Table of Contents Hide
- 1 What Is an LED Flood Light
-
2
Applications
- 2.1 Area lighting
- 2.2 Sports lighting
- 2.3 Landscape lighting
- 2.4 Facade and structure lighting
- 2.5 Security lighting
- 2.6 Industrial outdoor lighting
- 2.7 Mobile light towers
- 2.8 Billboard lighting
- 3 Lighting Technology
- 4 Light Distribution
- 5 Luminaire Construction
- 6 Light Source
- 7 Optical System
- 8 Thermal Management
- 9 LED Driver
- 10 Lighting Control
- 11 System Protection against Environmental Factors
- 12 Mounting and Aiming
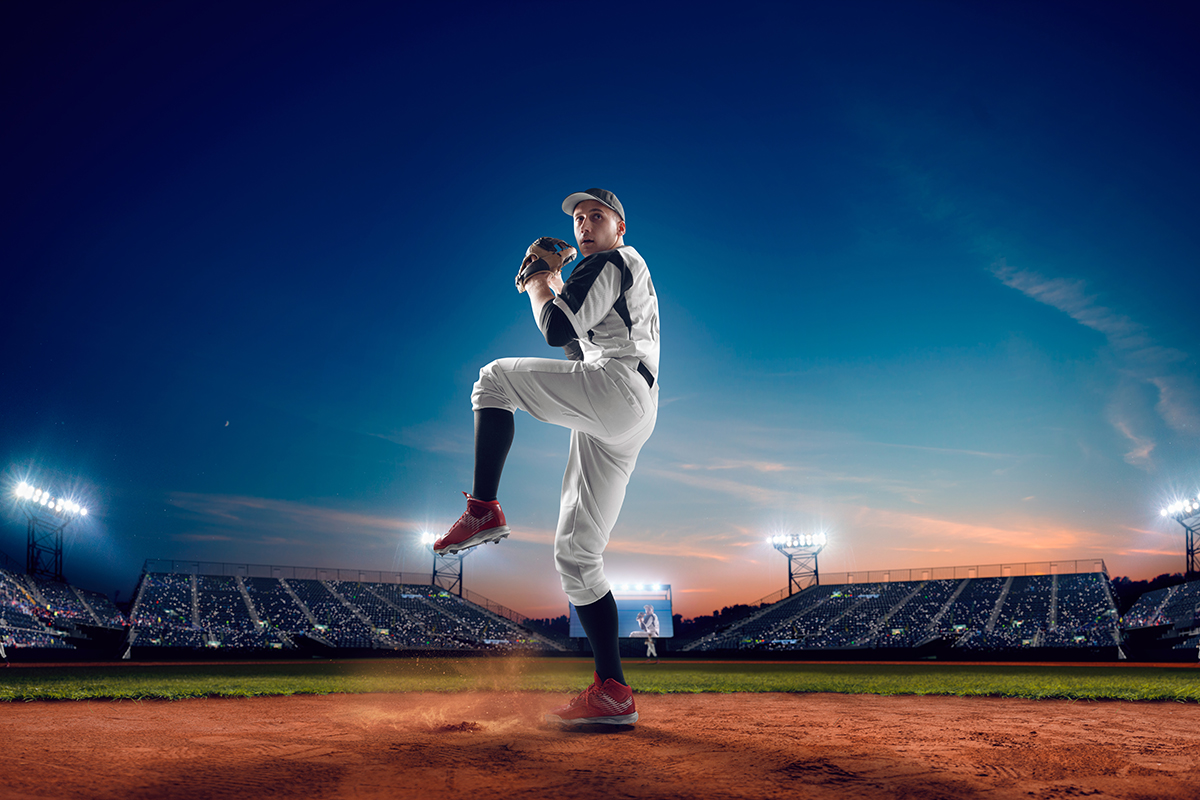
What Is an LED Flood Light
LED flood lights are aimable, directional LED luminaires that project a beam of light onto a specific area, surface, or object. Floodlighting is a basic element of both interior and exterior lighting. However, in the lighting industry "floodlighting luminaires" or "floodlights" generally refer to weatherproof outdoor luminaires that provide area lighting, ambient lighting, accent lighting, or task lighting for a variety of applications. Indeed, floodlights are a very ambiguous category of products. These outdoor luminaires are not meant to only project a wide spread of light, floodlights also include luminaires that produce a narrow beam of light for spotlighting or long throw lighting. As such, a floodlight can be defined as an outdoor directional light that is designed to provide controlled illumination of the desired range.Applications
Floodlights are the all-rounder of outdoor lighting. Except for roadway and street lighting which needs beam patterns tailored to road designs, floodlights can be a qualified candidate for virtually all outdoor applications that require directional illumination over a defined zone. With a wide selection of beam patterns and lumen packages, plus their optical aiming capability and mounting flexibility, floodlights provide a solution that allows photometric performance to be refined through a "trial and adjustment" process. They can be used to extend the daytime functionalities of exterior spaces and outdoor facilities into the night, or to accent and highlight architectural and landscape elements thereby transforming the dark exterior into an inspired nightscape.Area lighting
Floodlights can be used as area lighting luminaires to illuminate large geometric areas such as roadway interchanges, parking lots, car dealerships, airport aprons, recreational facilities, parks, storage yards, freight terminals, and toll plazas. While floodlights may not be ideally suited to pedestrian- and urban-scale lighting because of potential spill light and glare control problems, these luminaires has been used as a workhorse in high mast lighting systems. High mast lighting systems are generally installed at sites that are not bounded by light-sensitive areas such as residential complexes, hotels and hospitals. Floodlights are capable of being aimed at any direction from the high mast headframe to ensure that the most intense potions of the beam can be directed accurately to where it needs. High mast systems are often required to be placed at the perimeter of or some distance away from the target area for minimal interference or conflicts with the area. The lumen packages and light distribution patterns of floodlights can be designed to coordinate with the location of the high mast system.Sports lighting
Sports lighting systems use floodlights to deliver uniform lighting for stadiums, arenas, athletic fields, and play fields or outdoor facilities that run sports such as archery, baseball, bicycle racing, golf, motor racing, horse racing, football, soccer, tennis, skating, and cricket. Since there's usually no structures to mount overhead light fixtures and no surface to redirect the light bounced from the playing area, the only type of luminaires that can be used for outdoor sports lighting is the direct distribution floodlights. Sports lighting should be specially designed with proper illuminance values, uniformity ratios, light distributions, mounting heights, orientations, and locations. Floodlighting is generally provided from multiple directions to create good visibility of the playing target and modeling of the players while minimizing shadows and obtrusive light.Landscape lighting
Floodlighting luminaires are indispensable in creating drama, beauty, depth, dimension, texture, space, and focal points in a landscape scene. These luminaires can be used to accent hardscape features such as monuments, sculptures, fountains, or other architectural elements that are designed to be part of the landscape scheme. Softscape lighting for trees, shrubs, and other plants that landscape a building or an area is for the most part accomplished with floodlights through wash lighting, uplighting, moonlighting, spotting, silhouetting and shadowing. A wide choice of light distributions and a rejuvenating combination of lighting techniques offer almost infinite possibilities of lighting effects.Facade and structure lighting
