and handling areas (the Food Zone). The NSF breaks down the equipment requirements into three zones: Food Zone, Splash Zone, and Non-Food Zone. Lighting fixtures are often located in the Splash Zone and Non-Food Zone.Challenges
Industrial lighting is a complex task that must balance many different considerations such as upfront cost, quality, reliability, efficiency, maintainability, and controllability. In today's hypercompetitive business environment, maintaining tight control over energy expense without undermining productivity, security and safety can mean the difference between profit and loss. In industrial applications, lighting is a major cost component that is constantly reappraised with regards to its ROI (return on investment) and TCO (total cost of ownership). All industrial lighting must be designed to support a safe, comfortable and productive manufacturing or working environment. To develop lighting solutions that meet quality, quantity and operational criteria, a variety of challenges need to be addressed. High, hard-to-reach ceilings, expansive spaces, high humidity, corrosive or explosive atmosphere, hot or cold temperatures, dirty power, vibration from large machinery, long operating hours and unique building characteristics - these unfavorable conditions can add up in lighting fixtures that have high up-front, installation, operation and maintenance costs.Lighting Technology
Traditional industrial lighting is a drain on energy. In the past, high-intensity discharge (HID) (i.e. metal halide), fluorescent and induction lamps were the usual choice of light sources for industrial applications. Metal halide fixtures, in particular, had been the dominantly used lighting systems for high bay applications. A metal halide lamp generates light by the passage of an electric current through a gaseous mixture of vaporized mercury and metal halides. The popularity of metal halide lamps in industrial applications can be credited to their high wattage availability, a moderate efficacy and lifespan. However, metal halide lamps have many drawbacks that significantly outweigh their benefits. These drawbacks include the long start-up and hot restrike process, production of ultraviolet light (UV), disposal/recycling problem of hazardous mercury, short life expectancy of high wattage bulbs, fast lumen depreciation, envelope failure (bulb explosion), and limited dimming capabilities. Fluorescent and induction lamps also have a number of problems, with the most prominent one being low source efficacy as well as luminaire efficacy. In addition to a mediocre source efficacy, these gas discharge lamps, including metal halide lamps, have a high fixture light loss factor. The optical loss of a metal halide, fluorescent or induction fixture is typically 30% of the light output of the bare, omni-directional bulbs. While the luminous efficacy of traditional lighting systems significantly underperforms ever-changing energy codes, high frequent maintenance and relamping lead to a high TCO that frustrates industrial facility managers.The progress in LED technology brought lighting to the forefront of sustainability and brightens the entire industrial landscape. LED lighting overcomes many limitations of traditional lighting technologies. The fact that LED technology makes industrial lighting on steroids can be attributed to its revolutionary light generation principle. A light emitting diode, or LED, is essentially a p-n junction formed by oppositely impregnated or doped semiconductor layers. An active layer (quantum well) is interposed between the n-type semiconductor layer and the p-type semiconductor layer. When a bias is applied across the doped layers in the forward direction, electrons from the n-type semiconductor layer and holes are from the p-type semiconductor layer injected into the active layer where they recombine to generate light. This is known as electroluminescense. The bandwidth of the spectral power distribution (SPD) of electroluminescense is a few tens of nanometers, which means light generated by the LED chip is a monochromatic light. To create white light from the narrow-band emissions, the electroluminescence is partially or completely converted by a phosphor such as yttrium aluminum garnet (YAG). The semiconductor chip, which is often a gallium nitride (GaN) device, pumps phosphors typically within the device package. Such an LED package is called a phosphor-converted LED.
The Advantages of LED Lighting for Industrial Applications
The many benefits of LED lighting have been well documented. The most notable one is the high ROI that comes with the high efficiency, low-maintenance, and long life operation of LED systems, even when considering there's a relatively high initial investment.The source efficacy of LEDs made from indium gallium nitride (InGaN) has improved enormously over the past decade. The highest efficiency LEDs today have a luminous efficacy exceeding 200 lm/W, which is a quantum leap when compared with legacy light sources. The directional nature of LEDs results in a low fixture light loss factor. Through carefully designed lenses, an LED luminaire can achieve an optical efficiency as high as greater than 90%, with the added benefit of minimal light spill. A large light emitting surface (LES) is made possible with discrete LEDs. In conjunction with custom optics that regulates luminous flux from each individual LED, the light distribution uniformity of LED luminaires is improved by more than a factor of two versus HID luminaires. This means maximized fixture spacings, and consequently reduced number of installed luminaires as well as reduced energy consumption. The nearly instantaneous response of LEDs to changing current allows for a more efficient utilization of electricity through manual, programmed or sensor-based dimming control, which is not possible with traditional industrial luminaires.
