Table of Contents Hide
- 1 Hazardous location lighting
- 2 Diverse applications
- 3 Compliance with regulations
- 4 NEC Class/Division
- 5 ATEX/IECEx Zone system
- 6 LED lighting
- 7 Design and construction
-
8
Types of hazardous location LED lights
- 8.1 High bay lights
- 8.2 Low bay lights
- 8.3 LED flood lights
- 8.4 LED area lights
- 8.5 Portable work lights
- 8.6 LED task lights
- 8.7 Emergency lights
- 8.8 Exit signs
- 9 Explosion-proof LED lights
- 10 Intrinsically safe LED lights
- 11 Class I, Division 1 LED lights
- 12 Class I, Division 2 LED lights
- 13 ATEX-certified LED lights
- 14 NEMA-rated LED lights
- 15 IP-rated LED lights
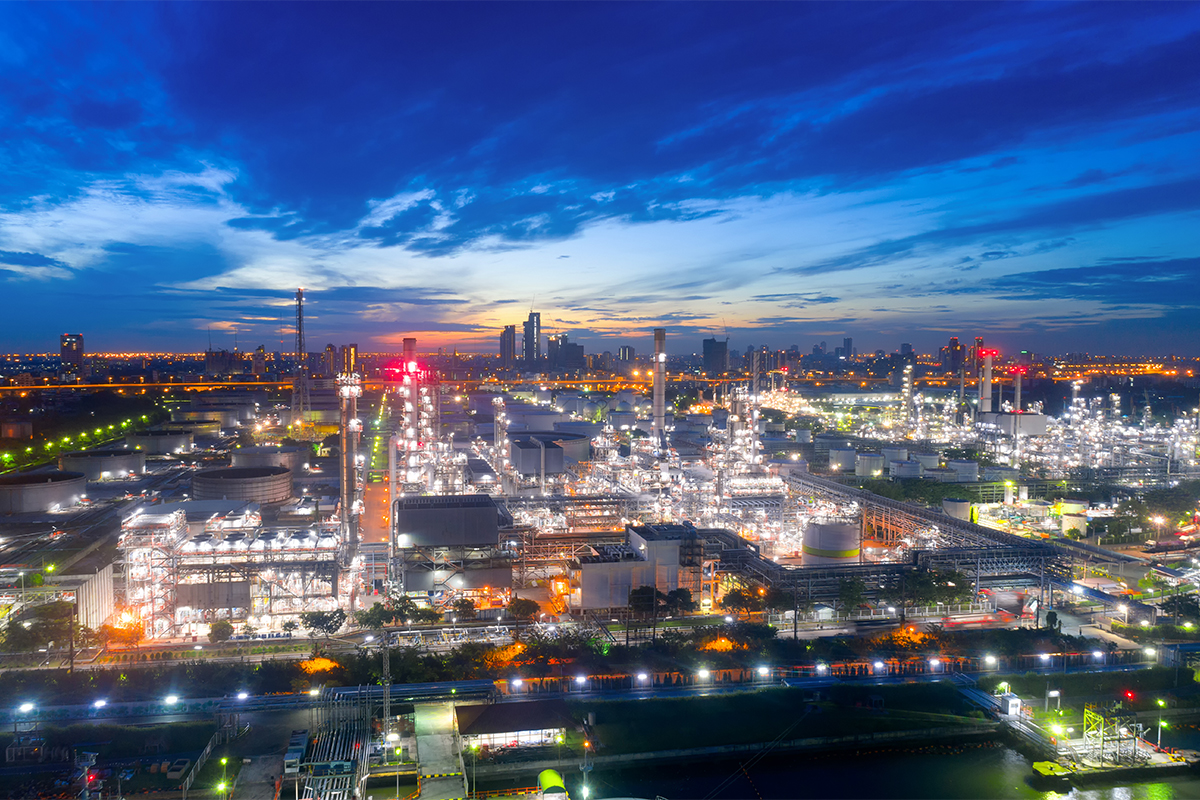
Hazardous location lighting
Hazardous location lights are specifically designed and certified for use in environments where there is a risk of fire or explosion due to the presence of flammable gases, vapors, liquids, combustible dust, or fibers. Hazardous location lighting ensures that areas with the potential for fire or explosion remain adequately illuminated while reducing the risk of igniting the hazardous substances in the atmosphere. This is achieved through the use of specialized lighting fixtures that meet stringent safety standards and are designed to operate safely in these challenging environments. The key principles behind how hazardous location lighting works involve design features and safety measures to prevent ignition sources and minimize the risk of explosion or fire. Hazardous location lighting fixtures are constructed with materials and designs that prevent sparks or hot surfaces from igniting flammable substances in the surrounding environment. This may include heavy-duty housings, sturdy enclosures, and specialized seals to contain any potential explosion within the light fixture. Hazardous location lighting allows workers to see clearly, navigate safely, and perform tasks effectively, reducing the likelihood of accidents and injuries. In addition to safeguarding human lives, hazardous location lighting also helps protect valuable assets and infrastructure from damage or destruction in the event of a fire or explosion.Diverse applications
The applications of hazardous location lighting fixtures involve settings where there is a potential risk of fire, explosion, or other hazardous conditions due to the presence of flammable gases, vapors, combustible dust, ignitable fibers, or similar substances. From oil and gas facilities dealing with flammable gases to chemical plants handling hazardous substances, from manufacturing plants with combustible materials to mines with explosive gases, specialized lighting fixtures are indispensable. They provide illumination without posing a risk of ignition, reducing the likelihood of fire, explosion, or accidents. Whether in marine environments, aircraft hangars, utilities and power plants, warehouses, pharmaceutical facilities, or wastewater treatment plants, hazardous location lighting fixtures are meticulously designed and certified to meet stringent safety standards. By minimizing the risk of sparking or overheating, these fixtures contribute significantly to maintaining a safe working environment in industries where hazardous conditions are prevalent.Oil and gas facilities
Oil and gas facilities are inherently high-risk environments due to the presence of flammable gases and vapors, which significantly increase the potential for fire and explosion hazards. To mitigate these risks, the implementation of hazardous location lighting is essential across various areas such as drilling platforms, refineries, and storage tanks. These specialized lighting solutions ensure adequate illumination while minimizing the risk of ignition, thus enhancing safety for workers and protecting valuable assets in the industry.Chemical plants
Chemical plants pose significant safety challenges due to the presence of hazardous chemicals and vapors, necessitating specialized lighting solutions to mitigate the risk of ignition and ensure the safety of personnel and infrastructure. Implementing appropriate hazardous location lighting is crucial to minimize potential hazards and maintain a safe working environment within chemical plants, thereby safeguarding both human lives and valuable assets.Manufacturing plants