The architectural features of a building or structure are the crucial design element that can be accentuated to deliver prestige, symbolism and recognition. Architectural floodlighting luminaires can be used to provide wall washing to bathe a whole wall in uniform light, wall grazing to bring out the textured beauty of a vertical surface, and accent lighting to create areas of visual drama and differentiation. Floodlights can be used to enhance the intrinsic charm and create a breath-taking impression of three-dimensionality for architecture such as buildings, bridges, and recreational facilities.Security lighting
Floodlights is often installed at the perimeters of residential, commercial, industrial, and institutional buildings or facilities to provide security lighting. Lighting can be a deterrent to criminal acts and create a perception of reasonably secure environment. The perimeter illumination from wide beam floodlights can enhance observation, frighten away intruders, and facilitate the proper use of other security devices such as surveillance cameras and video doorbells.Industrial outdoor lighting
Area and task lighting for industrial parks and outdoor manufacturing facilities such as petroleum refineries, chemical plants, drilling rigs, oil depots, sewage treatment plants, and open pit mines is often supported with floodlighting. Because high humidity, flammable vapors, corrosive atmosphere and hazardous materials are likely to be present in these areas, industrial floodlights may be engineered to stand up to these demanding conditions and certified for use in hazardous locations classified according to IEC or NEC/CEC standards.Mobile light towers
A mobile light tower is a trailer-mounted area lighting system geared for construction, jobsites, roadwork, disaster response, outdoor events, and other temporary public lighting. An array of floodlighting luminaires are mounted on the headframe of a retractable mast that deploys quickly and easily with a manual or electric winch.Billboard lighting
Floodlights are used to spread light across a billboard, from edge to edge and corner to corner, allowing the advertisement and storefront design to impress passersby through the night all year round.Lighting Technology
In the past, high intensity discharge (HID) lamps, specifically high pressure sodium (HPS) and metal halide (MH) lamps had been the dominant light sources for floodlighting luminaires. However, the use of these gaseous discharge bulbs involves many trade-offs. HPS can reach a relatively high source efficacy (70 - 140 lm/W) but the light produced by this technology can significantly distort human color perception. Therefore HPS lamps have very limited application scenarios. HPS floodlights are typically used in area lighting applications where color perception has minimal influence on the intended use. As opposed to the typical CRI (color rendering index) of 22 with HPS lighting, MH lamps have a tolerable color performance (CRI 65 typical) for color critical applications such as sports lighting. Nevertheless, aside from their intrinsically high fire hazards, noise pollution and UV radiation, MH lamps have a poor energy efficiency and short lifespan that significantly undermine the return on investment (ROI) of this technology.The history of artificial lighting has been one of constant evolutions punctuated by a series of crucial innovations. The most recent innovation in lighting is semiconductor-based light emitting diode (LED) technology. LEDs overcome many of the disadvantages of HID lighting and allow floodlighting luminaires to deliver an extraordinary ROI. Currently available LEDs have a typical source efficacy approaching 200 lm/W. The directional nature of LEDs allows up to 95% of the light emitted by the LEDs to be extracted out of the luminaire, whereas HID floodlights have a much lower system efficacy (70 - 85 %). High energy conversion and optical efficiencies translate to an extremely low operational cost and short payback period. The long life cycle of a properly engineered system and minimal maintenance requirement over the life of the product further drive down the total cost of ownership. The energy savings of LED flood lights can be even more maximized when the luminaire is operated by sensors or controls which can react to the environmental and occupancy changes or interact with other equipment and devices.
