Table of Contents Hide
- 1 What Is an LED Grow Light
- 2 How Do Plants Use Light
- 3 Photoreceptors
- 4 Photosynthetically Active Radiation (PAR)
- 5 Action Spectrum
- 6 The Revolutionary Power of LED Technology
- 7 Emission Mechanisms of LEDs
- 8 System Architecture
- 9 Light Source
- 10 Thermal Management
- 11 LED Driver
- 12 Ingress Protection
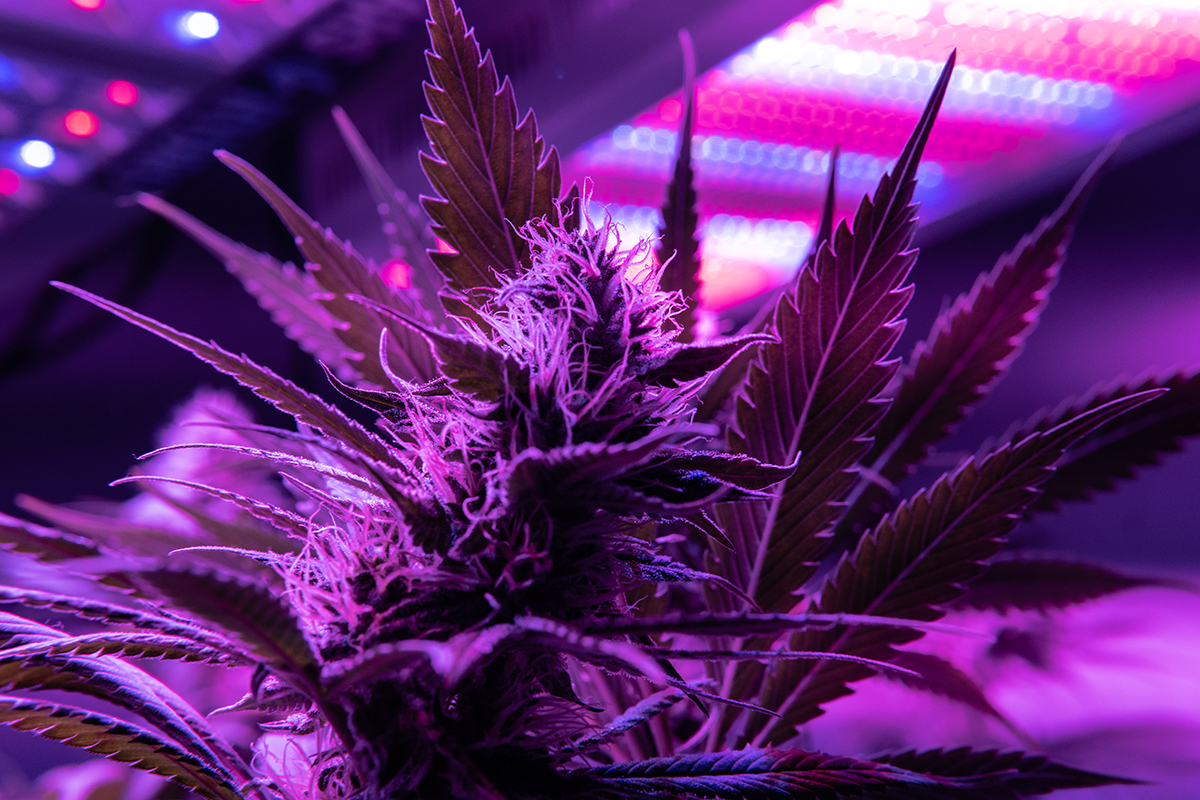
What Is an LED Grow Light
An LED grow light is a horticulture lighting system that uses solid state lighting technology to deliver photosynthetically, photomorphogenically, and photoperiodically active radiation. Horticulture lighting, once a small niche in both the lighting and agriculture industries, is undergoing a radical transformation fueled by the introduction of LED technology. The explosive growth of horticulture lighting market is spurred on by the ability of LED grow lights to provide a highly targeted spectrum that enables growers to create the most effective growing environment without the costly energy consumption. Endowed with both digital and spectral controllability, LED grow lights are deemed to make a significant contribution to horticulture revolution that comes with the growing trend in vertical farming and controlled environment agriculture (CEA).How Do Plants Use Light
Horticulture lighting is a science of spectroscopy that explores the interaction between plant biology and electromagnetic radiation. The sun propagates its energy through electromagnetic radiation which releases packets of energy called photons. Each photon carries a fixed amount of energy that causes the photon to vibrate or oscillate. The distance of one full cycle of the oscillation is referred to as its wavelength. The radiation spectrum of sunlight has wavelengths spanning from 200 nm to greater than 1000 nm. A very small part of this spectrum i.e. between the wavelengths 380 and 780 nm is capable of exciting the retina of the human eye and produces a visual sensation. This visible portion of the electromagnetic spectrum is called visible light. Coincidentally, this is almost the same range of wavelengths that plants react to (400 nm to 700 nm).When the radiant energy of a single wavelength within the visible spectrum is viewed by the human eye, it appears to be of a single spectral color. In plants, the radiant energy of a single wavelength is utilized to drive photosynthesis, a photochemical reaction within the chloroplasts of plant cells. A chloroplast is an organelle that contains stacks of membrane-bound compartments called thylakoids. The surface layer (membrane) of the thylakoid is where chlorophyll, the key photosynthetic photoreceptor, resides.