While the systems approach to improving energy efficiency in industrial facilities contributes to rapid payback on lighting and code-compliant facilities operation, the extended lifespan and minimal maintenance requirement of LED systems ensure a high return on investment and give facility managers peace of mind. A properly engineered LED lighting system can operate for as long as 100,000 hours. Made from a block of semiconductor, no filament or glass to break, the solid-state nature of LEDs allows luminaires to be built with greater resistance to shock, vibration, and wear. This increases the luminaire lifespan significantly. A longer operation life and reduced need for maintenance translate to the reduced risk of hazards commonly associated with servicing luminaires installed in challenging industrial environments, which often involve harsh and hazardous installations. Considerable labor costs and a high safety concern are involved in the maintenance and replacement of short-lived traditional lighting systems.
An often-neglected advantage of LED lighting is its ability to provide high quality spectral output. LEDs have a spectral power distribution only in the visible portion of the electromagnetic spectrum (roughly 400 to 700 nm). Absence of ultraviolet (UV) and infrared (IR) radiation means LED products are more photobiologically safe than traditional light sources. Both the color appearance (color temperature) and color rendering performance of LED luminaires can be spectrally optimized to align lighting with task requirements or human needs.
The explosion hazard is not a characteristic of LED lighting systems. These solid state lights contain no pressurized gas, hot filament or arc source. The exterior surface temperature of an LED luminaire is usually lower than the ignition temperature of the surrounding flammable atmospheres.
Design and Construction of Industrial LED Luminaires
Industrial LED luminaires generally fall into three categories: high bay lights, low bay lights, and outdoor floodlights. High bay fixtures refer to luminaires designed for applications where the mounting height is not less than 6.1m (20 ft) and the spacing-to-mounting height ratio is 1.5 or less. Low bay fixtures are designed for applications that where the mounting height is less than 20 feet above the floor and a spacing-to-mounting height ratio greater than 1.5 is required. These are not rigid rules. It is not uncommon to see high bay luminaires in low bay applications, and vice versa. Typically, a low bay luminaire has a light output in the range of 5,000 and 20,000 lumens, a high bay luminaire has a light output in the range of 15,000 and 100,000 lumens. Floodlights serve to provide outdoor area and task illumination for industrial parks and outdoor manufacturing facilities such as petroleum refineries, chemical plants, drilling rigs, oil depots, sewage treatment plants, and open pit mines. Outdoor floodlights come in a variety of lumen packages, photometric distributions, and mounting heights.The design of an industrial LED luminaire calls for a holistic approach because a group of interacting, interrelated, or interdependent elements affect the performance and longevity of LEDs. Energy efficiency and reliability are especially priorities due to the long running hours, harsh environments, and relatively high wattages typically involved. The system efficiency of an LED luminaire is the cumulative efficiency of its LEDs, driver and optics. The system reliability of an LED luminaire is determined by all its constitutive parts and their resistance to environmental and operational stresses. The three main design elements critical to the performance and useful life of industrial LED luminaires are junction temperature, drive current, and environmental conditions. Effective thermal management is required to keep the junction temperature within an optimal operating range. It is vital to exercise tight load regulation so that the drive current is always matched to the electrical characteristics of the LEDs in the context where dirty power is often present. To avoid extrinsic failures or fire/explosion hazards in industrial environments, it is necessary to factor environmental conditions into design considerations.
Industrial LED luminaires are manufactured in various forms to serve different needs. They generally have a fixture-as-heat-sink design which is intended to facilitate heat exchange to the surrounding environment. The housing serves as the heat sink and is typically constructed from die-cast, cold forged or extruded aluminum. The LED assembly is mechanically attached to the flat surface of the heat sink. A high thermal conductive interface material (TIM) is placed between the LED board and the heat sink to fill out thermal junctions and maximize the heat flow. The LED assembly may be integrated with secondary optics that sit close to the LEDs for controlled light extraction. The luminaire may otherwise have a plastic or glass cover attached to the bottom to enclose the light source and to protect against accidental damage. High wattage LED luminaires often have a modular construction which provides scalability in light output and flexibility in beam customizations, and also allows easy assembly, maintenance and upgrade. The building block of these luminaires is a light module that integrates the heat sink, LED assembly, and lens (or protective cover) into a self-contained assembly with the desired ingress protection (IP) rating.