The benefits of LED floodlighting extend far beyond long lifespan, high energy and maintenance savings. LED technology contributes to a significant improvement in quality of illumination for floodlighting applications. LEDs emit in a directional Lambertian spatial intensity distribution describable as essentially a beam of forward-directed light. This allows high efficiency optical control with custom optics designed for specific types of discrete LEDs or arrays to enable high uniformity light distribution. Uniform distribution of light over a surface or area is of critical importance in lighting design. In HID systems, the majority of the illuminance lands directly below the luminaire creating a hot spot with excessive luminance. The poor uniformity ratio (6:1 typical) of HID floodlights can result in significantly different luminance levels between the neighboring lighting installations and thus requires a high density of lighting installations to compensate for the poor illuminance uniformity. LED flood lights can be designed to illuminate with a uniformity ratio of less than 3:1, which allows a smooth spread of light to be cast over a surface or area. Uniform illumination avoids the distortion of visual perception, reduces the frequency of eye adaptation between different vision states, and allows consistent rendering of scenes or objects within a lighting zone. High illuminance uniformity also makes it possible to maximize fixture spacing for drastically reduced equipment and installation costs.
The compelling edges of LED floodlighting also include its exceptional spectral performance. The most economical LEDs available on the market offer a CRI in the 70 - 80 range, which is a significant improvement over HID light sources. This level of color quality is sufficiently good to address the absolute majority of color rendering requirements in outdoor lighting applications. The spectral composition of LEDs can be formulated to deliver superior color rendition with a CRI above 90 such as to satisfy the most color discriminating requirement. Another impressive spectral quality of LEDs is the scotopic/photopic (S/P) ratio, which is used to evaluate the effectiveness (for visual performance) of light sources as light level decreases. As opposed to the low S/P ratio (0.65) of HPS lamps, LED flood lights offer an S/P ratio as high as 2.0 or above. Illumination with a high S/P ratio results in improved peripheral visual performance in the mesopic vision state which falls between the scotopic and photopic ranges. Average light levels in outdoor area lighting that is designed to accommodate vehicular traffic are usually in the mesopic range. Excellent mesopic vision is important to ensure driver visibility and reduce collision rates.
LED floodlighting does not have to cope with the start-up and hot restrike issues that HID lighting faces. HID floodlights require the filament to warm up before the maximum amount of lumen output can be achieved. The warm-up period can last up to ten minutes. Hot restrike of HID systems is of greater concern than initial start-up. The hot restrike process that requires a cooling down/warming up cycle can take up to twenty minutes. Long restrike times can cause chaos and panics in large-scale outdoor events. Instant on/off operation of LED luminaires eliminates the hot restrike concern with HID lighting and thus contributes to a high level of security in the case of an emergency.
In contrast to HID's restrictive dimming capabilities, LEDs allow their light output to be adjusted to any desired level when equipped with a compatible driver that can perform dimming control. The ability to react instantaneously to changes in power input allows LED flood lights to be controlled in a very dynamic way. This opens up an entire suite of lighting control strategies for energy saving and dynamic lighting purposes. In particular, the dynamic aspect of LED lighting enables an infinite variety and combination of dynamic effects to be created with LED floodlighting in architectural and landscape lighting applications.