Chlorophyll absorbs radiant energy from the violet-blue and reddish orange-red wavelengths of sunlight. The energy is used to drive electrons, which are split from water molecules through photolysis, to react with nicotinamide adenine dinucleotide phosphate (NADP). The reaction changes this carrier molecule from its oxidized state (NADP+) to its reduced state (NADPH). Photolysis of water also produces oxygen as a byproduct and hydrogen ions (protons) which form a proton gradient (energy gradient). The proton gradient drives the generation of adenosine triphosphate (ATP) through the action of ATP synthase that is present in the thylakoid membrane.
Photosynthesis proceeds in two phases: the light dependent reactions (light reactions) and the light-independent reactions (dark reactions). Products of the light reactions, ATP and NADPH, are used to reduce carbon dioxide and convert it into glucose. Glucose is the energy source used by plants for cellular activities such as protein synthesis or cell division, it can also be passed into other biosynthetic pathways to form DNA. Complex carbohydrates formed by linked glucose molecules can be used to store energy for future needs (starch) or to build the cell wall of plant cells (cellulose). The series of reactions of using ATP and NADPH to produce glucose from carbon dioxide does not involve the use of light, and thus these reactions are called the dark reactions (also known as the Calvin cycle, named after Melvin Calvin who elucidated the pathway).
Plants also use light as a source of information to drive photomorphogenesis and photoperiodism. Photomorphogenesis refers to a developmental adaptation mechanism employed by plants to regulate seed germination, seedling development, organ orientation, cotyledon expansion, stem elongation, stomatal opening, root growth, and other morphological changes. Photoperiodism is rhythmic characteristic of biological processes developed by plants in response to the variations in day length and dark period. Photoperiodic control is commonly used in horticultural applications to steer plants from vegetative to reproductive growth for induction of early or out-of-season flowering.
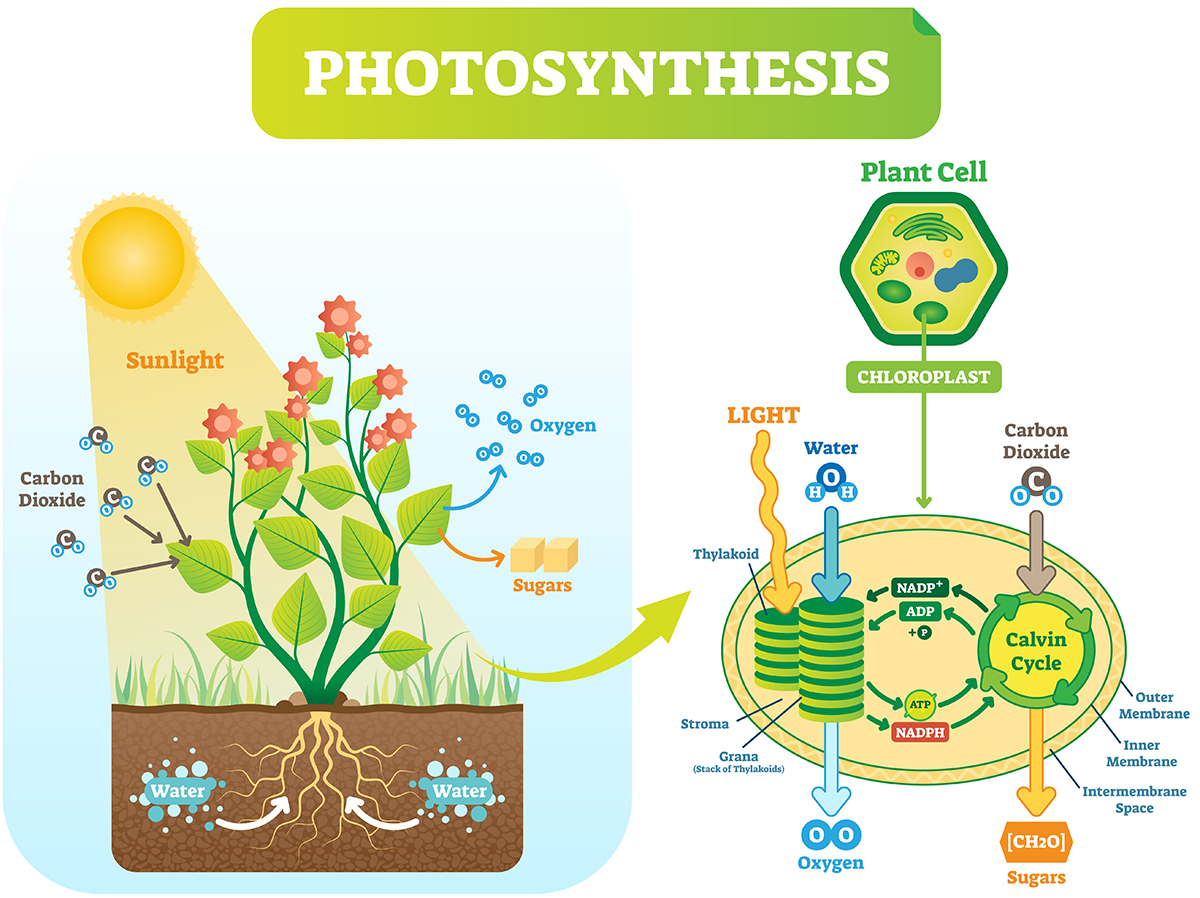
Photoreceptors
In essence, the purpose of horticulture lighting is to stimulate photoreceptors that drive photosynthetic activities, trigger photomorphogenic responses, or mediate photoperiodic signals. Plants have a suite of photoreceptors which absorb energy from or respond to light with specific wavelengths. The individual sensitivities of photoreceptor families provide opportunities to create a species-specific spectrum that works for every stage of plant growth.Chlorophyll is the key photosynthesis driver in plants. This complex molecule captures photons to generate high-energy electrons with great reducing potential and a proton-motive force across a thylakoid membrane, which are essential in the production of ATP and NADPH. Chlorophyll photoreceptors are most sensitive to photons with wavelengths in the red and blue regions of the spectrum. Chlorophyll is often referred to as a pigment because it reflects the wavelengths in the green part of the spectrum and therefore makes most plant appear green in color. Chlorophyll exists in two forms: chlorophyll A and chlorophyll B. Chlorophyll A, which resides in photosystems I (PSI or plastocyanin-ferredoxin oxidoreductase) and II (PSII or water-plastoquinone oxidoreductase), is the primary contributor to photosynthesis in the chlorophyll family. Chlorophyll B, which resides mostly in PSII, is called an accessory pigment. This pigment does not participate in photoactivation. The radiant energy it collected is passed on to chlorophyll A. Chlorophyll A has absorption peaks at 430 nm and 680 nm, and chlorophyll B absorps wavelengths at 450 nm and 660 nm most strongly. The ratio of chlorophyll B to A in plants is typically 1:3.