The drivers of both integrated and modular LED luminaires are typically mounted in a separate compartment or externally. This configuration prevents the temperature-sensitive circuit components from being thermally stressed by the self-heating LEDs, and allows for convenient servicing and replacement of drivers.
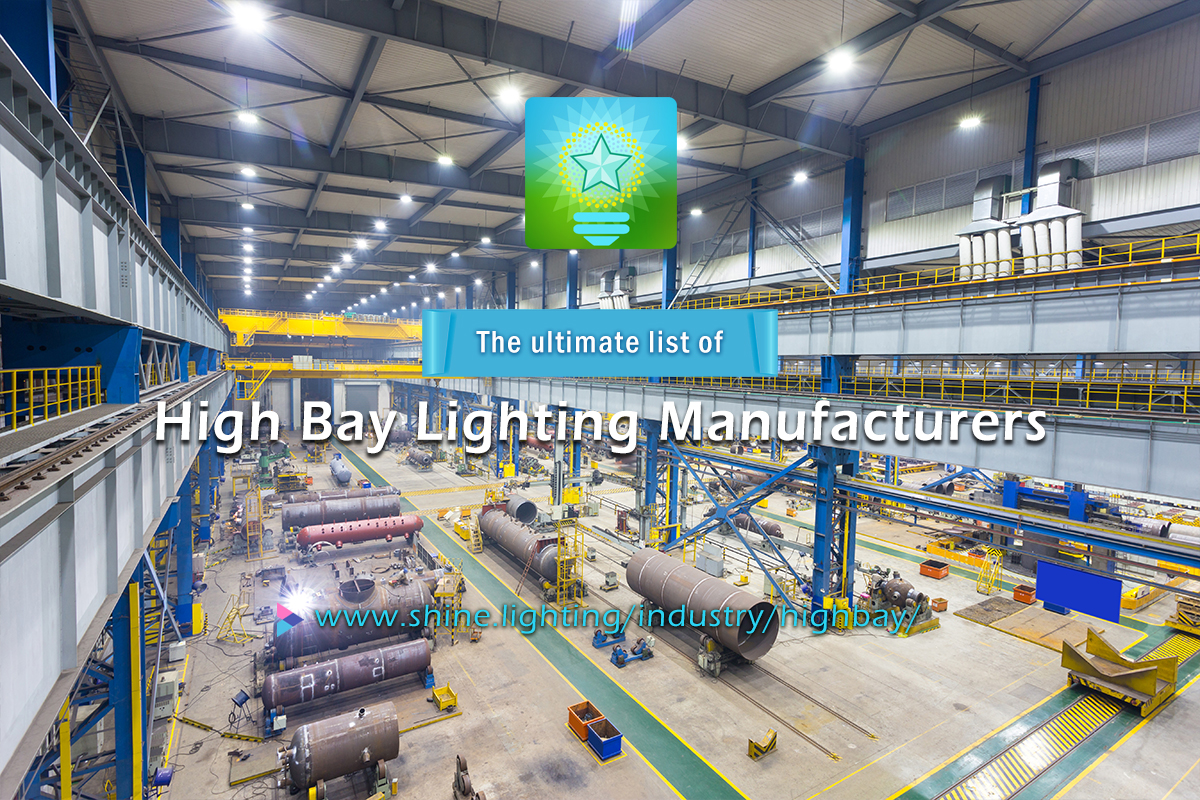
LED Assembly
The LEDs are mounted in a metal core printed circuit board (MCPCB), in a series string or in a mix of parallel and series for an identical current flowing in each LED. The MCPCB is constructed with an epoxy dielectric layer sandwiched between a top copper layer and an aluminum substrate. Such a design allows the circuit board to meet a minimum high potential (hipot) test while offering high through board thermal conductivity. This insulation dielectric often contains a second phase material such as ceramic particles which has thermal resistance. The thermal conductivity of an MCPCB can be 4 - 16 times higher than conventional FR4 boards.Within an industrial facility, there are locations where luminaires may need to withstand vibration from machinery. The reliability of the solder joint between the LED package and PCB thus becomes critical in the dependable operation of LED luminaires in such environments. The formation of a reliable solder joint not only depends on the solder alloys and the metallization of the LED package and PCB, but also on the reflow profile. The reflow profile has a significant impact on the wetting behavior, interface chemistry, and metallurgical microstructure of the solder joint. The creep resistance of the solder alloy is also a significant determinant of solder joint reliability under thermal cycling conditions, in particular when there's a high coefficient of thermal expansion (CTE) mismatch between components. Creep resistant alloys can limit the amount of strain energy buildup, thereby minimizing failures in solder joints and preventing forward voltage increase that could result from such a strain energy buildup.