Light Distribution
The light distribution of a floodlight is typically described in degrees of beam spread and uses the NEMA beam types as a reference. The NEMA luminaire classification system is based on the distribution of flux within the beam produced by the luminaire. Seven distributions, type 1 through 7, are defined in this system. Tighter beams have low beam type numbers and the wider beams have higher numbers. The beam spread of floodlights is classified according to the luminaire's field angle degrees. The field angle refers to the angle between two directions for which the intensity is 10% of the maximum.- Beam type 1: 10° to 18° (Very Narrow)
- Beam type 2: > 18° to 29° (Narrow)
- Beam type 3: > 29° to 46° (Medium Narrow)
- Beam type 4: > 46° to 70° (Medium)
- Beam type 5: > 70° to 100° (Medium Wide)
- Beam type 6: > 100° to 130° (Wide)
- Beam type 7: > 130° and up (Very Wide)
Floodlights are available in asymmetrical and symmetrical distributions. Axially symmetrical luminaires have the same horizontal and vertical beam spread and are classified with one NEMA number (i.e., Type 3). Asymmetrical luminaires have separate horizontal and vertical beam designations with the horizontal value always given first (i.e., Type 5 x 3 or Type 5H x 3V). Below are six standard NEMA beamspreads.
Luminaire Construction
LED flood lights generally fall into two categories based on their configurations: integrated and modular.The integrated type LED flood lights are similar to their HID predecessors which are designed in a self-contained system. This type of LED luminaires is designed to accommodate a light engine with a system wattage typically under 300 watts. The electrical system is co-located with the LED assembly in a sealed die cast aluminum housing. Earlier generations of LED flood lights replicate the form factor of HID systems and usually have a bulky volume and a clumsy look. Modern LED flood lights of the integrated type tend to have an organic design and sleek form. A perfect integration of all elements into the structure ensures these visually engaging luminaires deliver a tremendous aesthetic value essential to enhancing architectural settings and landscape designs.
Modular floodlighting systems offer a significant amount of options and customizations with a scalable architecture. The basic building block of these LED fixtures is the modular LED engine which includes all the elements of an LED system except for the power supply. The modular architecture allows a variable number of light engines to be installed on a bracket or secured on a frame to provide the lumen package and light distribution needed to meet the design specifications. The LED drivers and other electrical components are usually attached to the backside of the fixture. The waterproof drivers are either exposed in the open air or enclosed in a sealed PSU for an added level of protection. Modular design offers the benefits of lumen package scalability, adjustable beam direction for each module, and convenient servicing and replacement. These floodlights are typically used as high power lighting systems that may consume as much as 1200 watts of electrical power and produce a substantial volume of lumens needed for large-scale architectural lighting, large area high mast lighting, and sports lighting applications.
LED flood lights are constructed with a rugged aluminum housing which allow the luminaire to safely operate in the most demanding installations while providing conductive and convection cooling for the LEDs. Aluminum housings of LED floodlights are generally made through die casting which can create geometrically complex products with closer tolerances and higher dimensional stability than many other mass production processes. The chassis (frames or brackets) of modular floodlighting systems are also typically made of die cast aluminum to ensure the structural strength while maintaining a sleek look. Aluminum heat sinks of modular LED engines are often extruded for enhanced thermal performance. Aluminum construction results in high mechanical strength, good thermal conductivity, high corrosion resistance, and excellent surface finishability of the luminaire enclosure. Floodlighting luminaires should be designed to offer a reduced effective projected area (EPA) to minimize wind load requirements.
The light engine is an integrated assembly of discrete LED packages or high power LED arrays. The discrete LED packages are solder mounted onto a metal core printed circuit board (MCPCB). High power LED arrays are either mounted on an MCPCB or integrated into a ceramic substrate. The LEDs may be fitted with integrated secondary optics for individual optical control or simply exposed with their luminous flux regulated by the luminaire reflector which sits over the entire LED assembly. In addition to optical control, such a reflector serves to complete the aesthetics of the floodlight. The LED assembly is mechanically secured and thermally interfaced to the heat sinking surface of the aluminum housing. A thermal interface material (TIM) is oftentimes placed between the heat sink and LED board to facilitate heat transfer between two mating surfaces. A tempered glass lens is held in place with a die cast aluminum lens frame via stainless steel recessed captive screws to protect LEDs and allow for cleaning/debris removal. The snap-in type opening and closing mechanism is also used in some models to provide ease of installation and maintenance.