Manufacturing plants handling combustible dust or hazardous materials require lighting fixtures designed to operate safely in such environments. Hazardous location lighting plays a critical role in providing illumination without posing risks of sparks or overheating, thereby significantly reducing the potential for accidents. By implementing these specialized lighting solutions, manufacturing plants can enhance workplace safety and mitigate the inherent risks associated with handling combustible materials, ensuring the well-being of workers and the protection of valuable assets.Mining operations
Mining operations face inherent risks associated with explosive gases or dust in their environments. To ensure safety, hazardous location lighting is imperative to provide illumination without igniting potentially hazardous materials. By implementing specialized lighting solutions designed for such conditions, mining operations can significantly reduce the risk of accidents and protect the well-being of workers, while also safeguarding valuable assets within the industry.Marine environments
Marine environments, including ships and offshore platforms, present unique challenges due to the presence of flammable substances, which heightens the risk of fire or explosion. Lighting fixtures in these settings must adhere to stringent safety standards to mitigate the potential for accidents. Ensuring that lighting fixtures meet these safety requirements is essential for enhancing maritime safety, protecting personnel, and safeguarding valuable marine assets. By implementing appropriate lighting solutions, marine operators can effectively minimize risks and maintain a secure environment onboard ships and offshore structures.Aircraft hangars
Aircraft hangars, where aircraft are stored and maintained, often contain fuel vapors and other flammable materials, posing significant safety risks. Therefore, specialized lighting solutions are indispensable to ensure safety by preventing ignition and potential accidents. Implementing appropriate lighting fixtures designed for hazardous environments is essential to mitigate these risks effectively. By prioritizing safety through the use of specialized lighting, aircraft hangars can provide a secure environment for personnel and protect valuable assets, thereby enhancing overall safety standards in aviation operations.Utilities and power plants
Utilities and power plants, involved in energy generation or distribution, often contend with areas containing hazardous materials, necessitating robust safety measures. Hazardous location lighting emerges as a critical component, ensuring safe illumination without risking ignition in these environments. By employing specialized lighting solutions tailored to hazardous conditions, utilities and power plants can significantly mitigate the risk of accidents and safeguard both personnel and infrastructure. Prioritizing the implementation of hazardous location lighting underscores a commitment to maintaining a secure working environment and upholding safety standards in energy operations.Warehouses and storage facilities
Warehouses and storage facilities storing combustible materials, chemicals, or hazardous goods face inherent safety challenges. To mitigate the risk of fire or explosion, specialized lighting solutions designed for safety are imperative. Hazardous location lighting plays a pivotal role in reducing these risks by providing illumination without compromising safety in such environments. By implementing appropriate lighting fixtures, warehouses and storage facilities can enhance safety standards, protect personnel, and safeguard valuable assets, ensuring a secure working environment for all involved.Pharmaceutical facilities
Pharmaceutical facilities, where manufacturing processes are delicate and precise, demand strict adherence to safety standards, including lighting requirements. Hazardous location lighting stands out as essential in meeting these standards, ensuring compliance and minimizing the risk of accidents. By implementing specialized lighting solutions designed for hazardous environments, pharmaceutical facilities can create a safe working environment for personnel and protect the integrity of their operations. Prioritizing the use of hazardous location lighting underscores a commitment to safety and regulatory compliance, enhancing overall operational reliability and safeguarding the quality of pharmaceutical products.Wastewater treatment plants