Light Source
In the lighting industry, the term "LED" usually refers to an LED package, rather than an LED chip (the p-n junction semiconductor die). Packaging plays multiple roles in that it enables the semiconductor die to pump phosphors within the device package to produce white light with the desired spectral quality; mechanically, thermally and electrically interfaces the LED chip to its operating interface; and provides the semiconductor die with protection from environmental contaminants and stresses. The packaging design and packaging materials play a crucially important role in determining optical, electrical, thermal performance of LEDs. The majority of contemporary LEDs are constructed as high power packages, mid-power packages, and chip-on-board (COB) packages, while the latest trend in LED packaging is chip scale packaging (CSP).
There is a critical trade-off between the initial cost and long term performance in the selection of LED package platforms for industrial applications. High power packages attach a large LED chip to a metallized ceramic substrate which, in conjunction with metal pads on the underside of the ceramic substrate, provides a high efficiency thermal path to extract heat from the semiconductor die. The packaging design also allows homogenous distribution of the current density over the semiconductor junction, thereby reducing the risk of thermal runaway. Low thermal resistance and uniform current spreading bring high drive current and high flux density capabilities to high power LEDs. High thermal stability of the packaging materials allows the LEDs to deliver excellent lumen maintenance and color stability even at high temperatures. The package reliability and performance stability of high power packages are the most desired features in industrial applications.
A primary obstacle to widespread implementation of high power LEDs is their relatively higher up-front costs when compared with mid-power packages. Mid-power LEDs are plastic leaded chip carrier (PLCC) packages that are designed for low lumen density applications in the residential and commercial sectors. High initial efficacy and low cost are the selling points of mid-power LEDs. However, these advantages seldom translate to a high return on investment due to the inherent limitations of the package platform. PLCC packages have poor degradation resistance to high temperatures, corrosive atmosphere and photo oxidation. The construction of a PLCC package is supported by a molded, highly reflective plastic housing and a silver-plated lead frame. The plastic housing that encases the LED chip is made from polyphthalamide (PPA) or polycyclohexylenedimethylene terephthalate (PCT) which yellow from exposure to heat and light. The lead frame plating is prone to corrosion when exposed to corrosive gases such as hydrogen sulfide (H2S).
In high power LED systems, mid-power packages exhibit rapid lumen depreciation and color shift as a result of high thermal and oxidative stresses as well as atmospheric corrosion. The electrodes of the chip in PLCC packages are connected to the lead frame by the wire bonding which may break due to electromigration or a blowout in the bonding wire because of excessively large current. Consequently, the reliability of mid-power packages is a significant concern. The useful life of LED luminaires that use mid-power packages is considerably limited. Mid-power packages with epoxy mounting compound (EMC) housings and Quad Flat No-lead (QFN) anode/cathode pads provide improved resistance to discoloration at higher temperatures as well as enhanced interconnection reliability and heat dissipation. However, these packages come at a higher cost.
Spectral Output
Spectral output is another major factor that goes into the selection of light source. The spectral output of LEDs can be characterized by its color temperature and by its color rendition.It's a typical phenomenon in industrial applications to use light sources with a correlated color temperature (CCT) greater than 4000 K. It makes sense to select a CCT between 4000 K and 5500 K for workplace lighting because the large amount of blue emissions contained in the cool white light can suppress the production of the sleep hormone melatonin and program the body for day mode. In addition to simulating a daytime physiological response for improved concentration, alertness and performance, light sources with higher amounts of blue light carry a higher scotopic/photopic (S/P), which means better visual acuity in low luminance conditions (mesopic vision). It's generally safe to use LEDs with color appearance in fluorescent whites (6000 K - 6500 K). However, light source with such high CCTs may pose photobiological hazards in industrial applications and tasks requiring high illuminance (above 1000 lux). These industrial applications and tasks include, but not limited to, exacting assembly, fine bench or machine work, fine grinding, manual crafting, precision manual arc-welding, vehicle body finishing, quality control inspections, jewelry and watch manufacturing, and leather working.