Light Source
LED chips are bare LED dies that must be enclosed in packages before they can be used as light sources. LED packaging is designed to provide thermal conduction, electrical connection, mechanical support, and environmental protection for semiconductor diode. While LEDs that emit a monochromatic color such as red, green, or blue are often incorporated into LED flood lights to produces an enhanced spectrum of precisely controllable light for landscape or architectural lighting, the large majority of LED flood lights are designed to produce white light. In phosphor converted white LEDs, the package into which the LED chip is assembled should also provide wavelength conversion (partial conversion of short wavelength blue light) and color mixing (mixing blue light with the down-converted light to produce the desired white light).There are a multitude of options regarding the package design and packaging materials. Ultimately the optical, thermal, and electrical performances of LED packages of different designs and LED packages from different manufacturers can vary tremendously. Nevertheless, the cost of LED packages can oftentimes outweigh the performance and ROI of the light source. This is made evident with the flooding of mid-power LEDs in the outdoor lighting market. Mid-power LEDs, or more commonly known as SMD LEDs, are plastic leaded chip carrier (PLCC) packages that offers a very competitive cost and a high luminous efficacy. Unfortunately, their advantages are vulnerable in outdoor environments and high power LED systems. The high efficacy and low packaging cost of mid-power LEDs are achieved through the use of plastic material and lead frame with high light reflectivity. The initial source efficacy of these LEDs looks very attractive. However, under high operating temperatures mid-power LED exhibit rapid lumen depreciation and color shift. Thermal degradation is not the only failure point of these plastic packages. Mid-power LEDs are hard to survive high drive current operation and environments with corrosive gases or prone to vibration and demanding loads due their poor wire bonding reliability and high corrosion susceptibility of the leadframe plating.
High power LEDs deliver excellent lumen maintenance and high package reliability that justify their high packaging cost. The fundamental packaging philosophy of high power LED packages is to provide a robust platform that can survive high thermal, electrical and environmental stresses. The elimination of thermally unstable plastic housings, corrosion-prone leadframes, and fracture-prone wire bonding allows high power LEDs to thrive in high temperature conditions and hostile environments. A ceramic substrate with metallized with copper layers and thermal vias enables high volume heat transfer from the semiconductor junction to the ambient air via the system thermal path. High power LEDs can be driven at current of more than an ampere and pump out thousands of lumens over a lifespan significantly longer than mid-power LEDs.
Chip-on-board (COB) LEDs are multi-chip LED packages in which a high density array of diodes are die bonded onto an MCPCB or a ceramic substrate. These high power packages can reduce the number of discrete components in the system. COB LEDs can be mounted to a heat sink directly or via a COB connector, which further simplifies system design. COB LED flood lights are preferred for accent lighting applications where the luminaire must provide a directional beam of uniformly distributed light. Removal of the intermediate substrate allows the LED chips to dissipate heat efficiently through the circuit board or ceramic substrate. However, the electrical path to the individual LED chips in COB packages is created using wire bonding. This makes COB LEDs less resistant to electrical overstress (EOS) as compared to high power LEDs.
The chip scale package (CSP) technology strips superfluous elements to drive down cost, scale down the size, and improve reliability and performance of LEDs. The package-free design uses the flip-chip structure while eliminating the submount that comes with flip-chip packages. With thermal and electrical robustness comparable to high power LEDs as well as packaging costs lower than traditional mid-power LEDs, CSP LEDs are deemed to dominate the market as the technology matures.
Optical System
Secondary optics that shape the radiation pattern of LEDs in floodlighting systems can be categorized into lenses, reflectors, and combinations of them. Reflectors made of either aluminum or coated plastics regulate luminous flux from the LEDs through specular reflection, semi-specular reflection, or diffuse reflection. To produce wide beams, a large reflector that encloses the entire LED array is usually used. However, a system-wide reflector isn't suited to optical assemblies with a large light emitting surface (LES) because a substantial part of the emitted light from an array of discrete LEDs exit the reflector aperture without hitting the reflector surface. LED flood lights are in trend of emitting from a large LES so as to achieve an excellent uniformity ratio. In these products, a reflector matrix consisting of discrete precision-molded reflectors is used to control the light distribution of each individual LED or a small array of LEDs. System-wide reflectors for LED flood lights typically have square or rectangular exit apertures for the purpose of matching the luminaire form factor. The exit apertures of reflector matrices can be round or square depending on the light distributions requirements. Reflector matrices can be used to produce narrow beams as well. In some applications additional lenses, such as convex, collimator or micro-prismatic lenses, are incorporated into the individually molded reflector cavities to improve light extraction efficiency or maximize visual comfort.Compound lenses that combine an array of lens elements with a common axis have gained favor over optical reflectors in high power LED floodlighting systems or applications where beam control is critical. Total internal reflection (TIR) optics capitalize on characteristics unique to LEDs and are capable of providing accurate beam control and uniform light distribution with optical efficiencies as high as 93%. The TIR lens, which consist of a refractive lens and a reflector, combines the best optical characteristics of both a reflector and a lens. The refractive lens that nestles inside the reflector guides virtually every ray of light emitted by the LED and direct the rays to the reflector, which sends them out in a precisely controlled beam. The TIR lens assembly, injection molded in a one-piece design, is indexed to the circuit board to ensure consistent optical alignment for the array of discrete LEDs.