Wastewater treatment plants face unique challenges due to the presence of potentially hazardous gases or chemicals, necessitating stringent safety measures. Hazardous location lighting emerges as a critical component in mitigating these risks, providing illumination without posing a hazard in volatile environments. By utilizing specialized lighting fixtures designed for hazardous conditions, wastewater treatment plants can enhance safety standards, protect personnel, and safeguard critical infrastructure. Prioritizing the implementation of hazardous location lighting underscores a commitment to safety and regulatory compliance, ensuring the efficient and secure operation of wastewater treatment facilities.Compliance with regulations
Industries across various sectors are subject to stringent regulations aimed at ensuring workplace safety. These regulations cover a wide range of aspects, including the design, operation, and maintenance of facilities, equipment, and systems. Lighting requirements in hazardous locations are among the many specific safety regulations that industries must adhere to. The primary purpose of workplace safety regulations, including those related to lighting in hazardous locations, is to protect workers from harm. Ensuring adequate lighting in areas where there's a risk of fire or explosion helps minimize accidents, injuries, and fatalities by providing visibility and reducing the likelihood of mishaps. In hazardous environments where flammable gases, vapors, liquids, combustible dust, or fibers are present, the risk of accidents, such as slips, trips, falls, or collisions, is heightened. Proper lighting helps workers identify potential hazards, navigate safely, and perform tasks with greater accuracy, reducing the likelihood of accidents. Adequate lighting is crucial for early detection and mitigation of fire and explosion risks. Illuminated areas allow for better monitoring and surveillance, facilitating prompt intervention in case of emergencies. Additionally, lighting fixtures designed for hazardous locations are constructed to minimize the risk of ignition, further mitigating the potential for catastrophic events. Governments and regulatory agencies impose safety regulations to ensure that businesses and industries operate responsibly and protect the well-being of their employees and the surrounding community. Compliance with these regulations, including lighting requirements in hazardous locations, is mandatory and subject to enforcement through inspections, audits, and penalties for non-compliance. In addition to regulatory requirements, industries often follow industry-specific standards and best practices developed by organizations, professional associations, and technical committees. These standards provide guidance on various aspects of workplace safety, including lighting design, installation, and maintenance, to enhance overall safety performance.NEC Class/Division
The National Electrical Code (NEC) mandates the classification of these hazardous areas and provides guidelines for the types of lighting fixtures permitted in them. This classification ensures that appropriate safety measures are in place to minimize the risk of ignition and protect individuals working in these areas. The NEC outlines specific requirements for lighting fixtures used in different hazardous classifications including Class I (flammable gases or vapors), Class II (combustible dust), and Class III (flammable fibers). Each class of hazardous location presents unique challenges and risks, requiring specific safety measures and guidelines to prevent accidents and protect personnel. Proper classification and adherence to safety standards ensure that electrical equipment and lighting fixtures are suitable for use in these hazardous environments, reducing the potential for ignition and ensuring the safety of workers and facilities.Class I: These locations are where flammable gases or vapors could potentially be present in the atmosphere. Examples include petroleum refineries, chemical plants, fuel storage facilities, or areas where volatile substances are processed or stored. Due to the risk of explosion or fire, special precautions are necessary when installing electrical equipment and lighting fixtures in Class I locations.