About 90% of radiant energy for driving photosynthesis is harvested is by chlorophylls, with 10% left to another group of accessory pigments known as carotenoids. Carotenoids are a large family of isoprenoids that are either pure hydrocarbon molecules (carotenes) or oxygenated derivatives of carotenes (xanthophylls). With a wide absorption range of 400–550 nm and an additional absorption peak at 675 nm, the photosynthetic activity of carotenoids effectively supplements that of chlorophyll which performs poorly at the green wavelength band. Carotenoids exhibit yellow, red or orange in color because they reflect the wavelengths in these bands. Aside from collecting excitation energy for photoactivation of chlorophyll, carotenoids are of particular importance for their ability to protect cells and DNA from damaging UV radiation and free radicals (molecules with unpaired electrons). When photosynthetic reaction centers are saturated with incoming energy, violaxanthin (a xanthophyll pigment) is de-epoxidated into zeaxanthin which then dissipates excess photons as heat.
It is worth noting that there are other antioxidants and photo-protectants such as anthocyanins and flavonoids which scavenge free radicals and dissipate harmful wavelengths to protect cells. These non-photosynthetic and non-photoreceptor pigments are secondary metabolites which are produced when photosynthetic reaction centers are overloaded with short wavelength photons. Anthocyanins and flavonoids absorb light in the blue and UV-B spectral bands and thus provide protection for organic molecules (proteins, DNA and RNA) against damage from UV-B radiation. When secondary metabolism of plants is triggered to produce anthocyanins and flavonoids, plants change in pigmentation. Leaves and flowers may have stronger colors such as yellow, red or violet.
When it comes to non-photosynthetic photoreceptors, phytochromes, cryptochromes and phototropins are the most researched. Phytochrome is a protein pigment that exists in two interconvertible forms: a red light absorbing form (Pr) and a far red absorbing form (Pfr) which is the physiologically active form of phytochrome. Phytochrome regulates germination, stem elongation, leaf expansion, flowering induction, circadian rhythm entrainment, chlorophyll biosynthesis, and shade avoidance syndrome. Cryptochromes and phototropins, which are both UV-A/blue-light photoreceptors, work in conjunction to mediate blue light-induced stomatal opening, inhibition of hypocotyl elongation, de-etiolation, phototropism, chloroplast movement, redox balance, the level of cyclic nucleotides, etc.
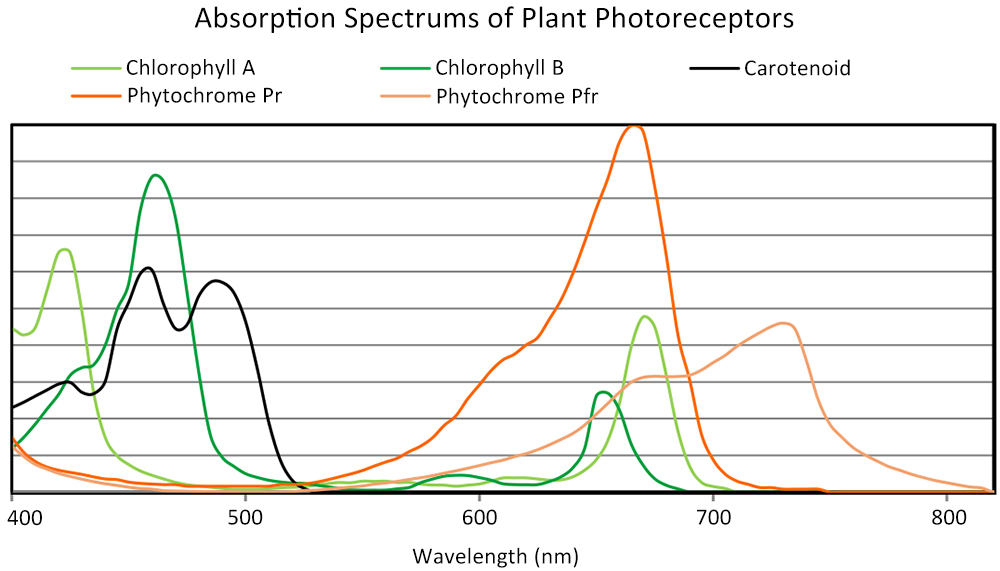
Photosynthetically Active Radiation (PAR)
The spectral range (wave band) of electromagnetic radiation from 400 nm to 700 nm is designated as photosynthetically active radiation (PAR). PAR is construed to provide a unified measuring system for quantifying the photosynthetic performance of horticulture lighting systems and irradiance (radiant flux incident on plants). It's important to note that wavelengths outside of the PAR region can be critical to plant development. The absorbance wavelengths of signal-transducing photoreceptors lay mostly outside of the PAR region. The active form of phytochrome has the absorption peak at 730 nm. Cryptochromes and phototropins have sensitivities that extend into the ultraviolet region (UV-A). Therefore, PAR-based lighting specifications should not be the sole reference when evaluating a grow light which is intended for triggering anatomical, physiological, or morphological responses in plants.The PAR metric system measures photon (quantum) flux, specifically, the quantity of photons in the wave band between 400 nm and 700 nm. The number of photons is calculated in moles or micromoles per second. One mole of photons is 6.0222×10²³ photons, hence one micromole of photons is 6.0222×10¹⁷ photons. Lighting manufacturers typically publish photosynthetic photon flux (PPF) and photon efficacy (PPF/W) values of their luminaires, whereas growers must additionally know photosynthetic photon flux density (PPFD) and daily light integral (DLI) values required by the plants. Because mounting distances have direct impact on the number of photons that reach plants, professional horticultural lighting manufacturers will provide PPFD data at difference mounting distances to facilitate growers' evaluation on the manufacturers' products.