A color rendering index (CRI) of 80 or slightly higher is considered the minimum acceptable value for industrial applications and a CRI greater than 90 is considered good. However, blue-enriched high CCT light sources with an 80 CRI are often deficient in key wavelengths that are important for rendering highly saturated colors. Color distortion because of the missing wavelengths can increase the risk of errors when executing detailed-oriented tasks. Whenever selecting LED luminaires for applications where color and contrast recognition are important, check the spectral power distribution (SPD) of the light source if all key wavelengths are uniformly spread throughout the visible spectrum. The general color rendering index Ra alone does not reflect the color rendering capability of a light source because it is a single number based on the average color difference for eight reflectance samples of fairly low saturation. It ignores the rendering performance of six highly saturated colors: red, yellow, green, and blue, complexion, and leaf green. As such, users should take note of the extra CRI colors, in particular R9, a deep red sample. An R9 value of 25 is considered good for general lighting, and R9 values above 75 should be considered for color-critical applications.
Lighting manufacturers have been trying selling to uneducated customers high CCT and low CRI products. They even game CRI calculations by focusing on the wavelengths for rendering eight test samples of CIE Ra. The reason for this is that there are cost increases and efficacy drops in lower CCT and high CRI LEDs. In blue pump LEDs that produce white light with a high CCT or low color rendition, only a small portion of blue emissions needs to be down-converted into longer wavelength light by a low cost yellow phosphor. On the other side, to produce high color quality white light or warm white light from blue pump LEDs, a significant portion of blue emissions needs to be down-converted. The more the wavelengths is to be down-converted, the higher the Stokes energy loss occurs. Increased Stokes loss due to phosphor down-conversion not only results in reduced luminous efficiency, but also increases the amount of waste heat that has to be extracted from the LEDs. In order for the blue pump LEDs for deliver radiant power fairly broadly across the visible spectrum for accurate color rendition, a more expensive broadband phosphor down-converted has to be used. What's more, the human eye is less sensitive to light with longer wavelengths. This causes the low CCT or high CRI LEDs to have a lower luminous efficacy of radiation (lumens per watt) in comparison to high CCT or low CRI LEDs that deliver the same amount of optical power (radiant flux in watts).
Optical Design
The performance of optical systems can significantly affect productivity, safety and energy efficiency in industrial environments. Many considerations enter into the design decision for the optical systems of industrial LED luminaires. Optical efficiency, uniformity, and glare are the primarily considerations that should be prioritized during optical design. Industrial luminaires are typically high lumen lighting systems, a high fixture light loss factor can mean a huge energy waste which offsets the energy efficient benefit of LED lighting. The directional emission pattern of LEDs enables high efficiency extraction of the luminous flux emitted from the light source. However, the high directional intensity of LEDs makes glare control a necessity when a bright and concentrated light source is in direct line of sight. While glare is of particular concern in low bay environments, the uniformity of light distributions is universally influential for its impact on the quality of illumination and luminaire spacing.In many workplaces, the distribution of light at the workplane should be relatively uniform so that shadow do not obscure important details. Uniform horizontal illuminance is of critical importance in industrial interiors where tasks are closely spaced. No extreme luminance differences should exist in neighboring areas because this will require the human eye to continuously adapt between two significantly luminance levels and result in eye fatigue. Uniform lighting also reduces the need to relocate luminaires upon the repositioning of task locations or production machinery. Most industrial applications require a max/min uniformity ratio of 3:1 or less. HID fixtures have a typical a max/min uniformity ratio of 6:1. In order to meet the uniformity requirement, a high fixture density is needed. Through a large LES and optical control using secondary optics, LED fixtures can distribute light with a very low uniformity ratio (less than half of that of HID fixtures), thus making it possible to maximize fixture spacing and drastically reduce the number of fixtures needed to cover the task area.
In industrial facilities, not only horizontal illuminance is important, quite often vertical illuminance and the illuminance at other planes between horizontal and vertical are equally essential. Work performed deep within the recesses of production equipment often requires light to penetrate into the equipment. This may be accomplished by using luminaires with very wide distribution. But care should be exercised to ensure no high angle glare is produced. Typically, a prismatic refractor is used to control the directions from which light leaves the luminaire thus obscure the image of the light source while providing vertical illuminance. In confined spatial environments such as rack supported warehouses, narrow traffic routes and high shelves require adequate illuminance on the horizontal floor surface, but also vertical illumination on both sides of the racked aisle. The photometric performance then requires the use of precision optics to distribute light along the aisle on the floor and illuminate the vertical surfaces of the rack.