Class II: These locations are characterized by the presence of combustible dust, which can ignite and cause explosions under certain conditions. Examples include facilities such as flour mills, grain elevators, pharmaceutical manufacturing plants, or any environment where fine particles can accumulate and become a hazard. Lighting fixtures used in Class II locations must be designed to prevent the ignition of combustible dust particles, reducing the risk of explosions.
Class III: These locations involve the presence of ignitable fibers or flyings, which can become airborne and pose a fire hazard. Examples include textile mills, woodworking facilities, or areas where materials such as cotton, wool, or wood particles are processed. Lighting fixtures in Class III locations must be selected and installed to minimize the risk of igniting these materials, ensuring a safe working environment.
Hazardous locations are subdivided into two divisions based on the probability of the presence of hazardous materials and the potential for ignition.
Division 1: These locations are where hazardous materials are likely to be present under normal operating conditions or where they may be present frequently or for extended periods. In Division 1 areas, there is a higher risk of encountering flammable gases, vapors, combustible dust, or ignitable fibers. Examples include areas near storage tanks, processing equipment, or production areas where hazardous materials are handled regularly. Lighting fixtures and electrical equipment installed in Division 1 locations must be designed to withstand the potential presence of hazardous materials and prevent ignition sources, ensuring safety during normal operations.
Division 2: These locations are where hazardous materials are not likely to be present in ignitable concentrations under normal operating conditions. They may still have occasional or intermittent exposure to hazardous materials, but the risk is lower compared to Division 1 areas. Examples include areas adjacent to Division 1 locations, where there may be occasional leaks, spills, or releases of hazardous materials, but they do not occur frequently or in large quantities. Lighting fixtures and electrical equipment in Division 2 locations must still meet safety standards to prevent ignition in the event of sporadic exposure to hazardous materials, ensuring safety during normal and abnormal operating conditions.
Hazardous locations are further categorized into specific groups based on the properties of the hazardous materials present. These group classifications help to identify and manage the risks associated with different types of flammable gases, vapors, and combustible dusts.
Groups A, B, C, and D (Class I Locations): Groups A, B, C, and D classifications are used in the context of Class I hazardous locations, which are environments where flammable gases and vapors may be present. These classifications help to categorize different types of flammable materials based on their ignition properties and potential hazards. Here's a breakdown:
Group A: This group includes acetylene, which is a highly flammable gas with specific ignition properties. Acetylene is particularly reactive and poses significant risks in terms of ignition and explosion. Facilities where acetylene is present must adhere to strict safety protocols to prevent accidents.
Group B: Comprising flammable gases such as hydrogen and butadiene, Group B materials are also highly reactive and pose significant risks of ignition and explosion. Industries handling these gases, such as chemical manufacturing plants or refineries, must implement stringent safety measures to mitigate these risks.
Group C: This group consists of flammable gases like ethylene and propane. While not as reactive as materials in Groups A and B, they still present significant fire and explosion hazards if not handled properly. Facilities where these gases are present must have appropriate safety protocols in place to minimize the risk of ignition.
Group D: Encompassing flammable vapors from substances such as gasoline, alcohol, and natural gas, Group D materials are commonly encountered in various industrial settings. These materials pose fire and explosion risks and require careful handling and storage to prevent accidents.
Groups E, F, and G (Class II Locations): Groups E, F, and G classifications are used in the context of Class II hazardous locations, where combustible dust is present. These classifications help to categorize different types of combustible dust based on their ignition properties, conductivity, and potential hazards. Here's a breakdown:
Group E: This group includes combustible metal dusts, such as aluminum or magnesium. These metal dusts have specific ignition properties and conductivity, making them prone to ignition under certain conditions. Industries working with metals must be aware of the risks associated with metal dusts and implement appropriate safety measures to prevent accidents.
