Table of Contents Hide
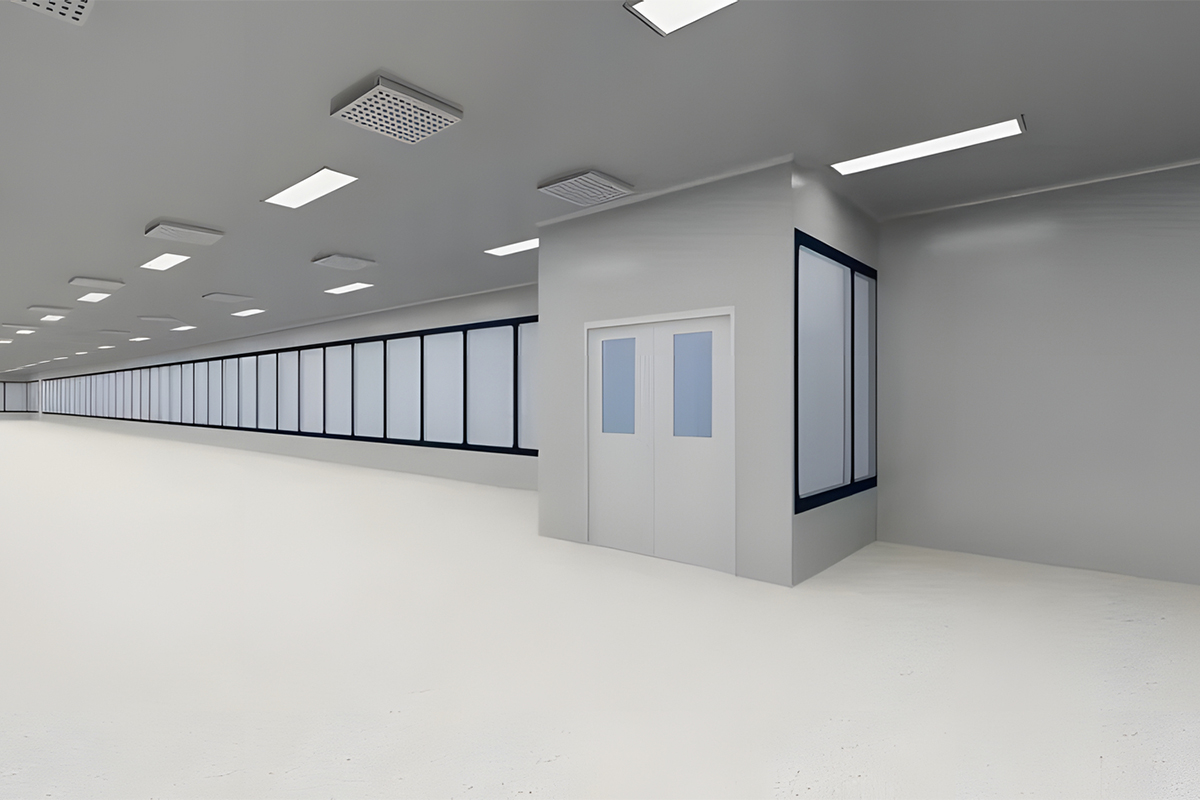
Cleanroom lighting
Cleanroom lights are designed to operate effectively within the strict cleanliness standards of cleanroom environments, ensuring that they do not compromise the integrity of the controlled environment or the products being manufactured within it. Cleanrooms are environments where the level of airborne particles, such as dust, microbes, and aerosol particles, is carefully controlled to specific limits. These environments are commonly found in industries like pharmaceuticals, electronics manufacturing, biotechnology, and healthcare, where maintaining cleanliness is crucial to ensure product quality and safety. Cleanroom lighting fixtures are engineered with precision and quality to meet the stringent requirements of such environments. They must not only provide adequate illumination but also be designed to minimize the introduction of contaminants into the cleanroom space. This might involve features such as sealed enclosures, smooth surfaces that are easy to clean, low particulate emissions, and compatibility with cleanroom protocols for installation and maintenance.Integral part of cleanroom environments
Cleanroom lighting serves several critical applications within cleanroom environments, where stringent cleanliness standards are essential. Cleanroom lighting provides adequate illumination for personnel to perform tasks accurately and safely. Tasks in cleanrooms can range from intricate assembly work in semiconductor manufacturing to delicate procedures in pharmaceutical production. Proper lighting ensures that workers can see clearly and perform their tasks with precision. Cleanrooms often house sensitive equipment and products that require thorough inspection and quality control measures. Effective lighting is crucial for visual inspections to identify defects, contaminants, or anomalies in products, components, or processes. Proper lighting conditions help ensure that quality standards are met and that defective items are promptly identified and addressed. Cleanroom environments may contain potentially hazardous materials, equipment, or processes. Adequate lighting is essential for maintaining a safe working environment and preventing accidents. Properly illuminated pathways, emergency exits, warning signs, and equipment indicators help reduce the risk of accidents and injuries. Cleanrooms may incorporate monitoring and surveillance systems to continuously monitor environmental parameters such as temperature, humidity, and particle levels. Lighting is necessary for clear visibility of monitoring displays, control panels, and surveillance cameras, enabling personnel to monitor cleanroom conditions effectively. Cleanroom lighting fixtures are designed to minimize particle generation and accumulation, helping to maintain the cleanliness of the environment. Sealed housings, smooth surfaces, and materials resistant to corrosion and degradation are characteristics of cleanroom lighting fixtures that contribute to contamination control efforts.Cleanroom classifications