The photometric performance of modern LED luminaires is achieved via either specialized secondary optics associated with individual LED packages, or traditional optics such as reflectors, refractors, diffusers which provide optical regulation for the LED assembly. Traditional optics offer a much simpler and more cost-effective approach than making special optics for each LED. They are typically used in applications that require the LED luminaires to deliver wide-distribution general lighting. Reflectors continue to play their role in optical control for LED luminaires but they're more often used to regulate the light output from an LED module with a small or narrow LES. However, most high power LED systems have a large emission surface which is intended to uniformly distribute light over a large area. A reflector which sits on such a large LED array will only control the light that is incident on the reflective surface. For LED assemblies that have a large emission surface, the secondary optics may be a lens array or a grid of small reflectors that regulates luminous flux from the individual LED packages. Designing optics separately for every LED allows for more efficient light extraction and higher precision beam control than it is possible with a single optical control element.
A lens array is a one-piece injection molded lens system that consists of a number of single lenses or compound lenses. The compound lenses are total internal reflection (TIR) lenses. A TIR lens is a combination of refractive and reflective lenses with a common axis. The lens array may be made of acrylic (PMMA) or polycarbonate (PC). However, from a reliability perspective, plastic lenses may not be a good choice for some industrial applications. In high wattage LED systems, the Stokes heat generated during wavelength down-conversion can cause the phosphor temperatures to rise 30°C to 50°C above the junction temperature. This produces a very high thermal stress to the plastic lenses which fit tightly over the LEDs. Accelerated discolouration and ageing can occur at elevated temperatures. In operating environments with high ambient temperatures, the plastic lenses are more prone to thermal degradation. Moreover, plastic optics attract dust and dirt depreciation becomes an issue. Aluminum reflectors and glass lenses are more reliable in harsh industrial environments.
LED Driver
The LED driver is the trickiest part of an LED luminaire. It handles the complexities of the incoming AC line power and provides a constant current output for optimal operation of LEDs. However, the relentless pursuit of cost reduction in the lighting industry makes LED drivers the primary object that takes the brunt of compromise on performance and reliability. As a result, drivers have been the most observed failure point in LED lighting systems. In industrial applications, the efficiency and reliability are the most important factors that have to be thoroughly evaluated during pre-purchase deliberations. In order to illuminate high ceiling, expansive spaces, industrial lighting fixtures typically draw a large amount of power. This prompted the need for LED drivers with high power conversion efficiency. To deliver an operating life matching that of LEDs requires the driver to operate to specification under wide temperature and electrical ranges that're often present in industrial facilities.The driver that is used in an industrial LED luminaire is typically designed as a switching mode power supplies (SMPS). An SMPS regulates its output by varying the duty cycle of a saturated power switch. The power switch acts on pulse-frequency-modulated (PFM) and/or pulse-width-modulated (PWM) control signals. Compared to linear power supplies, switching circuits have the fundamental advantages of higher efficiencies, wider input voltage application, better output quality, smoother and wider range dimming capability, better protection of downstream components from electrical overstress (EOS), and allowing galvanic isolation from the input circuit. These advantages of using switching circuits significantly outweigh the disadvantages of having to take electromagnetic interference (EMI) filtering and screening into account. The high frequency switching operation of SMPS circuits generates EMI radiation which interferes with radio signals as well as other electronics. The cost arising from suppressing EMI with additional circuits can double the overall cost of the LED driver.
Unlike an incandescent lamp which is a simple resistive load, SMPS drivers include reactive components which causes the load to draw additional reactive current out of phase with the line voltage. The presence of reactive load makes it necessary to exercise power factor correction (PFC) to maximize real power flowing to the load and minimize harmonic distortion. A minimum power factor (PF) of 0.95 is required for AC-DC LED drivers with a power rating of greater than 25W. AC-DC LED drivers can be divided into the single-stage type or the two-stage type. Single-stage LED drivers combine functions of power factor correction and DC-DC converter (e.g. a boost converter, a buck converter, or a flyback converter) in one circuit, whereas two-stage LED drivers have a second conversion stage following the active PFC stage. The two-stage design increases the component counts, internal losses and circuit complexity but allows the driver to deliver high immunity to power surges, minimal ripple in the output, and full range dimming in almost every output current range. A single-stage driver has substantially less components and lower costs when compared to a two-stage driver. However, large ripples at twice the line frequency may be introduced into the output due to incomplete suppression of the alternating waveform after rectification.