Group F: Comprising combustible carbonaceous dusts, Group F materials include substances such as coal, carbon black, or charcoal dust. These dusts are derived from organic materials and pose fire and explosion hazards if dispersed in the air and ignited. Facilities handling these materials must have strict protocols in place to minimize the risk of ignition and ensure worker safety.
Group G: Encompassing combustible dusts not covered by Groups E and F, Group G materials include a wide range of substances such as wood, plastic, grain, or chemical dusts. These dusts vary in their composition and properties but share the potential for ignition and explosion if not properly managed. Industries handling these materials must conduct thorough risk assessments and implement appropriate safety measures to mitigate the risks associated with combustible dust.
ATEX/IECEx Zone system
The ATEX/IECEx Zone system is a classification system used to define and designate hazardous areas where the presence of potentially explosive atmospheres may occur. This system is internationally recognized and is commonly used in industries such as oil and gas, chemical processing, mining, and manufacturing.ATEX, which stands for "ATmosphères EXplosibles," is a comprehensive regulatory framework established by the European Union to ensure the safety of equipment, protective systems, and workers in potentially explosive atmospheres. ATEX encompasses two directives:
ATEX Directive 2014/34/EU: This directive sets out the requirements for equipment and protective systems intended for use in explosive atmospheres within the European Union. It mandates that such equipment must meet strict safety standards and undergo rigorous testing and certification processes to mitigate the risk of ignition and explosion.
ATEX Directive 1999/92/EC: This directive focuses on the obligations of employers to ensure the health and safety of workers who may be exposed to explosive atmospheres. It outlines measures to assess and manage risks, including the implementation of appropriate safety procedures, training, and the provision of suitable protective equipment.
The International Electrotechnical Commission Explosive (IECEx) System serves as a globally recognized certification scheme for equipment and services intended for use in explosive atmospheres. By providing a standardized framework for conformity assessment, the IECEx System enables manufacturers to demonstrate compliance with international standards, facilitating the international acceptance of their products. This system enhances safety by ensuring that equipment used in hazardous environments meets rigorous safety requirements, thereby reducing the risk of ignition and explosion. Overall, the IECEx System plays a crucial role in promoting the safety and reliability of equipment used in explosive atmospheres on a global scale.
The ATEX/IECEx Zone system classifies hazardous areas into zones based on the likelihood of the presence of explosive atmospheres and the frequency and duration of their occurrence. The system typically consists of three main zones:
- Zone 0: An area where explosive atmospheres consisting of flammable gases, vapors, or liquids are present continuously, frequently, or for long periods.
- Zone 1: An area where explosive atmospheres are likely to occur under normal operating conditions, but not continuously, and if they do occur, they are likely to persist for a short period.
- Zone 2: An area where explosive atmospheres are not likely to occur under normal operating conditions, and if they do occur, they are unlikely to persist for an extended period.
Equipment used in hazardous areas must be selected and certified according to the appropriate ATEX/IECEx Zone classification. This ensures that the equipment is designed and constructed to prevent ignition sources and minimize the risk of explosion in potentially explosive atmospheres.