Photosynthetic photon flux (PPF) is used to measure the amount of photosynthetically active photons coming from a light sources or lighting system. The unit used to express PPF is micromoles per square meter per second (μmol/s).
Photon efficacy (PPF/W) evaluates the ability of a light source or lighting system to convert the consumed electric power to photosynthetically active photons, expressed in micromoles per joule (µmol/J). This metric indicates the energy conversion efficiency of the light source or lighting system.
Photosynthetic photon flux density (PPFD), also referred to as quantum flux density, indicates the amount of photosynthetically active photons that fall on a square meter of the target area per second. The unit of this metric is expressed as "μmol/m2/s".
Daily light integral (DLI) measures the cumulative PPF that a plant receives over a 24-hour period. It is expressed in moles of photons per square meter per day (mol/m2/d).
Action Spectrum
The PAR metrics alone fail to reflect the effectiveness of a grow light because all photons within the PAR range are counted as photosynthetically active. As noted above, photoreceptors respond only to selective wavelengths, which means the unabsorbed wavelengths are wasted. Spectral efficiency, which refers to how well the spectral power distribution (SPD) overlaps with the desired action spectrum, is another critical component that goes into the design considerations of horticulture lighting systems. An LED grow light must provide targeted spectral output to stimulate photosynthesis and growth and/or to steer plant development and morphology. The PAR metrics tell the quantity of light, whereas the light spectrum tells the quality of light.LED grow lights can be categorized into full spectrum lights and narrow band lights. Full spectrum lights simulate the active part of solar electromagnetic spectrum and provide a balanced mix of all spectral colors. Full spectrum lights typically make efficient photosynthesis a high priority, but they does so in the context of addressing the morphological, physiological other non-photosynthetic needs of plants in almost every aspect of growth and development, from germination all the way through to harvesting. Narrow band lights have a very few color bands and deliver energy or signaling information that plants need in the exact spectrums that are most effective to induce the desired responses. Listed below are the primary color bands and their functions in horticulture lighting.
Red light (600 – 700 nm)
Photons with wavelengths in the 630 nm–680 nm color band yield the highest quantum efficiencies for driving photosynthesis. Photons with the wavelength at 660 nm can initiate conversion of phytochrome from its inactive form Pr to its active form Pfr, and in doing so induce a variety of photomorphogenic effects related to flowering, dormancy, seed germination, stem elongation, leaf expansion, and shade avoidance. Red light encourages rooting, budding, flowering and fruiting. Plants exposed to hyper red light often have rapid vertical growth, but with thinner stems and smaller leaves.Blue light (400-500 nm)
Blue light enhances chlorophyll absorption thereby driving photosynthesis, but it must be carefully controlled and mixed with other wavelengths because over-exposure to high energy blue wavelengths can inhibit plant growth. Blue light promotes stomatal opening, hence driving transpiration and improving access to carbon dioxide. Plants grown under high blue irradiation have smaller, thicker and darker green leaves, shorter leaf internodal lengths, and higher dry matter content. Exposure to blue light also stimulates the production of flavonoids and carotenoids. Stem elongation is controlled by blue light. A high ratio of blue light can be used to inhibit plant elongation and create a greater density of plants.Green light (500–600 nm)
Green light