Cleanrooms are classified into different types based on the level of cleanliness required for the specific processes carried out within them. The classification of cleanrooms is primarily determined by the number of particles of a specific size per cubic meter of air. The classification system is typically based on the number and size of particles allowed per cubic meter of air, as well as other factors like airflow velocity, room pressurization, temperature, and humidity control. These factors are crucial because even tiny particles can adversely affect sensitive processes and products. For example, in industries where precision is critical, such as semiconductor manufacturing, even a small particle of dust can cause defects in the final product. Therefore, cleanrooms in such industries may require stringent controls to maintain extremely low levels of particulate contamination. Cleanroom classifications are usually standardized and governed by international standards organizations like the International Organization for Standardization (ISO) or national standards bodies like the United States Federal Standard 209E (FS 209E), although FS 209E has been replaced by ISO 14644 in many countries.Cleanrooms are often classified according to the ISO (International Organization for Standardization) standard 14644-1. This standard specifies the maximum allowable number of particles per cubic meter of air for different cleanliness classes. The classification system typically ranges from ISO Class 1 (the cleanest) to ISO Class 9 (the least clean), with each class specifying the allowable limits of airborne particles. Cleanrooms of higher classifications, such as ISO Class 1 or ISO Class 3, have stricter requirements and are used for processes that demand extremely low levels of contamination, while lower-class cleanrooms may be suitable for less critical processes. The US Federal Standard 209E classification system was commonly used before the ISO standards became more widely adopted. It also specifies the maximum allowable number of particles per cubic foot of air for different cleanliness classes. In pharmaceutical manufacturing, cleanrooms are often classified according to EU GMP guidelines. These guidelines define various cleanliness grades, ranging from A to D, with Grade A representing the highest level of cleanliness required for critical processes, such as sterile product manufacturing. Certain industries, such as semiconductor manufacturing or biotechnology, may have their own specific cleanroom classification standards tailored to the unique requirements of their processes.