TIR optics are made from polymethylmethacrylate (PMMA or acrylic) or polycarbonate (PC). Acrylic is currently the most favored choice because of its low manufacturing cost, high transmissivity, excellent diffusion of LED hot spots, and high UV stability. However, long-term heat exposure can accelerate the aging process and cause deformations. Polycarbonate, which offers superior thermal stability, ignition resistance and optical performance, is a leading material choice for lens applications requiring close contact to the LED source. What impedes its widespread application in the LED industry is obviously the cost factor.
Thermal Management
Temperature is the single most important failure accelerator in LED flood lights. As a byproduct of converting electrical power into light in the courses of erlectroluminescence and photoluminescence, a substantial amount of heat is generated at the LED junction and the phosphor layer. LEDs convert between 40 to 60% of the power they are fed into light, which means between 60 to 40% of the power is thrown away as waste heat. Since LEDs do not radiate heat in the form of infrared waves the way like HID light sources, all the heat generated dwells on the semiconductor devices. Thermal buildup within the LED can lead to phosphor thermal quenching (drop in phosphor efficiency), degradation of encapsulant and plastic resin, and accelerated nucleation and dislocation growth in the semiconductor dies. These failure mechanisms usually result in fast degradation in light output and premature failure.Thermal management of an LED system is a multidimensional engineering work which involves light source selection, drive current control, and heat transfer from the LED junction to the ambient air. As mentioned previously, the packaging design and materials of LEDs are one of the key thermal design factors. Ceramic-based high power LEDs can operate efficiently at a high junction temperature such as 125 ° C without the risk of irreversible degradation. On the other side, the plastic-based mid-power LEDs are short-lived when they're operated at a junction temperature above 100 ° C. Therefore, mid-power LEDs are more discriminating about thermal management and drive current than high power LEDs. In thermal engineering of LED systems using mid-power LEDs, special considerations should be given to the performance and reliability of solder joints. Unlike high power LEDs that have high operating temperature capable interconnects, thermal cycling, overdriving and environmental stresses can ruthlessly undermine the reliability of solder joints and thus damage the integrity of the thermal path.
LED flood lights typically rely on passive cooling as the air circulation and ambient temperature in outdoor environments are adequate to drive convective heat transfer. Aside from the use of high performing TIMs and MCPCBs which is designed to ensure the lowest possible thermal resistance along the thermal path, the most important thermal management component is the heat sink. Crappy products are usually equipped with lightweight heat sinks, in addition to cheap mid-power LEDs and bare-bones driver circuits. A heat sink serves to pull heat away the LEDs through thermal conduction and then to convect that thermal energy into the surrounding ambient air. The heat sink should provide adequate thermal interface area to spread heat, sufficient thermal capacity to absorb the heat, and enough surface area to facilitate high efficiency thermal convection. The latent heat capacity (thermal absorption capacity) of a heat sink depends on the thermal conductivity of the material that the heat sink is made from and the physical volume of the heat sink. Aluminum is chosen as the most commonly used heat sink material in LED systems not only for its reasonably good thermal conductivity, but also for its ability to be processed into heat sinks with a thermodynamically optimized geometry. Geometry is one of the critical characteristics of a heat sink. Heat sinks with a maximized surface area and an aerodynamic design can dramatically increase convective cooling performance.
LED Driver
An LED driver regulates the power to the LED light engine. LEDs must be operated on DC power to ensure they are always forward biased to produce light with no visible flickers. LEDs also need to be operated as current driven devices because their light output is determined by the forward current flowing through the junction. LEDs have a forward voltage, below which the forward current will not flow. This forward voltage has a negative temperature coefficient, which means the forward voltage will drop when the LED junction temperature rises. Thus a fixed voltage drive would result in huge fluctuations in the forward current and so the optical output. Furthermore, the self-heating semiconductor device cannot be driven at a current beyond its maximum rated limit. The high electrical stress and concomitant increase in junction temperature are the causes of threading dislocations in highest densities and accelerated atomic defect growth, which lead to permanent lumen depreciation and catastrophic failures of LEDs.The electrical characteristics of LEDs, along with the high efficiency and long life requirements as well as the cost pressure, imposes great challenges to the design of LED drivers. LED drivers that operate LED flood lights are generally designed as switching mode power supplies (SMPS) which draw pulses of current by switching energy storage elements at high frequencies. Switching power supplies have the fundamental advantage of higher efficiencies as the switch regulator operates in saturation and cut-off regions of a switch element such as a MOSFET, and maintains a constant current flow by varying the duty cycle. However, high frequency switching can generate much noise and produce electromagnetic interference (EMI). The additional circuits required for EMI filtering and screening can double the overall cost of the LED driver, which constitutes the largest downside of the SMPS driver solution.