The key performance metrics of drivers focus on not only their ability to efficiently convert AC line power to an output compatible with the LED packages, but also the ability to protect downstream components from power surges, poor incoming power quality, and abnormal operating conditions. Voltage and current fluctuations in the power line are a common condition in heavy industrial settings. Although they do not create huge, short-duration high-voltage transients that accompany lightning strikes, switching-related transients (caused by starting motors or transformers, operation of fuses and circuit-breakers, utility power switching, etc.) are lower in amplitude, but last longer and occur more frequently. Constant dirty power use over time can accelerate the failure mechanisms in LEDs as well as other downstream components. While protecting luminaires from high-voltage surges is important, a wide input voltage capability is necessary for the driver to accommodate the longer duration, lower amplitude oscillatory transients. In addition to surge protection, a variety of protection schemes are also built into the driver hardware. Protections implemented on power supplies and DC/DC converters include over-voltage, over-current, short-circuit, open-circuit, and over-temperature protections.
Typically, the electrolytic capacitor is the first component of a driver to fail. The performance and lifetime of electrolytic capacitor is seriously affected by its operating temperature because of the use of electrolyte which has poor thermal stability. The operating temperature of the capacitor is determined by the driver efficiency, ambient temperature, and the internal heating within the capacitor caused by the ripple current flowing through it. For every 10°C increase in the operating temperature the lifespan of the electrolytic capacitor is shortened by a factor of 2. The evaporation of electrolyte in the capacitor causes the rise of equivalent series resistance (ESR) and the drop in capacitance. This results in large ripple in the output, generation of noise, a decrease of holdup time, and in some cases malfunction or no-start conditions of the control circuits. In industrial environments where the high ambient temperature is present, the dependable operation of LED drivers call for good thermal management of the driver, high efficiency power conversion (for less dissipated heat), and the use of high temperature capable electrolytic capacitors.
Flicker and Strobe
Flicker and stroboscopic effects are a common issue with LED luminaires operated by low cost LED drivers. To slash costs and/or reduce footprint, the design of LED drivers often ignores the full suppression of the sinusoidal waveform of the alternating mains voltage. This results in the unwanted residual periodic variation or ripple in the direct current output. The instantaneous response of LEDs to changing current causes them to flicker that may match the AC frequency, such as 120 or 100 Hz, when there are sufficiently large ripples. Flicker is visible up to 80 Hz. Both visible and invisible flicker can produce negative physiological effects in some populations. They include seizures, migraines, headaches, eyestrain, and, in severe cases, epileptic seizures and evidence of aggravating autistic conditions. When there is motion of objects, periodic changes in light output can give rise to stroboscopic effects. Stroboscopic effects might induce hazards to operators of rotating machines or other rapidly cycling equipment. The output of single-stage driver circuits and linear power supplies usually exhibits a large ripple, whereas the two-stage design performs better in smoothing out the large output current ripple delivered to the load. As one of the key performance markers, high quality drivers have a ripple value within the range of ± 10%, low-performing drivers have a ripple value as high as ± 30%. In general, percent flicker greater than 20% at 100 Hz or greater than 30% at 120 Hz is considered unacceptable.Lighting Control
Lighting control systems allow luminaires to deliver the correct amount of light at the correct time, thereby reducing energy waste to a minimum. The effectiveness of lighting control depends on the on/off/dim capability of the light source being operated. LEDs lend them perfectly to lighting control for their instant on/off capability and current-driven nature. LEDs can be dimmed by constant-current LED drivers that support pulse-width modulation (PWM) or constant current reduction (CCR) dimming. Industrial LED luminaires often employ the CCR technique to dim the LED load. Commonly referred to analogue dimming, CCR dimming is typically controlled through the 0-10V or DALI protocol. LED drivers can be programmed to provide constant light output (CLO) dimming. The advantage of CLO is that the drop in luminous flux of the luminaire due to the natural wear-out mechanism of LEDs is continuously compensated. This eliminates the need to overplan the lumen package of a luminaire at the beginning of the life cycle.Initially largely manual in nature, the on/off switching and dimming control of lighting systems evolved into highly automated operations accomplished by using various lighting control strategies such as occupancy control, daylight harvesting and time control. Industrial spaces are more suited to networked control which allows luminaires to be controlled as a whole, in zones, or individually. A networked control system may be operated on a wired communication platform. However, wired lighting control solutions are inherently not scalable as implementation costs rise when system complexity increases. Wireless control systems eliminate the need for complex wiring that increases installation and maintenance costs and limits where the fixtures can be installed. Wireless communication protocols such as ZigBee, Z-Wave, Wi-Fi, Bluetooth Mesh and Thread allow luminaires to exchange data over a flexible, scalable and interoperable network with low deployment costs. The growing trend in Industrial IoT (IIoT) is driving the migration of lighting control to IP-based network infrastructure. This opens up a host of additional applications beyond more energy efficient, adaptive, and automated lighting.