Forms and configurations of cleanrooms
Cleanrooms come in various forms and configurations, each tailored to specific industry requirements, cleanliness standards, and operational needs. Hardwall cleanrooms are constructed using rigid materials such as metal or rigid plastic panels for walls and ceilings. These cleanrooms offer a permanent and durable structure with a high degree of customization. Hardwall cleanrooms are often used in industries like semiconductor manufacturing, aerospace, and pharmaceuticals where long-term stability and precise control over environmental conditions are essential. Softwall cleanrooms are constructed using flexible materials such as vinyl curtains or plastic sheets for walls and ceilings. These cleanrooms provide a more flexible and cost-effective solution compared to hardwall cleanrooms. Softwall cleanrooms are frequently used in industries like electronics assembly, biotechnology, and research laboratories where temporary or mobile cleanroom facilities are needed or where frequent reconfiguration is required. Modular cleanrooms are prefabricated cleanroom systems that can be easily assembled, disassembled, and reconfigured to accommodate changing needs. These cleanrooms typically consist of pre-engineered panels, frames, and components that can be quickly installed in existing facilities or as standalone structures. Modular cleanrooms offer flexibility, scalability, and rapid deployment, making them suitable for industries with dynamic production requirements or limited space. Portable cleanrooms are compact, self-contained cleanroom units that can be transported and deployed as needed. These cleanrooms are often equipped with built-in HVAC systems, filtration units, and lighting fixtures to provide a controlled environment for specific applications. Portable cleanrooms are commonly used in industries like healthcare, pharmaceuticals, and biotechnology for mobile testing, cleanroom training, or emergency response purposes. Mini-environment cleanrooms are localized cleanroom enclosures designed to provide ultra-clean environments within larger cleanroom spaces or non-cleanroom areas. These cleanrooms use high-efficiency particulate air (HEPA) or ultra-low particulate air (ULPA) filtration systems to create controlled environments for critical processes or equipment. Mini-environment cleanrooms are commonly employed in industries like semiconductor manufacturing, nanotechnology, and optics fabrication.Cleanroom lighting applications
Cleanroom lights find applications across a wide range of industries where maintaining a controlled environment with low levels of airborne particles, dust, microbes, and other contaminants is critical.In semiconductor fabrication, even tiny particles can cause defects in microchips, leading to costly production losses. Cleanrooms are essential for manufacturing semiconductor wafers, where precise control over environmental conditions is required to ensure high product yields and quality. Cleanroom lighting in semiconductor manufacturing facilities helps maintain stringent cleanliness standards to prevent contamination of delicate electronic components during production processes.
Cleanrooms are vital in pharmaceutical manufacturing for producing sterile drugs, vaccines, and other medical products. Maintaining a sterile environment is crucial to prevent contamination and ensure product safety and efficacy. Cleanrooms are used for processes such as aseptic filling, compounding, and packaging of pharmaceutical products. In pharmaceutical facilities, cleanroom lighting is essential to ensure the sterility of the production environment, preventing any contaminants from compromising the quality of medications.
Cleanrooms play a crucial role in biotechnology research, genetic engineering, and biopharmaceutical production. These environments are used for cell culture, DNA sequencing, protein purification, and other sensitive biotechnological processes where maintaining sterility and controlling contamination are essential. Cleanroom lighting helps maintain a controlled environment free from contaminants that could affect sensitive experiments and research.
Cleanrooms are employed in the production of medical devices such as implants, surgical instruments, and diagnostic equipment. These environments ensure that medical devices are manufactured under controlled conditions to meet regulatory standards for safety, sterility, and quality. Cleanroom lighting is necessary to maintain cleanliness and precision during the manufacturing of medical devices to ensure their safety and efficacy for patient use.
Cleanrooms are increasingly used in food and beverage processing facilities to maintain hygiene and prevent contamination. Cleanrooms help control airborne particles, microorganisms, and allergens, ensuring the safety and quality of food products during processing, packaging, and storage. In food and beverage processing facilities, cleanroom lighting helps ensure hygienic conditions and prevents contamination of products during manufacturing processes.
Cleanrooms are essential in various research fields, including nanotechnology, materials science, and microelectronics research. Researchers use cleanrooms to conduct experiments and fabricate devices at the nanoscale level, where contamination control is critical for obtaining reliable results. Cleanroom lighting is crucial in research laboratories where experiments require a controlled environment free from contaminants to ensure accurate and reliable results.
Cleanrooms are utilized in hospitals and healthcare facilities for sterile compounding of medications, preparation of intravenous solutions, and surgical procedures requiring aseptic conditions. Cleanrooms in healthcare settings help prevent healthcare-associated infections and ensure patient safety. Cleanroom lighting is important in healthcare facilities to maintain sterile conditions in operating rooms, isolation wards, and other areas where cleanliness is essential for patient safety and infection control.
Cleanrooms are utilized in the manufacturing of optical components, precision instruments, and aerospace components where even minor contaminants can affect performance. Cleanroom environments provide the necessary cleanliness levels for fabricating lenses, mirrors, semiconductors, and other precision-engineered products. Cleanroom lighting is essential in these industries to minimize dust and other particles that could impair the functionality of optical devices and precision instruments.