Another inconvenience of the SMPS drivers is their dependence on reactive components, primarily the electrolytic capacitors. Electrolytic capacitors are used as the primary energy storage device to hold up the voltage when powered from a low frequency AC supply. Typically, the lifetime of an LED driver and performance of an LED luminaire are dependent on the quality of the electrolytic capacitor. This component contains electrolyte which gradually evaporates over time. The rate of evaporation can be accelerated by high operating temperature. Every 10°C increase will shorten the life by a factor of two. The loss of electrolyte in an electrolytic capacitor results in reduced holdup time and an increased output voltage ripple and noise. Despite its vulnerability, the electrolytic capacitor is still an indispensable component in LED driver circuits. Its ability to smooth output current ripple is critical for a luminaire to produce flicker-free lighting for HDTV broadcasting applications which impose high frame rate requirements on the lighting. In fact, a high quality electrolytic capacitor can well match the rated life of LED luminaires.
SMPS drivers are the only feasible option for medium to high power lighting solutions for their high efficiency, high quality output, and ability to deal with wide input voltage ranges. However, an increasing number of products are using linear power supplies, an alternative to switching power supplies. Low cost, absence of EMI radiation, and driver-on-board (DOB) design capability are the main appealing points of linear LED drivers. This type of driver circuits utilizes linear regulators to regulate the output power. Linear LED drivers can only step down an input voltage to produce a lower output voltage. A headroom voltage, the minimum voltage differential between the input and output, is required to operate the driver circuit. Unlike an SMPS that switches an energy storage device to regulate the output, linear regulators simply dissipate the headroom voltage to achieve the desired output. This headroom loss causes the linear LED driver to only be 60 to 85 percent efficient, while an SMPS driver can have a power efficiency as high as 98%. The considerable amount of waste power can be a huge financial loss that obviously cannot be compensated by its low initial cost. The efficiency of the LED driver also plays a major role in determining the thermal stresses of the lighting system. Since most linear driving circuits are presented as the DOB design which significantly scales down the sizes of LED flood lights, the heat generated during power regulation introduces a substantial thermal stress to the co-located LEDs. Moreover, linear drivers literally have a number of problems left to be addressed, including limited range of AC input, incapability of galvanic isolation, large output ripple, and poor survivability in overvoltage conditions.
The design specifications of LED drivers also include power factor correction (PFC) which allows the driver to maintain a high power factor over a wide input voltage range while suppressing total harmonic distortion (THD). Various protection features, such as overcurrent, short-circuit, overvoltage and over-temperature protections, should be considered as well to ensure the system reliability.
Lighting Control
LED flood lights can be configured to implement multiple levels of control strategies to maximize energy savings, optimize the quality of light, or create preprogrammed light shows and dynamic effects. LED drivers can be designed to provide dimming capability that allows pulse-width modulation (PWM) or constant current reduction (CCR) dimming with 0-10V, DALI, or DMX controls. These devices can be programmed to interpret control signals from occupancy sensors, daylight harvesting photocells, electronic logic circuits, or remote controllers. Modern controls are generally designed as systems for networked, interactive management of luminaires as a whole, in zones, or individually. The use of wireless mesh network (e.g., via Bluetooth or ZigBee) to monitor performance and operating conditions, and execute advanced light management has seen rapid growth in momentum in recent years.System Protection against Environmental Factors
LED flood lights must be thoroughly sealed and gasketed at all points of entry and material transition to prevent the ingress of moisture, corrosive gases, dust, contaminants and insects. Moisture absorption is one of the common failure mechanisms responsible for premature failures, lumen deprecation and color shift in LED packages. Silicone encapsulant has high moisture permeability and absorbs moisture in atmospheres of high humidity. When subjected to extreme temperature cycling, the presence of moisture known to be the primary causes of the delamination in silicone encapsulant. What's more, corrosive gases can diffuse through silicone encapsulant and lead to corrosion of the metals used in the LED packages. To avoid these extrinsic failures, it is necessary to exercise control of environmental conditions for the light engine and electrical circuits.An IP6x (IP65, IP66, IP67, or IP68) level of ingress protection is required to ensure high enclosure integrity of entire luminaire including light engine and driver/electrical compartment. However, the IP level can drop when the seal is repeatedly stressed by pressure differentials within the enclosure. Pressure differentials are primarily caused by recurrent temperature changes in outdoor environments and are compounded by the high case temperatures of LED luminaires. Repeated expanding and contracting due to the cycling of positive and negative pressure buildups within an airtight enclosure cause seals to fail eventually. To maintain the original IP rating, outdoor LED luminaires typically use a breathing membrane solution which provides a durable barrier against liquid, dust, dirt and other contaminants while allowing air to pass through the membrane for continuous pressure equalization. Pressure equalizers or membrane breathers are usually made of expanded polytetrafluoroethylene (ePTFE) which is a unique, microporous membrane.