Green light is of minor importance in photosynthesis but it does make a unique contribution. Green light can penetrate to interior leaf layers and drive photosynthesis of the inner canopy which is not reached by red and blue light. Absorption of green light can stimulate physiological responses, optimize stomatal aperture, enhance anatomical traits, encourage, long petioles internodes, contribute to developmental adaptation, and increase the concentration of hexadecatrienoic acid and yield of α-linolenic acid. The inclusion of green light in a red and blue wavelength mix produces white light which allows for visual assessment of the crop.Far red light (700-800nm)
Far red light is primarily used to target phytochromes for photoperiodic control of flowering time. The far red radiation can contribute to quick development of healthy plant biomass that results in larger blossom formations. Far red light also has photomorphogenic effects on elongation of stem and petioles.UV-A (320-400 nm) and UV-B (280 - 320 nm)
A large dose of UV light is harmful to the chemical bonds of molecules and to DNA structure. Moderate exposure increases the stress tolerance of plants and triggers protective mechanisms. Cryptochromes and phototropins react to UV-A. The UVR8 photoreceptor responds to UV-B.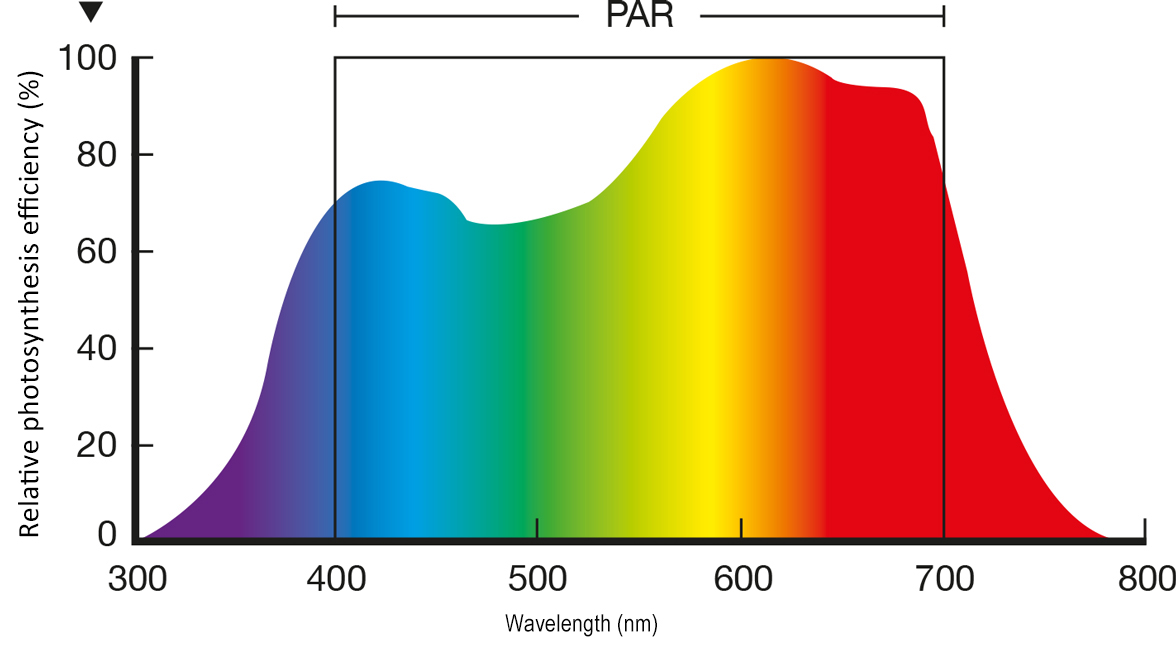
The Revolutionary Power of LED Technology
The use of LED technology is profoundly transforming the horticulture industry. The wavelength composition of LED lighting can be customized for either narrow band output with whatever spectral peaks or full spectrum radiation with whatever spectral ratios. This ability deems LEDs a spectrally efficient light source. A high spectral efficiency translates to minimal energy waste and effective photoreceptor stimulation. This trait is deficient in conventional horticultural lighting systems using high intensity discharge (HID) or fluorescent technology. High spectral efficiency and high electrical efficiency combine to give LED grow lights an incomparable advantage of high photon efficacy. It was the introduction of LED technology that enabled the horticulture industry to move towards sustainability. With unprecedented spectral versatility, LED lighting substantially contributes to the advance in precision agriculture technology in indoor farming facilities. Being able to target the wavelengths of all known photoreceptors in plants, LED horticulture lighting enables year-round sustainable cultivation of fruit, vegetable and flower with faster growth, maximized crop density, increased yield, and potentially better taste, color and nutritional content.Apart from its spectral advantages, LED lighting addresses the inherent limitation of both sunlight and conventional artificial light sources which radiate a large amount of infrared (IR) energy. Infrared light is the transfer of heat energy via invisible electromagnetic energy waves. Excess thermal radiation can damage plant cells or decelerate the rate of plant growth and development. Therefore HID lighting systems, such as high pressure sodium (HPS) and metal halide (MH) lamps, must be mounted at some minimum distance above the plants to mitigate their thermal impact. This inevitably results in more energy waste as these lighting systems have to use higher wattage light bulbs to ensure that a sufficient amount of photons land on the plant canopies. The minimum mounting distance requirement of these thermal radiators leads to a poor vertical space utilization and incurs an extra cooling cost.
LED grow lights produce no infrared radiation, which allows for fixture mounting at close proximity to plant canopy for maximum irradiance. This exclusive advantage of LED technology enables innovative implementation of lighting in green houses and indoor farms. In addition to toplighting, LED grow lights can be used for interlighting and multilayer applications. Interlighting (intracanopy lighting) refers to illumination on the side or in between the plants. LED interlighting encourages previously shaded leaves of tall plants (such as tomatoes, peppers, cucumbers and roses) to photosynthesize. LED lighting plays a key role in vertical farming, a multilayer plant production technology for indoor growing facilities where many racks of plants are stacked vertically. Absence of heat in radiant beams allows LED grow lights to be mounted into low-height plant racks and provide efficient, effective, and uniform photosynthetically, photomorphogenically, and photoperiodically active radiation.
