Table of Contents Hide
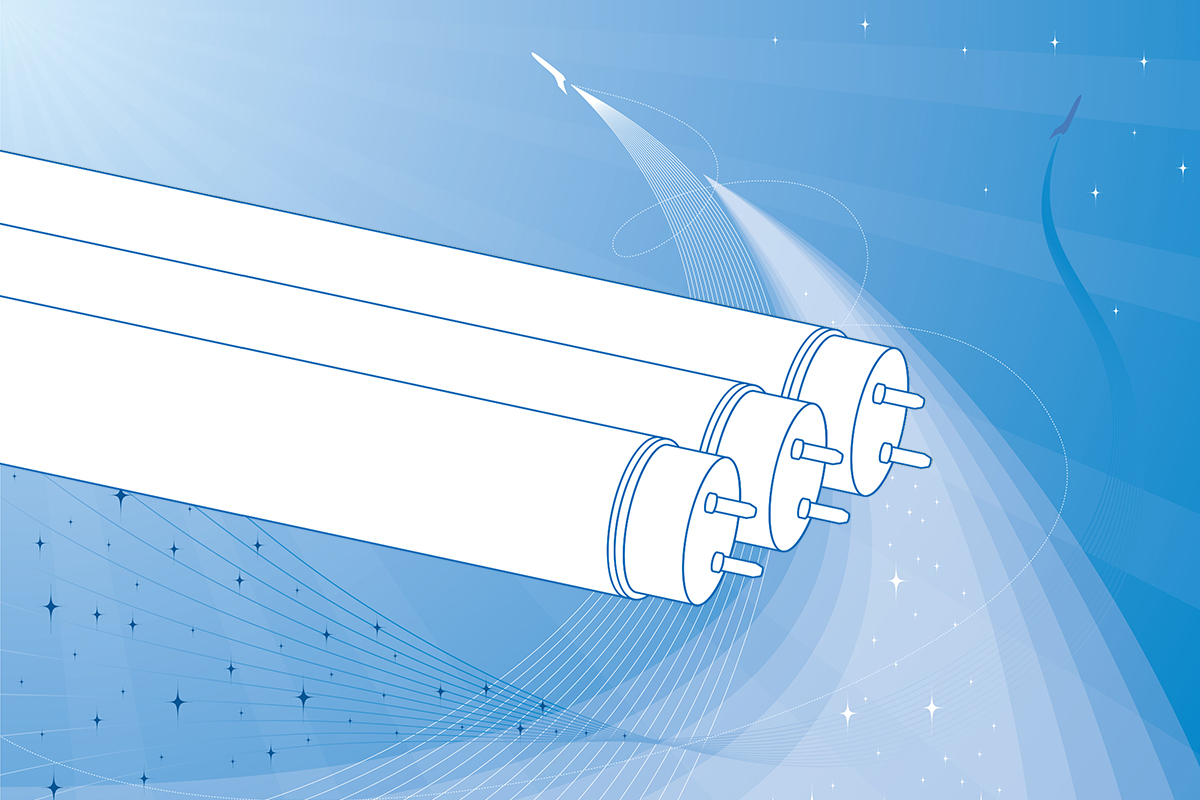
What Is an LED Tube Light
An LED tube light is an LED retrofit lamp that serves as a replacement light source for linear fluorescent lamps. LED tubes are designed to fit into the fluorescent sockets, effectively converting the light fixtures that originally accommodate fluorescent tubes into more energy efficient, longer life LED systems. As a product developed to address the needs of retrofitting existing fixtures, LED tubes have greatly simplified the job of lighting upgrade, whether the installation involves recessed troffers, wraparound fixtures, linear high bay lights, shop lights, or vapor tight fixtures. Despite the trend towards designing LED luminaires as integrated performance systems, LED tubes are still the workhorse in existing commercial, industrial and institutional buildings such as offices, hospitals, schools, shopping centers, retail establishments, warehouses, manufacturing and assembly facilities.Physical Specifications
As fluorescent tube replacements, LED tubes are also referred to as LED fluorescent tubes, notwithstanding they are no longer gas-discharge lamps but produce light from an array of semiconductor light sources. As lamp retrofits, LED tubes inherited the form factor and lamp base of linear fluorescent lamps. Until 1980, almost all fluorescent lamps used for general lighting were T12 lamps which are 1.5 inches (3.81 cm) in diameter. After then, the majority of new installations used T8 lamps which are 1 inch in diameter. Designed with the same G13 medium bi-pin base, T8 lamps are interchangeable with T12 lamps. This interchangeability combined with the ability of T8 lamps to provide more light and operate more efficiently than T12 lamps makes T8 lamps the dominant linear light source for both new construction and renovation projects. T8 lamps are typically available in imperial lengths of 2, 3, 4 and 5 feet, or in metric lengths of 600 mm, 900 mm, 1200 mm, and 1500 mm.In general, an LED tube light refers to the T8 type LED lamps if not specified, although T5 fluorescent lamps also have their LED replacements. Linear T5 LED lamps are 5/8 inch or 16 mm in diameter. They're not interchangeable with T8 LED tubes due to the shorter maximum overall length of the T5 (approx. 2" shorter) and the use of different pin spacing on the bases (T5 uses G5 miniature bi-pin bases).