Thermal Management
The object of thermal management to provide an efficient thermal transfer path from the LEDs through the circuit board to the ambient environment. More than half of the electrical power fed to LEDs is dissipated as heat. The self-generated heat within the LED must be extracted out of the package before excess buildup of heat causes irreversible damage to the LED. The majority of LED failure mechanisms that lead to abnormal lumen depreciation and color shift are temperature-dependent. Operating LEDs beyond their maximum junction temperature limit will accelerate nucleation, dislocation and other defect generation in the active region of the diode where the radiative recombination occurs. This causes internal quantum efficiency (IQE) losses due to the increase in non-radiative recombination of injected electrons and holes. Thermally-induced failure mechanisms that occur at the package level include phosphor thermal degradation, discoloration of encapsulant and plastic packaging materials. That is to say, the service life of LEDs is highly dependent on temperature control of the p-n junction. The cooler the junction temperature of an LED remains during operation, the better the lumen maintenance and color stability the LED will have. In some luminaire designs, the driver may be co-located with or thermally influenced by the LED module, thermal management must ensure heat-sensitive components of the driver, e.g. electrolytic capacitors, are not stressed by the LED thermal load.Within an LED system, the junction temperature of LEDs is affected by drive current, thermal path, and ambient temperature. While being dimensioned to equal the maximum power load applied to the LEDs, the thermal path must be shortest possible to facilitate efficient heat transfer between the LEDs and the ambient atmosphere. A systems approach to thermal management is mandatory. The design variables of a thermal path include the maximum allowable junction temperature of LED packages, high operating temperature capability of interconnects, thermal resistance of the MCPCB and TIM, and heat sink performance. The most influential part of a thermal management system is the heat sink which functions to store the dissipated heat from LEDs and create more surface area to convect and radiate the stored heat to the ambient air. A heat sink is made from a high thermal conductivity material such as aluminum has a flat area to permit intimate contact with the LED assembly for effective heat spreading. Heat sinks may be designed with channels, fins or other geometries which increase surface area for thermal convection.
It's worth noting that the heat sinks of many industrial LED luminaires are over-designed. Deep fins and complex geometries lend these heat sink susceptible to accumulation of dirt and/or ponding of fluids. Over time the accumulated dirt can significantly compromise the performance of the heat sink, while pooling of water or other caustic liquids will cause corrosion of the heat sink.
Ingress Protection
In the design of lighting for industrial environments, the ability of lighting systems to resist the ingress of dirt, dust, moisture and water is one of the critical considerations. High humidity, water splashes, airborne contaminants, and other performance-inhibiting elements are likely to be present in many industrial facilities. When used in these environments, a luminaire with a low level of ingress protection is highly susceptible to premature failures or accelerated performance degradation. Moisture or water trapped within a luminaire can cause metal corrosion, electrical malfunctions, and lens clouding. Dust, dirt or particulates that deposit on optics and light sources can cause lumen depreciation. An LED by itself has poor resistance to moisture and gas ingress because the optical materials used in LED packages, i.e. silicone, have high moisture and gas permeability. Moisture that penetrates into the bulk of lens and encapsulant can cause the formation of cracks in silicone encapsulants, as well as delamination at the chip/phosphor interface due to hydro-mechanical stresses.In moisture and dust laden environments or areas where daily high-pressure wash-downs are present, the minimum class for protection from dust and moisture ingresses should conform to the IP65 rating or better. To ensure the high enclosure integrity over the rated service life of a luminaire, a membrane venting solution is used to equalize the pressure differentials between the enclosure and its environment.