The growing trend towards Internet of Things (IoT) and smart lighting sets the stage for LED grow lights which offer superior controllability in both light spectrum and light intensity. The digital nature of LEDs allows them to work seamlessly with other solid state circuits such as sensors, wireless communication modules, and microprocessors. Not only the wavelengths and radiance delivered by LED grow lights can be fine-tuned to drive intense photosynthesis and/or photomorphogenesis in plants, LED grow lights can incorporate IoT-based intelligence, operate on sophisticated algorithms, and respond to signals generated by computers and smartphones. LED-based digital lighting is an indispensable component of analytics-optimized, sensor-driven precision agriculture which helps grower handle a variety of tasks without any human intervention while creating opportunities for unprecedented cost savings.
Emission Mechanisms of LEDs
A light emitting diode (LED) is a solid state device that emits from a block of semiconductor rather than from a vacuum or gas tube. An LED produces light by exciting electrons from the conduction band of a negatively charged semiconductor layer to recombine with holes from the valence band of a positively charged semiconductor layer in the active region (p-n junction) of the diode. This is known as electroluminescense, which produce monochromatic wavelengths. LED are inherently narrow band emitters that produce single colors such as red, blue or green. The wavelength (or color) of the light is determined by the band gap of the doped semiconductor layers. Both the dopants and semiconductor materials contribute to the spectral output LEDs, this is where part of the spectral versatility of LEDs comes from. Shorter wavelength light, e.g. blue, green, is produced by indium gallium nitride (InGaN) LEDs, and long wavelength red light is produced by aluminum indium gallium phosphide (AlInGaP) LEDs.The highly coveted spectral advantage of LEDs also resides in their down-conversion and color mixing abilities. To produce full spectrum or polychromatic light, the InGaN LEDs can be coated with a phosphor layer which down-converts part of the short wavelengths into longer wavelengths. In this case, the spectral power distribution of an LED is determined the composition of phosphor down-converter. In the color mixing method, multiple colored LED chips are packaged as a single multi-channel emitter or LED packages of different colors are mounted close together. Each LED chip or LED package is individually controllable so that any color within the gamut of the constituent LEDs or any desired light spectrum can be generated through intelligent color mixing. Dynamic spectrum control allows specific spectral compositions to be created to induce the targeted responses at different stages of plant growth and development.
System Architecture
An LED grow light consists of an LED assembly, a heat sink, driver and control circuitry, and optics. The LED assembly is typically an array of LEDs which are solder mounted to a metal core printed circuit board (MCPCB). The optics which may include lenses and reflectors is used to improve light extraction, control beam spread, ensure uniform light distribution, and protect LEDs from environmental contaminants. The LED assembly is mounted to a heat sink which conducts heat away from the LED junction and then dissipates the heat to the ambient air through thermal convection and radiation. Often times LED luminaires have a fixture-as-heat-sink design in which the fixture itself is acting as the heat sink. The LED driver rectifies commercial AC power into DC power and then converts the rectified DC power into a predetermined magnitude of DC power typically through a switch mode regulator. The LED driver may be remote-mounted or co-located within the luminaire housing.Many consumers take it for granted that LED grow lights are high performing and long lasting. Just because that LED technology scores high in terms of energy efficiency, controllability, reliability, durability and lifespan, it doesn't mean an LED grow light will take over these advantages. LEDs are semiconductor devices that are very sensitive to current and voltage fluctuations. LEDs are also self-heating devices which generate a huge amount of heat at the semiconductor junction and phosphor layer. When LEDs are incorporated in a system, many failure mechanisms in LEDs can be triggered if the lighting system is not engineered to provide a robust platform for the LEDs. Aside from thermal degradation and electrical circuit failures, LEDs are susceptible to electrostatic discharge (ESD), humidity-induced corrosion, chemical degradation, temperature cycling, lense cracking, and manufacture defects such as poor intermetallic formation. These challenges impose high standards on design and engineering competencies across mechanical, electrical, thermal, and optical disciplines.
Light Source
Most of the LED grow lights available on the market use mid-power LEDs that are built on the PLCC (plastic leaded chip carrier) architecture. These surface-mount devices or SMD LEDs are nothing good but have a small footprint, a high initial light output and an attractive price point. The PLCC architecture comes with a number of failure and degradation points in its design. Mid-power LEDs are packaged in a plastic resin which most likely has a poor thermal stability as the majority of the Asian LED manufacturers use cheap the polyphthalamide (PPA) or polycyclohexylenedimethylene terephthalate (PCT) resin, rather than the more thermally stable but expensive epoxy molding compound (EMC). While discoloration of the plastic resin reflector is a dominant degradation mechanism in many mid-power packages, oxidation or corrosion of lead frames, bonding failures, and phosphor delamination can also lead to PPF deprecation, spectral shift and premature failures. The water is rough for the mid-power LED market. The use of mid-power LEDs is indispensable in light fixtures for interlighting and multilayer lighting applications. A good rule of thumb is to use products from time-tested brands only.In comparison to mid-power LEDs of which radiant flux degradation and color shift accelerate under high temperatures, high power LEDs have excellent PPF maintenance and spectral stability. Fabricated on ceramic substrates, these high flux density packages are characterized with high chemical and temperature stability as well as low thermal resistance. For light fixtures that require a high PPF output, high power LEDs are undoubtedly the choice. Chip-on-board (COB) LEDs are also high power packages but come with a large LES (large light emitting surface) that enables a homogenous light output. COB LEDs are fabricated on metal core printed circuit board (MCPCB) or ceramic substrate, which means a low thermal resistance and a high thermal dissipation efficiency. Chip scale package (CSP) mid-power and high power LEDs, which strip superfluous packaging elements and use flip-chip design, deliver the reliability comparable to ceramic-based LEDs but at a more competitive cost. However, the availability of CSP LEDs is limited at the time of writing as the technology is not mature yet.