Fluorescent Ballasts: the X-factor of LED Conversion
A fluorescent light fixture typically consists of a housing, an electronic ballast and at least one fluorescent light tube. The prominence of LED conversion for T8 fluorescent fixtures in the upgrade marketplace relies heavily on the handling of ballasts. The ballast is used to regulate the current going through the fluorescent lamp. It secures the lamp's supply current parameter limitation in a precise range so as to maintain the gas excitation while preventing the electric current from rising to destructive levels due to the tube's negative resistance characteristic. Electronic ballasts can be categorized into the instant-start type, the rapid-start type, and the programmed-start type. Instant-start ballasts work by applying a high starting voltage across a lamp having a single pin (the cold cathode) to start lamp arc without preheating the electrodes. A rapid-start ballast is designed for fluorescent lamps having a filament (two electrode pin lamp) and operates by applying voltage and heating the two electrode pins (the cathodes) simultaneously. A programmed-start ballast incorporates a cathode cut-out circuit and can precisely preheat the cathodes before the higher starting voltage is applied. It is a more advanced version of the rapid-start ballast. The predominant electronic ballast used in fluorescent light fixtures is the instant-start ballast because it provides maximum energy savings and operates lamps in parallel. Rapid-start ballasts, including programmed-start ballasts, will extend lamp life for circuits switched often, but are more expensive and cause increased energy consumption compared with instant start circuits.The electronic ballast is typically installed within the fixture housing and electrically connected to the power supply. This means to retrofit a fluorescent fixture the ballast should be bypassed with rewiring by a qualified electrician, or the LED tube must run off the existing fluorescent ballast so as to simplify installation and save labor cost. While most end users prefer the plug-and-play, direct replacement solution that has the lowest initial cost, a lot of issues may arise due to the incompatibilities between the electronic ballast and LED driver. The electrical incompatibilities constitute the safety, efficiency and reliability issues facing linear LED retrofit solutions. Another electrical wiring point of interest is whether the lamp holder (tombstone) configuration is shunted or non-shunted. Fluorescent lamps operated by instant-start ballasts are installed in shunted lamp holders where both pins are wired together to connect with the single circuit in the ballast. Rapid-start lamp holders are non-shunted sockets. Two pins of the socket connected to the rapid-start ballast receive power while the corresponding pins on the other socket serve to physically secure the tube only. Therefore whether the lamp holder is shunted for instant start fluorescent ballasts or un-shunted for rapid start ballasts also affect the compatibility with LED tubes. Generally, lamp holders that accommodate LED tubes are of the non-shunted type.