LED lighting
LED technology revolutionizes hazardous location lighting by offering numerous advantages over traditional lighting technologies like incandescent, fluorescent, or HID (High-Intensity Discharge) lamps. LEDs are highly energy-efficient, converting a large portion of electrical energy into light. This efficiency reduces energy consumption and operating costs, which is crucial in industrial environments where lighting may be required continuously. LEDs have an exceptionally long lifespan compared to traditional lighting sources, lasting tens of thousands of hours. This extended lifespan reduces maintenance frequency and costs, as fixtures may not need to be replaced or serviced as frequently. LED fixtures are inherently rugged and durable, making them well-suited for harsh environments found in hazardous locations. They are resistant to shock, vibration, and temperature fluctuations, ensuring reliable operation even in challenging conditions. LEDs emit light in a specific direction, allowing for precise control and distribution of light. This directional lighting capability is advantageous for focusing illumination exactly where it's needed in hazardous areas, enhancing visibility and safety. LEDs reach full brightness instantly when powered on, eliminating the warm-up time required for some traditional lighting sources. This instant-on feature is crucial in emergency situations or environments where rapid response is necessary. LEDs can be easily dimmed and controlled, providing flexibility in adjusting light levels according to specific requirements or conditions. This capability allows for energy savings and customization of lighting solutions tailored to the needs of different areas within hazardous environments. LEDs are compact and lightweight, allowing for versatile installation options in confined or space-restricted areas common in industrial settings. Their small form factor makes them suitable for retrofitting existing fixtures or integrating into new designs.LED lights produce minimal heat compared to traditional lighting sources such as incandescent or HID lamps. This significantly lowers the risk of igniting flammable substances in hazardous environments, reducing the likelihood of fire or explosion. LED lights operate at much lower voltages compared to traditional lighting sources such as incandescent or HID lamps. This reduces the risk of electrical arcing, which can potentially ignite flammable gases, vapors, or dust present in hazardous environments. By operating at lower voltages, LED lights minimize the energy levels that could generate sparks, thereby decreasing the likelihood of fire or explosion. LED lights produce light through a semiconductor process that does not rely on heating a filament or generating an electric arc. As a result, LED lights do not emit sparks during operation, making them inherently safer in environments where explosive atmospheres may be present. This eliminates one of the primary ignition sources associated with traditional lighting technologies, further reducing the risk of fire or explosion. The absence of high-voltage components and spark-producing elements in LED lights significantly lowers the risk of ignition in hazardous locations. LED lights are designed to operate without generating excessive heat or electrical discharge, minimizing the potential for igniting flammable substances in the surrounding atmosphere. This enhances safety by reducing the probability of accidental fires or explosions caused by lighting fixtures. LED lights can be engineered with intrinsically safe designs that prevent the release of sufficient energy to ignite flammable gases or dust. By incorporating features such as current-limiting circuits and encapsulated components, LED lights can achieve intrinsically safe certification, ensuring their safe operation in hazardous environments without the need for additional protective measures.
Design and construction
Hazardous location lighting fixtures are constructed with materials and designs that prevent sparks or hot surfaces from igniting flammable substances in the surrounding environment. This may include heavy-duty housings, sturdy enclosures, and specialized seals to contain any potential explosion within the fixture. The electrical components within hazardous location lighting fixtures are often sealed to prevent flammable substances from coming into contact with them. This prevents sparks or electrical arcs from causing ignition. In environments where corrosive substances are present, hazardous location lighting fixtures are made from materials that resist corrosion. This ensures the longevity and safety of the fixtures in these harsh conditions. Hazardous location LED lights are designed with specific features to address the risk of igniting flammable materials in volatile environments. One crucial aspect is temperature control, as excessive heat from lighting fixtures could potentially trigger ignition. To mitigate this risk, these LED lights may incorporate various mechanisms aimed at managing and dissipating heat effectively. One approach is the integration of thermal management mechanisms, which can include heat sinks or fins designed to absorb and disperse heat away from the fixture. By efficiently dissipating heat, these mechanisms help to maintain the temperature of the LED light within safe limits, reducing the risk of igniting flammable materials nearby. Before being used in hazardous locations, lighting fixtures must undergo rigorous testing and certification to ensure they meet safety standards set by organizations such as UL or CSA. This certification ensures that the fixtures are designed and built to safely operate in hazardous environments.The incorporation of a flame path into explosion-proof LED lights is a critical safety measure that contributes to the overall risk reduction strategy in hazardous environments. It helps to minimize the likelihood of ignition and the potential consequences of an explosion, ensuring the safety of workers and the integrity of facilities where flammable gases, vapors, combustible dust, or ignitable fibers are present. The flame path serves as a pathway or channel within the lighting fixture that is specifically designed to contain and redirect any potential explosion or ignition event that may occur within the fixture itself. By confining the explosion to this controlled pathway, the risk of ignition of surrounding flammable materials is minimized. This helps prevent the spread of fire or explosion to the broader hazardous environment. In the event of an explosion inside the fixture, the flame path directs the force, heat, and gases away from the surrounding area. By containing and channeling the explosion's energy, the flame path helps to mitigate its impact, reducing the risk of damage to equipment, structures, and, most importantly, personnel in the vicinity.