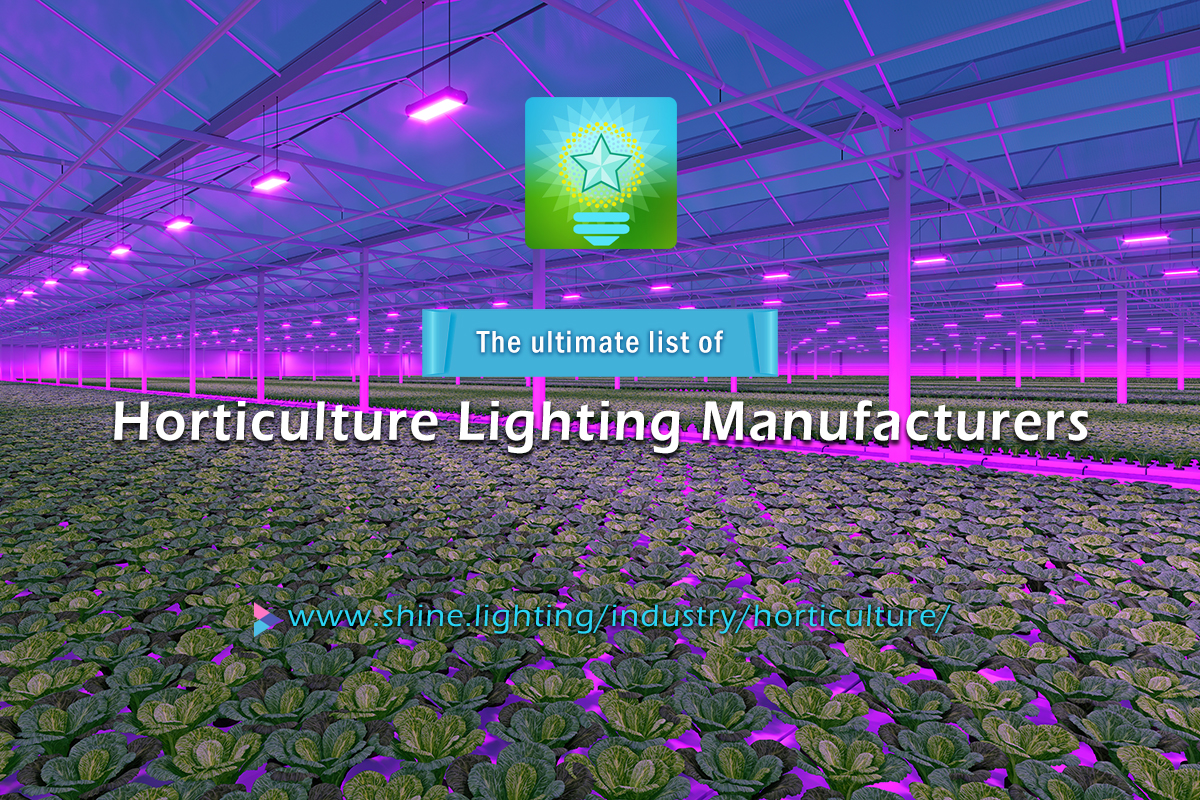
Thermal Management
Thermal degradation is the single largest failure mechanism in LEDs. The waste energy of LEDs is released as heat on the semiconductor packages, instead of be radiating as infrared energy via electromagnetic waves. Despite being an energy efficient light source, LEDs convert only around 40% of the consumed electrical power to light and the rest is converted into heat. As a byproduct of converting electricity into light, the waste heat can be a failure accelerator if allowed to accumulate. Excess thermal buildup can lead to thermal runaway, increased nucleation and growth of dislocations, phosphor or encapsulatant degradation, electromigration, and so forth. These thermal degradation effects cause efficiency drops (PPF depreciation), spectral shift, shorten lifespans, and even catastrophic failures. Operating an LED above the maximum allowable junction temperature will result in a 30% to 50% decrease in its useful life for every 10˚C increase.In addition to using LEDs with high thermal performance, thermal management at the system level is of critical importance and this is where part of the differentiation between a high-performing light and a poor-performing light comes in. Efficient removal of heat from the LED junction to the ambient environment requires the thermal resistance of all the components along the thermal path to be minimized to the lowest possible value. A high coefficient of thermal expansion (CTE) match and a low thermal contact resistance (TCR) between thermal conduction components are equally important to ensure the integrity and capacity of the thermal path. The former relates to the solder joints between the LED packages and MCPCB. The latter is about the thermal interface material (TIM) which is used to fill interfacial air gaps and voids between the heat sink and the MCPCB.