Types of LED Tube Lights
A lighting upgrade involves considerations on the financial aspect as well as the installation, operations, and maintenance implications. Whether to connect or bypass the existing fluorescent ballasts is not just about saving the installation cost or not, but also affects the energy efficiency, electrical safety, operational features, and maintenance cycle of the LED retrofit tubes. LED tube lights can be grouped into four categories depending on the ballast compatibility and driver integration: Type A (Ballast Compatible), Type B (Ballast Bypass), Type C (External Driver), and Dual Mode (Type A + Type B).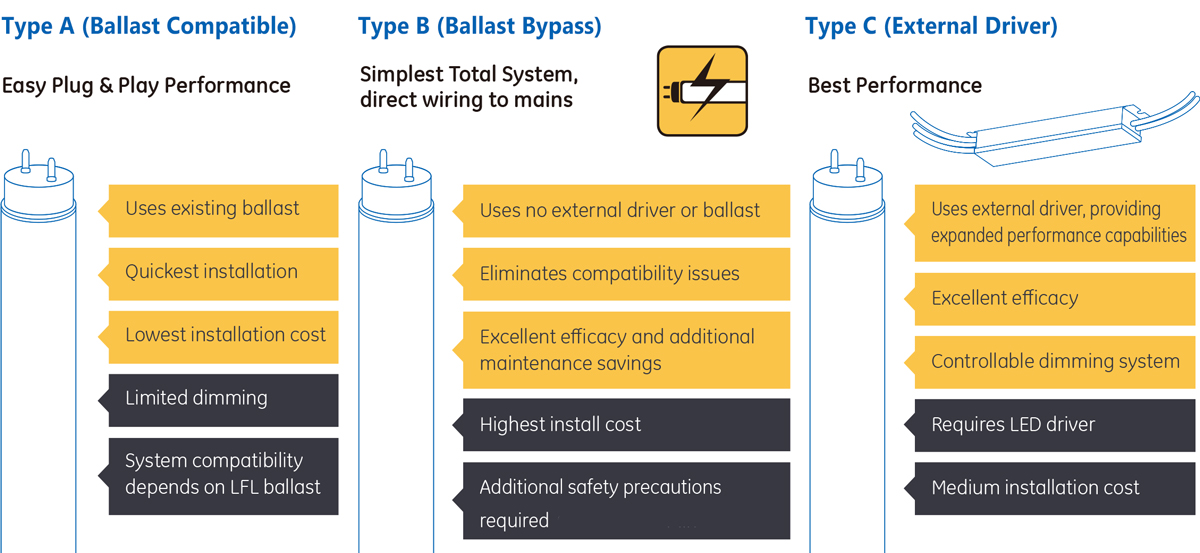
Infographic courtesy of GE Lighting
Type A (Ballast Compatible)
Type A LED tubes offer a plug-and-play solution for their ability to operate directly from the existing linear fluorescent ballasts. A retrofit is carried out by simply removing the existing fluorescent tube and replacing it with the LED tube. The existing wiring remains intact and no structural modification of the existing fixture is required. The integral drivers of Type A LED tubes convert the AC voltage coming from the fluorescent ballast to DC current. The compatibility between the driver and ballast is brought on by the additional circuitry included in the driver. The circuitry is capable of simulating the electrical characteristics of a fluorescent lamp. This tricks the ballast into thinking it's still operating a fluorescent lamp.At first glance, the plug-and-play lighting upgrade with Type A LED tubes looks appealing. Nevertheless, when components designed for fluorescent systems are adapted for use with LED lamps there're uncertainties and compromises. The compatibility issue is particularly problematic because all ballasts are not created equal. The lifetime benefit of LED lighting may not be available on ballast-compatible LED tube lights as these lamps will not work without a working ballast. When the ballast in a fixture dies, the LED tube fails as well. A ballast constantly draws power, which causes additional power loss (an additional 2 - 3 watts per lamp). Another major customer dissatisfaction with ballast compatible LED tubes is their poor dimming performance. Most type A LED tubes will not respond to dimming ballasts. In the long run, a low upfront cost of type A LED tubes usually does not translate into a corresponding return on Investment (ROI) that people would expect from LED lighting.