The IP rating system
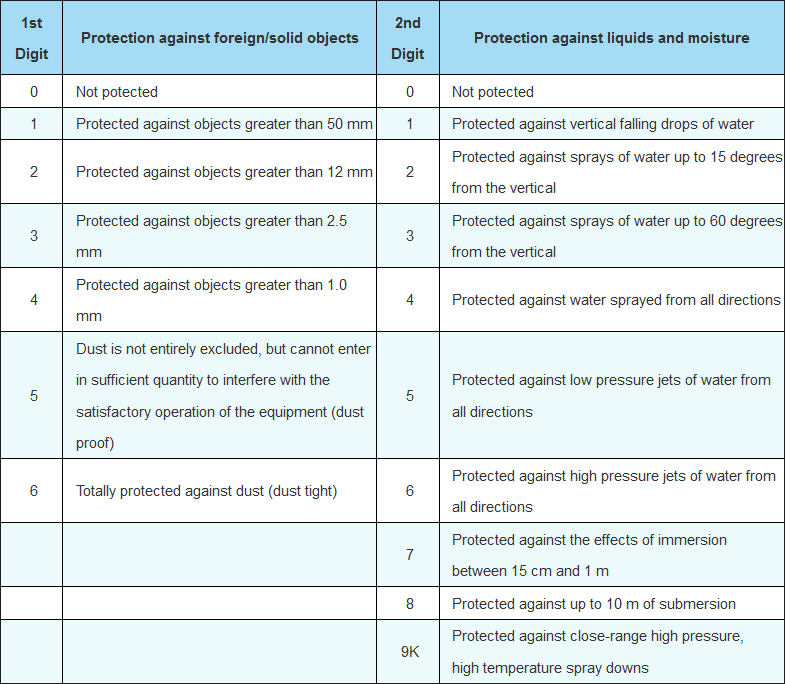
NEMA-to-IP Conversion
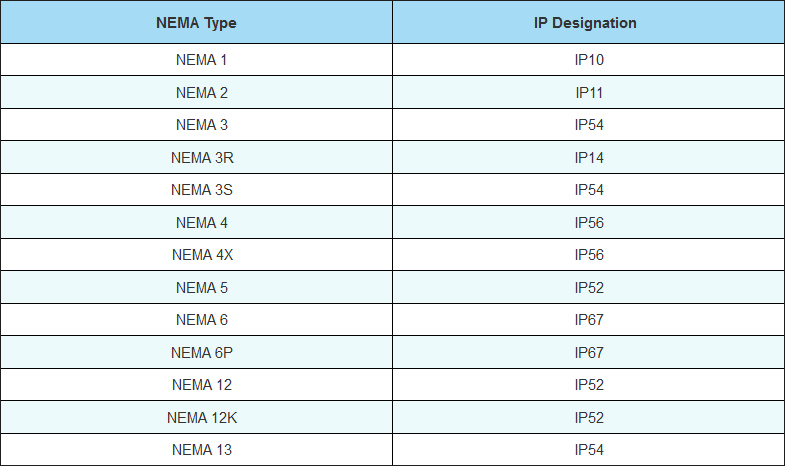
It is a common practice to seal the tempered glass lens to the lens frame by a one-piece silicone gasket. Glass lenses do cause additional optical loss. However, floodlights with exposed polymer (mostly acrylic) optics are more susceptible to dirt depreciation than glass protected luminaires. The luminaire dirt depreciation (LDD) rate is 0.9% per year for floodlights with flat glass outer optics versus 3.0% per year for floodlights with exposed optics. A simple hose-down or a heavy rain can removes the dirt and grime on the glass lens, whereas exposed acrylic optics have poor natural self-cleaning ability and are prone to dirt accumulation over the years.
The aluminum housing of a floodlighting luminaire and other metal parts and accessories that are exposed to the air are electrostatically applied with a durable polyester powdercoat after a multi-stage cleaning, pretreatment and chemical conversion coating process. The power coated surface must be tested to withstand a rated period of salt spray exposure per ASTM B117, to meet scribe creepage rating per ASTM D1654, and to resist UV exposure per ASTM G154.