Heat sinks account for one of the biggest expenses in a bill of materials (BOM) of LED lighting systems. Unethical lighting manufacturers always attempt to reduce this expense by using more lightweight heat sinks or cheaper replacement materials (the use of thermoplastics in replacement of aluminum is a type of this practice). LEDs seldom fail abruptly even under high thermal stresses. The consequence of compromised thermal performance is usually unnoticeable in LED systems until after a year or several thousand hours of operation. That's why the market is being flooded with dirt cheap products, of which the initial performance appear to be acceptable but the cheat in thermal capacity eventually shows their true colors. A significantly shorter PPF maintenance or system life compared with products with adequate heat sinking performance is the reward for those go after petty advantages.
LED heat sinks are most often made of aluminum and its alloys which have thermal conductivities in the range of 90-240 W/mK. Aluminum heat sinks fabricated through cold forging or extrusion process have the highest thermal conductivities (often greater than 200 W/mK). However, most high power LED grow lights use die cast aluminum heat sinks. Die casting is the most cost-effective and efficient method for mass production of aluminum heat sinks. It also enables the inclusion of multiple design features found in plastics while providing effective heat transfer. The thermal conductivity of die cast heat sinks, depending on the compositions of aluminum alloys, ranges between 90 - 120 W/mK.
Thermal conduction performance is only one of the components in heat sink design. Conduction is a mechanism employed for heat transfer between solid components, e.g. from the LED chips all the way through MCPCB to the heat sink in an LED system. The waste heat eventually needs to be dissipated into the ambient air. The transfer of heat from heat sinks to the air requires thermal convection, the transfer of heat through the movement of liquid or air. The amount of convective heat transfer is dependent upon the mobility of the fluid (liquid or air) and the active surface area exposed to the flowing fluid. Passive heat sinks which dissipate heat through natural convection are always preferred for reliability and silent acoustics. For a passive heat sink to perform to their full capacity, its boundary design should be given special considerations. Passive heat sinks are frequently designed with fins or three-dimensional geometry to maximize the effective surface area of the hear sink boundary. However, CEA facilities, vertical farms and growth chambers are typically closed environment with no air movement. Forced convection, which relies on the movement of air created from a fan or synthetic jet, is therefore often used in high wattage horticultural lighting systems.
LED Driver
An LED is a current driven device, of which the light output is proportional to its forward current. LEDs also operate with a low forward voltage, below which little light is emitted and any fluctuation in the forward voltage will cause the forward current to change correspondingly. Adding to the challenge of LED load regulation is that forward voltage of the LED is easily affected by junction temperature. As LEDs are self-heating devices, the changes in junction temperature is inevitable. There're also discrepancies in the forward voltages of the red, green and blue LEDs which are often used in LED grow lights to produce dynamic light spectrums. As such, the LED driver must be designed to produce a dependable current output regardless the fluctuations of forward voltage. Tight current regulation provided by an LED driver is important to ensure a stable light output, it also makes sense to protect LEDs from thermal degradation due to overdriving and from catastrophic failures due to electrical overstress (EOS), electrostatic discharge (ESD), in-rush current, or other types of transient electrical surge.Although constant voltage LED drivers find their applications in horticultural lighting for driving a number of LED modules (e.g. LED tape lights) with a single power supply, most LED grow lights are operated by constant current LED drivers which regulate power to deliver a consistent, non-fluctuating LED load. An LED driver typically includes a rectifier to convert the AC mains voltage into an unregulated DC voltage and a filter capacitor to balance power between the pulsating input and the constant output for reduced double line frequency current ripple. The rectified voltage is then fed to a switching regulator which provides a substantially constant output by switching energy storage elements such as capacitors and inductors. A DC-DC converter that uses this type of voltage regulator is known as a switch mode power supply (SMPS). SMPS-based LED drivers offer a high efficiency of up to 95% and provide precise output under varying input voltage conditions (which means the driver can accommodate a universal input e.g. between 100V and 277V).
An increasing number of lighting manufacturers are proactively pushing their low cost products using a linear power supply. This type of products are often marketed as AC LED systems or driverless LED systems. However this is quite misleading. Every LED ultimately requires a DC constant current to provide a consistent output. These AC LED products still need to rectify AC power into a DC voltage. Their difference from SMPS LED drivers that the intermediary DC voltage is stepped down to a load voltage by a linear regulator. A linear LED driver requires the regulated voltage must be some minimum amount lower than the input voltage. That minimum amount is called the dropout voltage. Linear power supplies eliminate the use of large, reactive components such as coils, capacitors, inductors and switching transistors. This not only drives down the cost, parts count and volume of driver circuits, but also enables the limited number of driver components to be mounted on the same MCPCB with LEDs (known as driver-on-board or DOB).
Despite all the benefits that come with linear power supplies, it is not recommended to use this driving technology. Linear LED drivers are inherently inefficient because the dropout voltage, which accounts typically 20-30% of the consumed power, is simply thrown away as heat. The waste heat in turn imposes high thermal stress on the LEDs in a high power DOB system and thus requires additional heat sinking to draw it away. Linear LED drivers have a very limited range of input voltage because they only step down the voltage and require a minimum dropout voltage. There're also an electrical safety concern with linear LED drivers as they can not be galvanically isolated from the AC mains.
The LED driver is no longer a simple power supply, it is the brain for an LED lighting system. LED grow lights are typically implemented as dimmable systems that support pulse-width modulation (PWM) or constant current reduction (CCR) dimming. Integration of digital interfaces enables interaction with PAR sensors, humidity sensors and CO2 sensors. Connection to networking microcontrollers allows digital spectral control and dynamic DLI management through ZigBee, Wi-Fi, Bluetooth, and other wireless communication protocols.