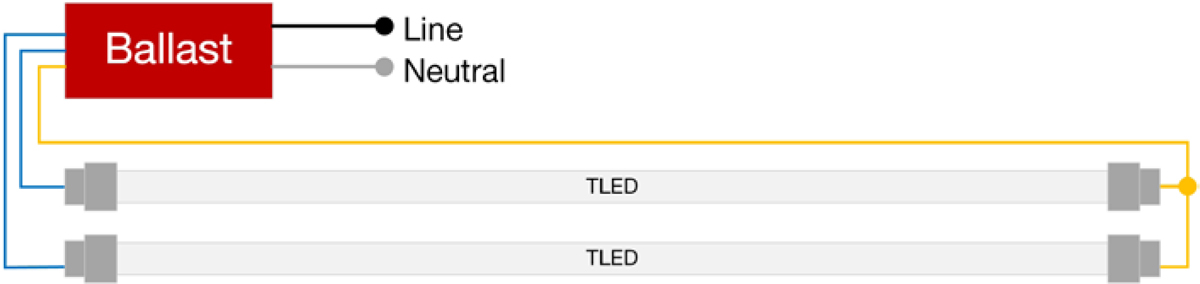
UL Type A LED tube wiring example (Image courtesy of Lutron Electronics)
Type B (Ballast Bypass)
Type B LED tubes operate with an internal driver which is powered directly from the main voltage supplied to the fixture. This involves electrical modification to the existing fixture in order to remove/bypass the ballast and connect the LED driver to the power supply. Type B LED tubes can be either single- or double-ended. A single-end LED tube is designed to put mains voltage across the two pins on one end while the other end becomes a dummy end and is only used for holding the tube in place. There is no shock hazard with the single-end circuit design when retrofitting to LED systems. However it can be dangerous when a T8 fluorescent tube is re-inserted into a single-end wired fixture. This may cause the fluorescent tube to fire up and eventually go into a runaway mode that leads to wires melting, fuse blowing or severe arcing. A double-end LED tube is designed to having power running to both ends. Electrical safety is a concern here. When one end of the LED tube is inserted or removed from the socket while the power is on, an electrical shock hazard can result from touching the other end of the tube. Therefore, a double-end ballast bypass LED tube must have an internal safety switch so as to provide shock hazard protection for the installer. The safety switch is designed to prevent electric current from flowing through the lamp before socket engagement of both ends of the LED tube.Type B LED tubes provide the longevity and efficiency that come with LED technology because they operate independently of the life-limited and power-consuming ballasts. This design eliminates any compatibility issues that occur in retrofitting fluorescent fixtures with type A LED tubes as well as saves on maintenance costs associated with ballast replacements. Nevertheless, a retrofit with a type B LED tube involves a high installation cost because of high-voltage wiring. Type B LED tubes require sockets dedicated to the technology. Very often sockets should be replaced since the majority of fluorescent fixtures use instant-start ballasts. Instant-start ballasts require shunted sockets whereas single-end LED tubes are typically designed to work on non-shunted sockets which are also used by rapid-start ballasts. Double-end LED tubes are generally compatible with both shunted and non-shunted sockets because the two pins on each end of the LED tube have the same polarity. Most type B LED tubes have narrow dimming and control capabilities due to the availability of space for sophisticated dimming and control circuitry.
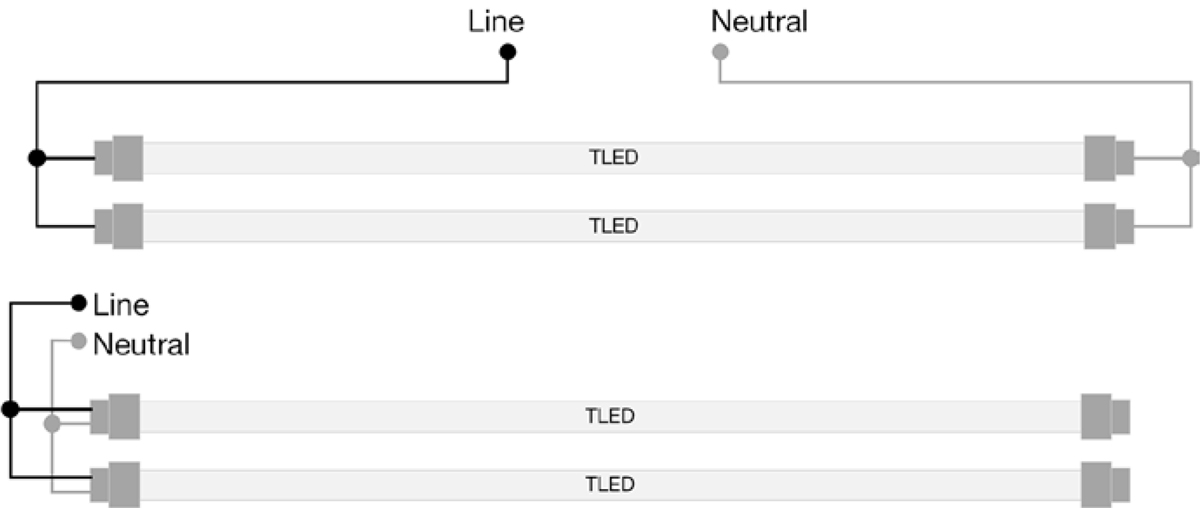
UL Type B LED tube wiring example (Image courtesy of Lutron Electronics)
Type C (External Driver)
Type C LED tubes are designed with a remote driver, rather than an integral driver. The ballast on an existing fixture must be removed and input wires must be connected to the LED driver. This must be done before installing the new LED linear tubes so that low-voltage outputs of the driver are connected to the sockets instead of line voltage. While this LED retrofit solution is the most labor-intensive and involves a relatively high cost, it offers predictable and warrantied performance. Remote placement of the driver allows for a less challenging thermal environment for the driver electronics. This design extends the lifespan of circuit components e.g. electrolytic capacitors, which are highly sensitive to the operating temperature. Because the driver is not confined to a small space, it can incorporate a variety of features, including robust dimming and control functionality, transient voltage suppression, etc.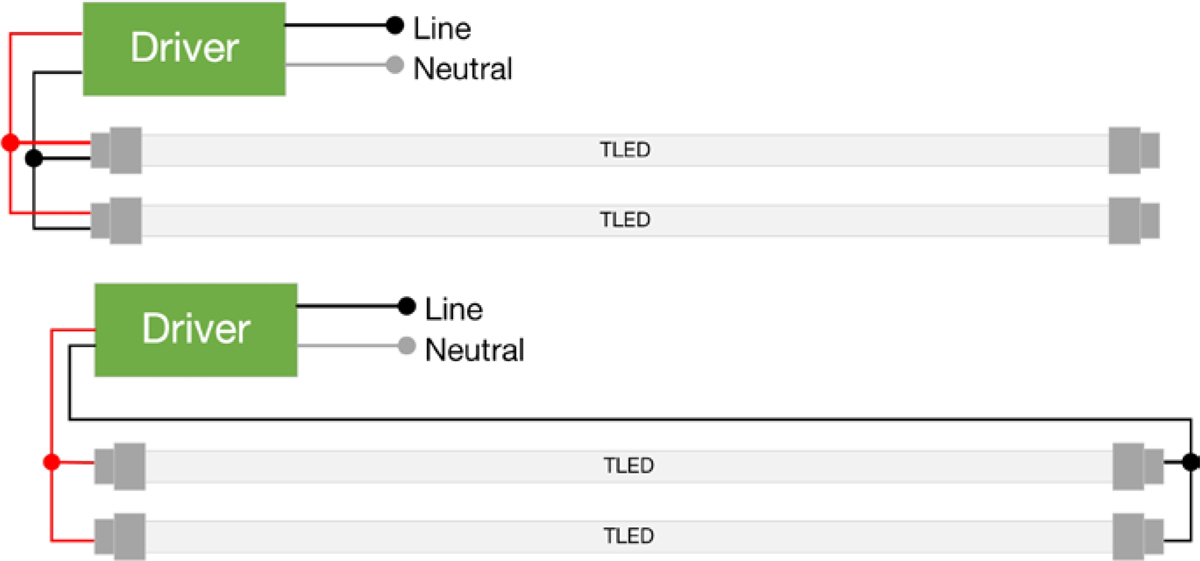
UL Type C LED tube wiring example (Image courtesy of Lutron Electronics)
Dual Mode
A dual mode LED tube can work with or without a ballast. It is equipped with an internal driver that automatically adapt to either ballasted fixtures or direct AC line voltage. Dual mode LED tubes offer a flexible solution for the lighting retrofit market. They can run off with compatible ballasts and require no modifications or rewiring to the existing fixture. They can be also powered directly from the main voltage for higher efficiency operation. Dual mode LED tubes must have a safety feature required for protection against electrical shock during high-voltage wiring. In general, the driver circuitry of dual mode LED tubes is too complicated to ensure the cost effectiveness and sometimes the system safety and reliability.Design and Construction
LED tubes come in two types of housings: hybrid aluminum/plastic and full plastic/glass. An LED tube with a hybrid aluminum/plastic construction has an exposed, D-shaped aluminum housing which integrates with a polycarbonate lens to form a tubular housing. The extruded aluminum housing has a cavity that is used to accommodate the driver circuit. The driver circuit that runs through the aluminum housing is enveloped with an insulation sleeve to isolate the circuit from touchable metal parts. A linear LED module, which consists of an array of SMD LED packages which are solder mounted onto a metal-core printed circuit board (MCPCB), is attached to the flat bottom of the aluminum housing. The bottom of the aluminum housing can also be slotted to receive the LED module while the two sides adjacent to the slot are angled to shape the beam and provide optical reflection. The LED tube with a full plastic or glass housing has a built-in aluminum plate that holds the linear LED module and provide heat dissipation. The driver circuit is side-mounted into one of the end caps which have a length longer than those of tubes with a hybrid aluminum/plastic construction.The aluminum housing of the hybrid construction type provides efficient heat dissipation for the LEDs. The large surface area of the exposed aluminum extrusion enhances convective heat transfer which is extremely important in thermal management. A disadvantage of this design is that the internal parallel driver may be stressed by the thermal load of the LEDs. The driver is confined to a small space and thus is in close proximity with the heat source. Electrolytic capacitors are widespread used in LED drivers because they provide the necessary large capacitance (hundreds and even thousands of micro-Farad) as energy storage devices and buffers. The life of an electrolytic capacitor is heavily affected by its operating temperature. While good quality electrolytic capacitors may survive high temperature operation, most LED tubes are equipped with low cost capacitors that can degrade fast and result in light flickering, short circuits, compromised isolation ability, etc.
Full glass/plastic tubes with an internal end-cap driver are at another extreme. The side-mount design allows the driver be located away from the LEDs, drastically reduces the thermal stress on the driver, and provides enhanced electrical insulation. However, the enclosed glass or plastic housing limits transfer of LED waste heat to the ambient air through convection. The full PC housing is prone to bending and warping especially at longer lengths despite the claim that nanoplastic tubes provide better bending endurance. Glass construction provides rigidity. The glass tube is typically PET coated to create a protective envelop.
Depending on the application, the glass or polycarbonate lens may be frosted or in a clear finish. Frosted lenses obscure the LED hot spots from view and aid in uniform light distribution, but the diffusion may result in an optical loss of about 15%. LED tubes with clear lenses provide a high optical efficiency but the harshness of LEDs can be visually uncomfortable. They are typically placed behind a glass or plastic lens of a light fixture. The beam angle of LED tube ranges from 105° to 320°. LED tubes with rotatable end caps allow for optical aiming.
LED Driver
The design of an LED driver involves many variables, including cost, size, parts count, efficiency, power factor (PF), total harmonic distortion (THD), input voltage range, flicker, dimming capabilities, electromagnetic interference (EMI), and operating temperature. LED tubes run off a constant current source which is typically configured as a switching mode power supply (SMPS). AC mains-connected LED drivers may be of a single-stage type or of a two-stage type. An SMPS LED driver that is used to operate an LED tube require a low cost, low parts count solution to provide regulated DC output power with low ripple, good power factor correction and moderate line current distortion. A single-stage LED driver performs both power factor correction (PFC) and switching regulation in one circuit. The two-stage system uses two separate circuits for PFC and DC-DC conversion.Single-stage LED drivers save 20-50% of the circuit parts count, size and cost, when compared to two-stage LED drivers. The one-step conversion also maximizes circuit efficiency. Single-stage drivers however, do not provide complete suppression of the alternating waveform after rectification. The output current may contain large ripple that results in light flicker at twice the line frequency. Good circuit designs can reduce the ripple to a relatively low value; however, the ripple is generally still higher than the two-stage solution. The two-stage solution has an active PFC stage designed to correct phase errors and reduce harmonics, and provides a near unity power factor across a universal input voltage range. The DC-DC converter stage is used to provide tight regulation with minimal ripples in the output current provided to the LED load. The extra output stage substantially increases the cost and size of the driver and causes additional efficiency loss. Nevertheless, the two-stage design offers a fair trade for better quality light output (less flicker) and allows smooth, deep dimming in almost every output current range.
The DC-DC converter stage is typically buck-boost (Cuk, SEPIC) or flyback topologies. However, the high-speed switching operation through which the predetermined magnitude of DC power is generated can produce electromagnetic emissions that will require additional EMI filtering to mitigate. For safety, it is desirable to provide galvanic isolation between the input and the output circuits. Low-cost drivers are usually designed with no galvanic isolation. This may be result in electrical shock hazards when touching the exposed aluminum heat sink of an LED tube in the event of a dielectric breakdown of electrical insulation. A line-powered LED driver that is galvanically isolated also offers additional protection from transient voltages/power surges for its circuit components as well as downstream components.
Light Source
LED tubes use variants of SMD LEDs designed in an industrial standard footprint, e.g. 2835, 3528, 4014, and 5050. These mid-power LEDs are ubiquitously employed in indoor applications for their low cost, high efficacy and high design flexibility. However, a variety of package-related failure mechanisms occur in mid-power LEDs. Mid-power LEDs currently available on the market are plastic leaded chip carrier (PLCC) packages which include a plastic housing and lead frame. The plastic housing functions as a reflector to enhance light extraction and serves as a protective barrier against external mechanical stresses. The metal-plated lead frame provides electrical connection, thermal dissipation and light reflection. The highly reflective plastic housing and lead frame combine to maximize photon extraction efficiency and contribute to the high initial lumen/watt of PLCC packages.The use of plastic housing and metal plating allows mid-power packages to deliver the highest luminous efficacy among LEDs built on different package platforms. Unfortunately, they're also the least reliable products since the plastic housing and metal plating are inherently less resistant to chemical contamination and thermal stress. While LED tubes made with mid-power LEDs deliver luminous efficacies sufficiently high to be qualified for various energy efficiency programs or standards, e.g. the Qualified Product List (QPL) of DesignLights Consortium (DLC), the light output of plastic LED packages degrades fast because package material deterioration causes loss of reflectivity. In addition to lumen depreciation, the accompanying color shift (the change in the chromaticity coordinates from its original values) can be more of a concern because significant color deviations render the light quality unacceptable and thus limit useful lifetime of LED tubes. At high temperatures the white reflective housing made of a synthetic plastic resin will discolor, which is the dominant color shift mechanism in the mid-power LED packages. The resin discoloration results in a blue chromaticity shift. Oxidation of exposed lead frames can also produce chromaticity shifts (CSM-4 behavior).
To achieve an excellent lumen maintenance and color stability with PLCC LED packages, the housing must be molded from a polymer resin that has a high resistance to thermal degradation and photo-oxidation. Common polymer resins used in PLCC packages include polyphthalamide (PPA), polycyclohexylenedimethylene terephthalate (PCT), and epoxy molding compound (EMC). Mid-power LEDs based on EMC resin are more resistant to thermal degradation than PPA and PCT but come with a higher cost that makes it hard to justify their use in LED tubes. With cheap PPA or PCT-based LED packages, the drive current must be kept low and thermal management must be efficient enough to keep the LEDs in a safe operating zone and thus delay the onset of lumen degradation and chromaticity shift.
Color Quality
The color quality of a light source can be characterized by its color rendering performance and by its color uniformity. Except for products developed for niche markets, LED tubes are designed at the lower limit of acceptability for color quality as a result of the compromise toward cost and efficiency. A color rendering index (CRI) of 80 is the minimum acceptable value for general interior illumination in commercial and institutional applications. However, typical 80 CRI LEDs are over-saturated in the blue and green spectrums and deficient in key wavelengths for saturated colors that are important to our perception of the world around us. When faithful color reproduction is essential in applications like retail display lighting, a minimum CRI of 90 and a moderate R9 value (e.g. 25) is required.LEDs are binned for their correlated color temperature (CCT) to ensure color uniformity from lamp to lamp as well as minimal color variations across the entire run of the LEDs within a tube. LED tube manufacturers seldom specify the chromaticity binning tolerance for their products because setting the specification too tightly will increase the cost. LEDs used in LED tubes are binned to somewhere between a 6-step MacAdam ellipse (6 SDCM) and an 8-step MacAdam ellipse (8 SDCM).